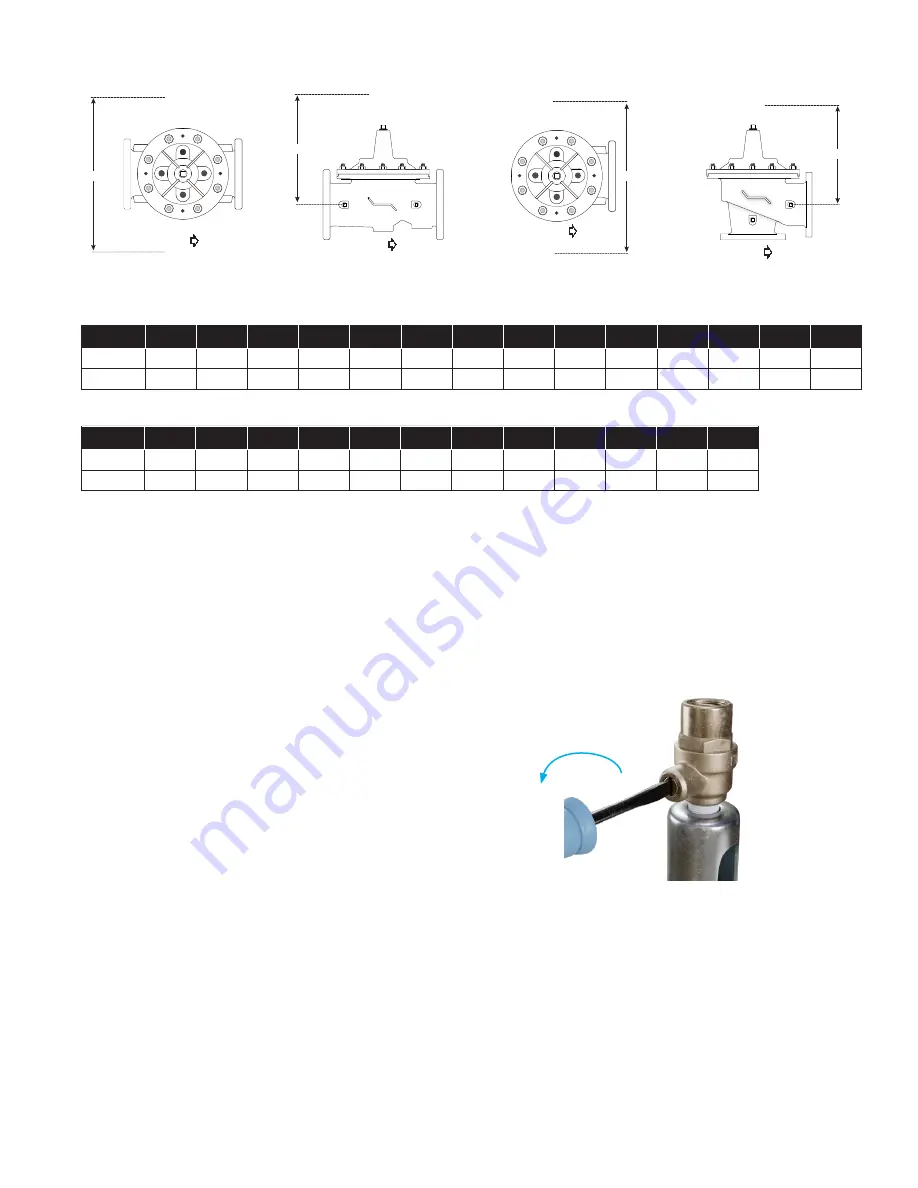
Setting the Altitude Controls
STEP 1
Pre-set pilots as noted:
Altitude Control
– Adjust OUT, counterclockwise, backing pressure off the spring. This simulates a low tank setting which can be grad-
ually increased to the desired setting.
Opening and Closing Speed
– Turn the adjustment screws on the Closing Speed and Opening Speed Controls, if the main valve is so
equipped, OUT, counterclockwise, 1½ to 2½ turns from full closed position.
STEP 2
To ensure proper operation, any trapped air will need to be bled off
the valve cover during startup. The ACV includes a bleed valve, use
a flat head screwdriver to slowly open the valve (See Figure 1).
STEP 3
Pressure the line, by opening the upstream isolation valve slowly. Air
is vented through the air bleed valve. Tighten the fitting when liquid
begins to vent (See Figure 1).
Repeat the process until no air is trapped in the system.
Globe
Angle
Size (in)
1
1/4
1
1/2
2
21/2
3
4
6
8
10
12
14
16
20
24
A (in)
16
16
20
22
22
24
32
34
38
44
48
52
56
56
B (in)
10
10
12
14
14
16
24
26
28
30
34
40
48
48
Size (in)
1
1/4
1
1/2
2
2
1/2
3
4
6
8
10
12
14
16
C (in)
16
16
20
22
22
24
32
34
38
44
48
52
D (in)
10
10
12
14
14
16
24
26
28
30
34
40
The following tables detail the recommended minimum valve servicing dimensions.
A
B
C
FLOW
FLOW
FLOW
D
FLOW
Valve Servicing Dimensions
Counterclockwise to OPEN
bleed valve
Figure 1
Position Indicator
IOM-ACV-127-8_6127-8 2115
EDP# 1917065
© 2021 Watts 3