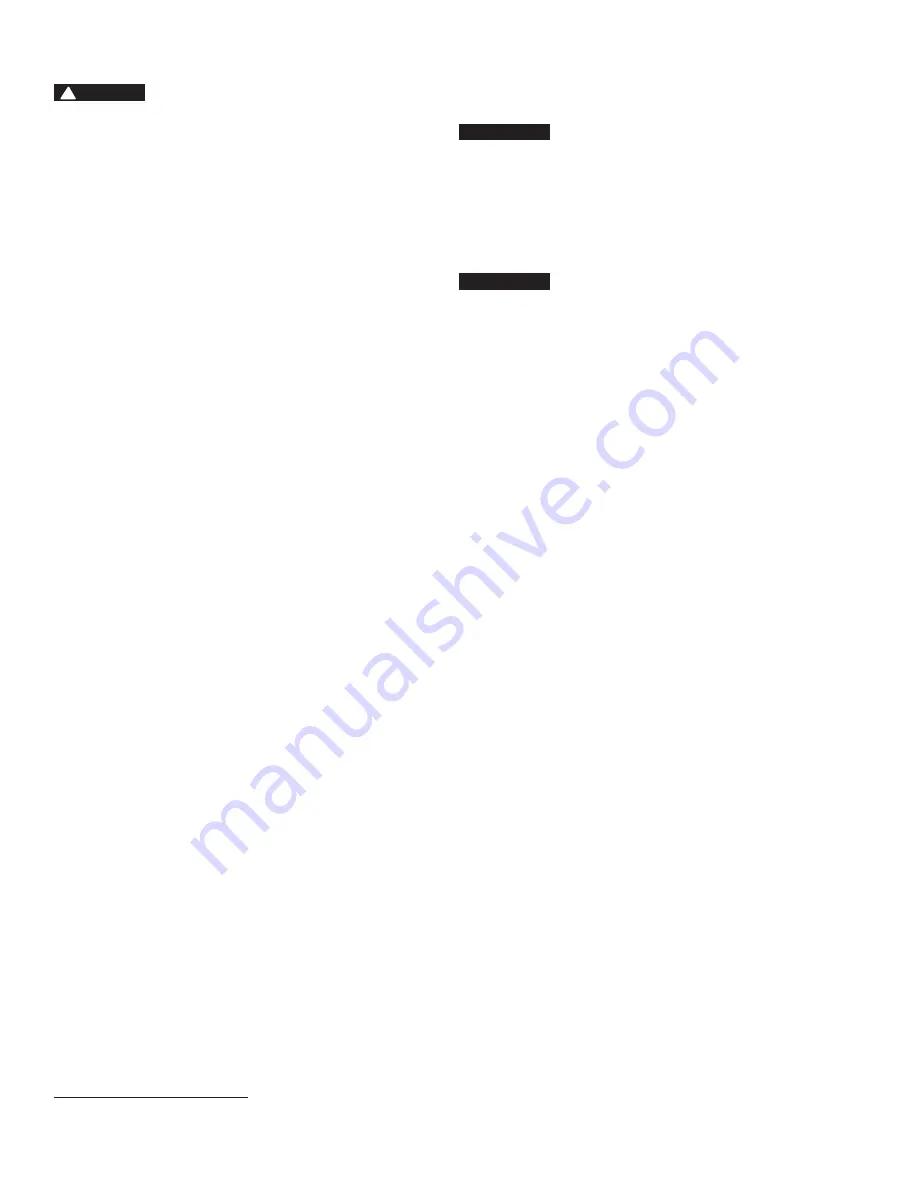
4 PWF Filter Systems
1
Noryl is a trademark of Sabic.
How To Use This Manual
This installation manual is designed to guide the installer through
the process of installing and starting up water conditioning systems
featuring the PWF controller.
This manual is a reference and will not include every system
installation situation. The person installing this equipment should
have:
• Training on the control valve.
• Knowledge of water conditioning and how to determine proper
control settings.
• Adequate plumbing skills.
Control Valve Function and
Cycles of Operation
The time clock control valve has two calendar options for
regeneration frequency: 1. an option where the user can choose the
number of days (1-99) between each backwash; and 2. a seven-
day option where the user can choose which day(s) of the week a
backwash should occur.
The control valve uses no traditional fasteners (e.g. screws); instead
clips, threaded caps and nuts and snap type latches are used.
Caps and nuts only need to be firmly hand tightened because radial
seals are used. Tools required to service the valve include one small
blade screw driver, one large blade screw driver, pliers and a pair of
hands. A plastic wrench is available which eliminates the need for
screwdrivers and pliers. Disassembly for servicing takes much less
time than comparable products currently on the market. Control
valve installation is made easy because the distributor tube can be
cut ½" above to ½" below the top of tank thread. The distributor
tube is held in place by an o-ring seal and the control valve also has
a bayonet lock feature for upper distributor baskets.
The AC adapter power pack comes with a 15 foot power cord and is
designed for use with the control valve. The AC adapter power pack
is for dry location use only. If the power goes out, only the time of
day needs to be reset. All other values are permanently stored in the
nonvolatile memory.
Installation Preview
Conduct a visual check of all equipment for any damage that may
have occurred during shipment.
If there is obvious damage to any equipment, it should be noted
on the carrier’s Bill Of Lading. Open and inspect the contents of all
closed crates, cartons, etc. and inspect for concealed damage. The
manufacturer is not liable for any dam-age during transit.
Position the equipment in its proper location, setting on a flat
surface. Level equipment as required. Equipment out of plumb can
exhibit poor flow characteristics, which will affect the performance of
the system.
Units are shipped with media (resin & gravel), distributions tube, and
control valve installed. Double-check the valve installation on the
tank. Tighten if necessary.
Unit should be positioned with the valve control facing forward.
Check the main line water pressure. The softener is designed for a
minimum of 20 psi and a maximum of 125 psi working pressure. If
the line pressure exceeds this limit, a pressure-reducing valve should
be installed.
Maximum allowable water temperature is 40°F (4°C) – 110°F (38°C).
A 120vac 60 cycle electrical source must be available for operation
of the controller.
Connect raw water supply line to the inlet valve connection. Connect
treated water outlet to service line. It is suggested that the pipe size
be equal or one size larger than the valve connection.
NOTICE
NOTICE
General Warnings (continued)
Installation Guidelines:
seconds. This resets the electronics and establishes the
service piston position. The display should flash all word-
ing, then flash the software version and then reset the
valve to the service position.
• The control valve is compatible with a variety of
regenerants and resin cleaners. The control valve is
capable of routing the flow of water in the necessary paths
to regenerate or backwash water treatment systems. The
injector regulates the flow of brine or other regenerants.
The control valve regulates the flow rates for backwashing,
rinsing, and the replenishing of treated water into a
regenerant tank, when applicable.
• Control valve installation is made easy because the
distributor tube can be cut ½” above to ½” below the top
of tank thread. The distributor tube is held in place by an
o-ring seal and the control valve also has a bayonet lock
feature for upper distributor baskets.
WARNING
!