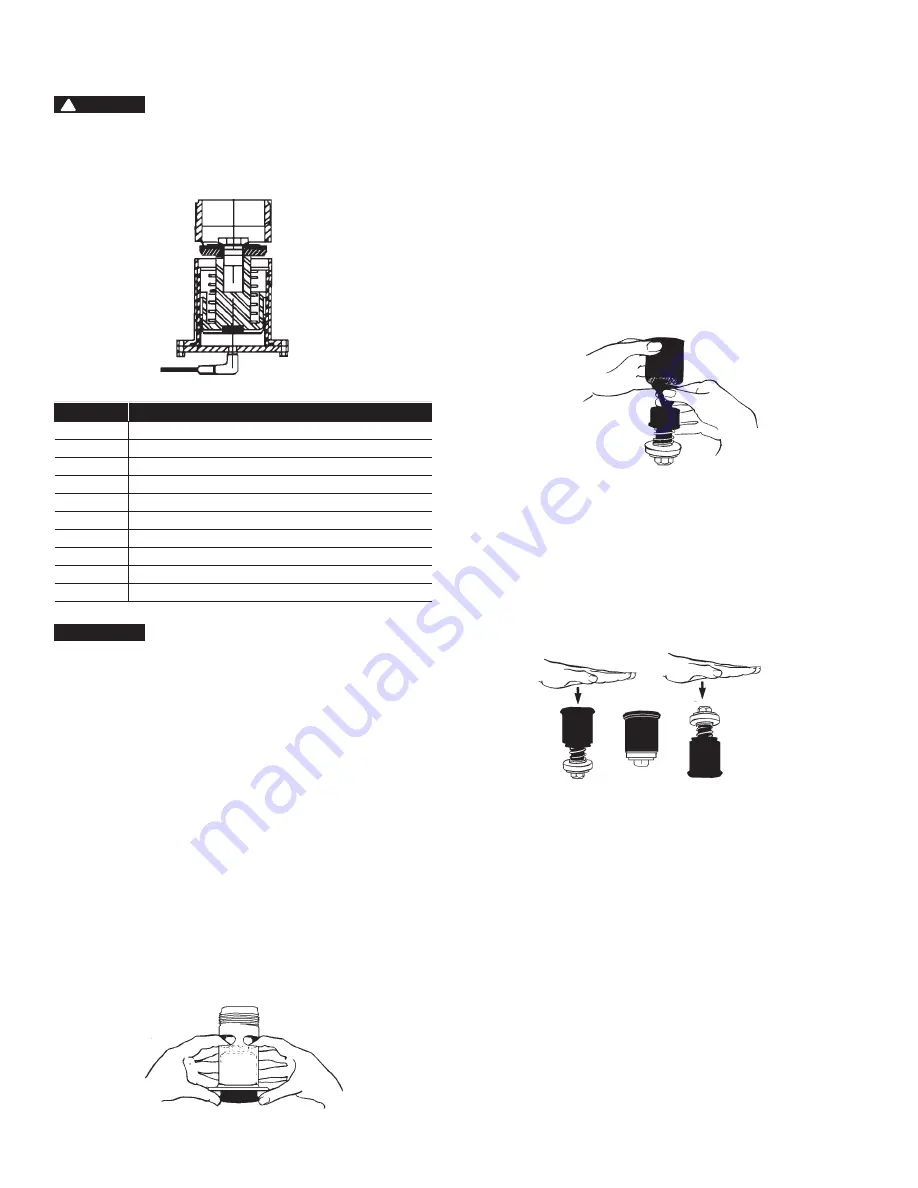
4
Servicing the Relief Valve
WARNING
!
Depressurize valve before servicing.
The relief valve may be serviced while on or off the backflow preventer
valve. (See the components in relief valve in Figure 1.)
ITEM
DESCRIPTION
21
Relief Valve Body
22
Rubber Shutoff Disc
23
Piston Diaphragm Assembly
24
Hex Head Bolt
25
Disc Retainer
26
Sleeve
27
Bottom Bolt
28
Bottom Flange (w st. elbow)
29
Bottom st. elbow
30
O-ring disc
27
21
22
23
24
25
26
28
29
30
6. Grip the sleeve and the piston assembly by the head of the hex
head bolt. Pull up on the sleeve to extend the diaphragm. Slide
the sleeve (item 26) completely off the diaphragm and inspect the
diaphragm for tears, holes, or excessive wrinkles. If the diaphragm
is dam aged, or der a new piston-diaphragm assembly.
To reassemble the relief valve
1. Thoroughly clean all inside surfaces of the relief valve body.
2. Inspect the relief valve body seat surface located at the top edge
of the three discharge slots near the top of the body by rubbing the
end of an index finger around the entire seat surface; access the
seat sur face through the slots or the bottom of the body. The seat
must be free of nicks. If nicks are discovered, remove the body and
install a new relief valve assembly.
3. Position the diaphragm on the piston assembly so that it is fac ing
up. (See Figure 3.)
4. Fold the top (ribbed) edge of the diaphragm inward, grasp the
sleeve with the ribbed edge up, and slide the sleeve down over
the piston assembly.
5. While still holding the sleeve, slide it up over the diaphragm and,
using your thumb and index finger, position the bead of the dia-
phragm so that it wraps over the outside of the rib on the top of
the sleeve so that the sleeve is held by the diaphragm. Place the
piston assembly on a flat, firm surface with diaphragm facing up.
(See Figure 4.)
6. Cup a hand slightly to form an air trap and force the sleeve down
over the piston assembly with a rapid slap (hard) on the open end
of the diaphragm with the cupped hand. The trapped air in the dia-
phragm forces the diaphragm between the inside of the sleeve and
the outside of the piston. Ensure that the diaphragm is fully seated.
If diaphragm is wrinkled, repeat the previous step.
7. Slide the piston assembly and sleeve into the relief valve body
with the hex head bolt entering the flanged end of the body first.
Slide the piston assembly in until the diaphragm lip is smoothly
seated in the ma chined groove in the flanged end of the body.
Run an index finger around the outside of the diaphragm bead to
ensure it is seated smoothly.
8. Position the bottom flange cover on the bottom of the relief valve
body and secure it by hand-tightening the four bottom bolts.
9. Tighten the four bottom bolts to approximately 15 ft-lb with a 5/16"
socket or open-end wrench, then reattach the relief valve hose to
the elbow in the bottom flange cover. Reattach the flood sensor to
the relief valve and mount the activation module to sensor.
NOTICE
Do not use a pipe wrench to remove the relief valve assembly from
the backflow preventer.
To disassemble the relief valve
1. Detach the activation module, if installed, from the flood sensor
then use a #2 Phillips screwdriver to remove the sensor from the
relief valve.
2. Disconnect the relief valve hose from the elbow in the bottom
flange cover at the swivel hose connection. Do not remove the
el bow.
3. If the valve is to be removed from the backflow preventer for
service, place a screwdriver blade or flat bar across the edges of
two of the hex head screws in the bottom flange cover and turn
counterclockwise to loosen the relief valve assembly.
4. Remove the four bottom bolts from the bottom of the relief valve
assembly with a 5⁄16" socket or open-end wrench. Remove the
bottom flange cover.
5. Remove the piston assembly and sleeve from the relief valve body
by placing the index fingers through the slots in the side of the
body and pressing down on the top of the disc retainer in the top
of the piston assembly. (See Figure 2.) Pull the piston assembly
free of the body by grasping the sleeve and pulling down.
Figure 2
Figure 3
Figure 1
Figure 4