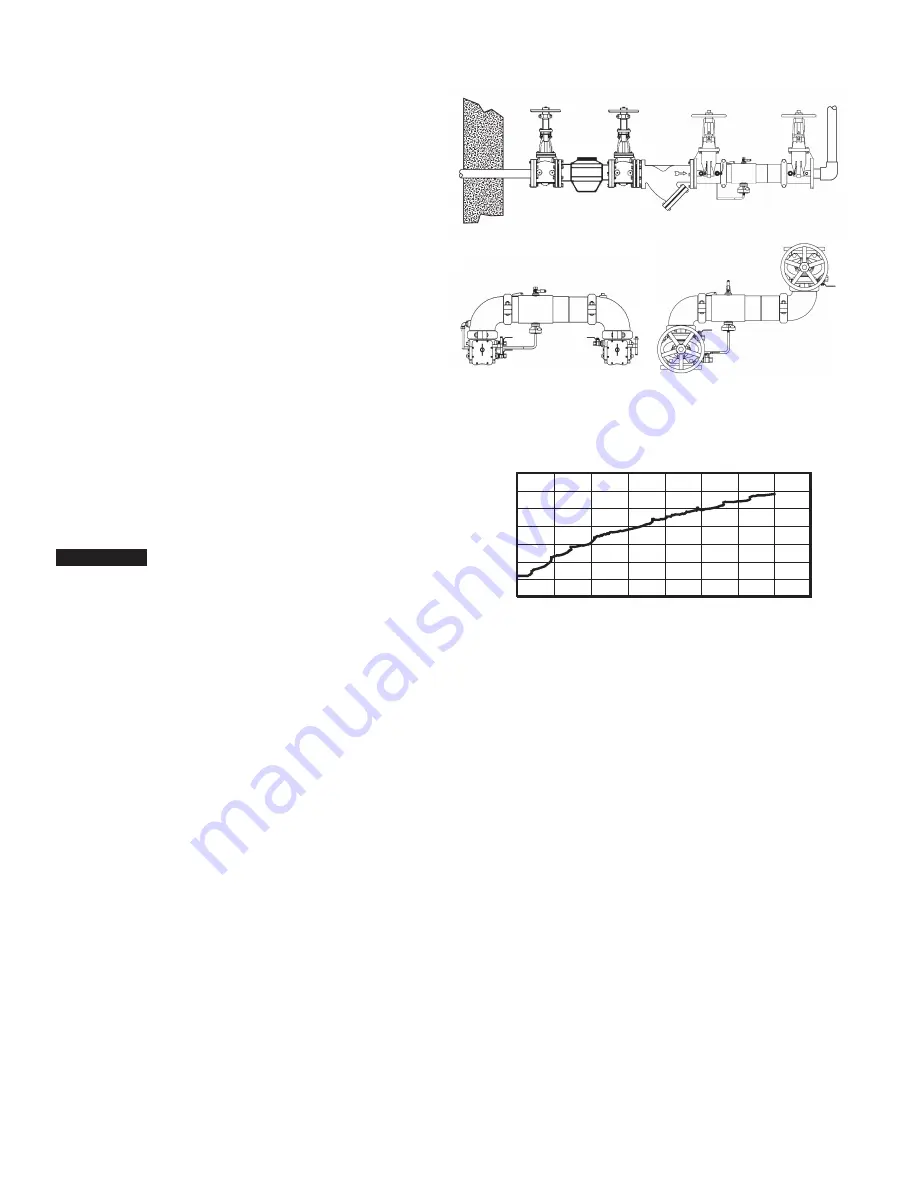
2
• Most field problems occur because dirt and debris are present
in the system at the time of installation and becomes trapped
in check #1. The system should be flushed before the back-
flow valve is installed. If the system is not flushed until after the
backflow valve is installed, remove both check modules from
the valve and open the inlet shutoff to allow water to flow for
a sufficient time to flush debris from the water line. If debris in
the water system continues to cause fouling, a strainer can be
installed upstream of the backflow assembly.
• Series C400-FS, C500-FS, and LFC500-FS can be installed
in either horizontal, “N” pattern, or “Z” pattern position as long
as the backflow assembly is installed in accordance with the
direction of the flow arrow on the assembly and the local water
authority approves the installation.
• The assembly should be installed with adequate clearance
around the valve to allow for inspection, testing, and servicing. A
minimum clearance of 12" should be between the lower portion
of the assembly and the floor or grade. The valve should be
protected from freezing.
• Installing a backflow preventer in a pit or vault is not
recommended.
• Normal discharge and nuisance spitting are accommodated by
the use of an Ames air gap fitting and a fabricated indirect waste
line. Floor drains of the same size must be provided in case of
excessive discharge.
• Series C400, C500, and LFC500 backflow preventers should be
tested by a certified tester at the time of installation.
NOTICE
Assembly body should not be painted.
Installation Guidelines
Relief Valve Discharge Rates 2
1
⁄
2
" – 10"
lpm gpm
1330 350
1140 300
950 250
760 200
570 150
380 100
190 50
0 0
0
20
40
60
80 psi
0
138
276
413
551 kPa
Rate of Flow
Pressure
Horizontal Installation
N Pattern
Z Pattern