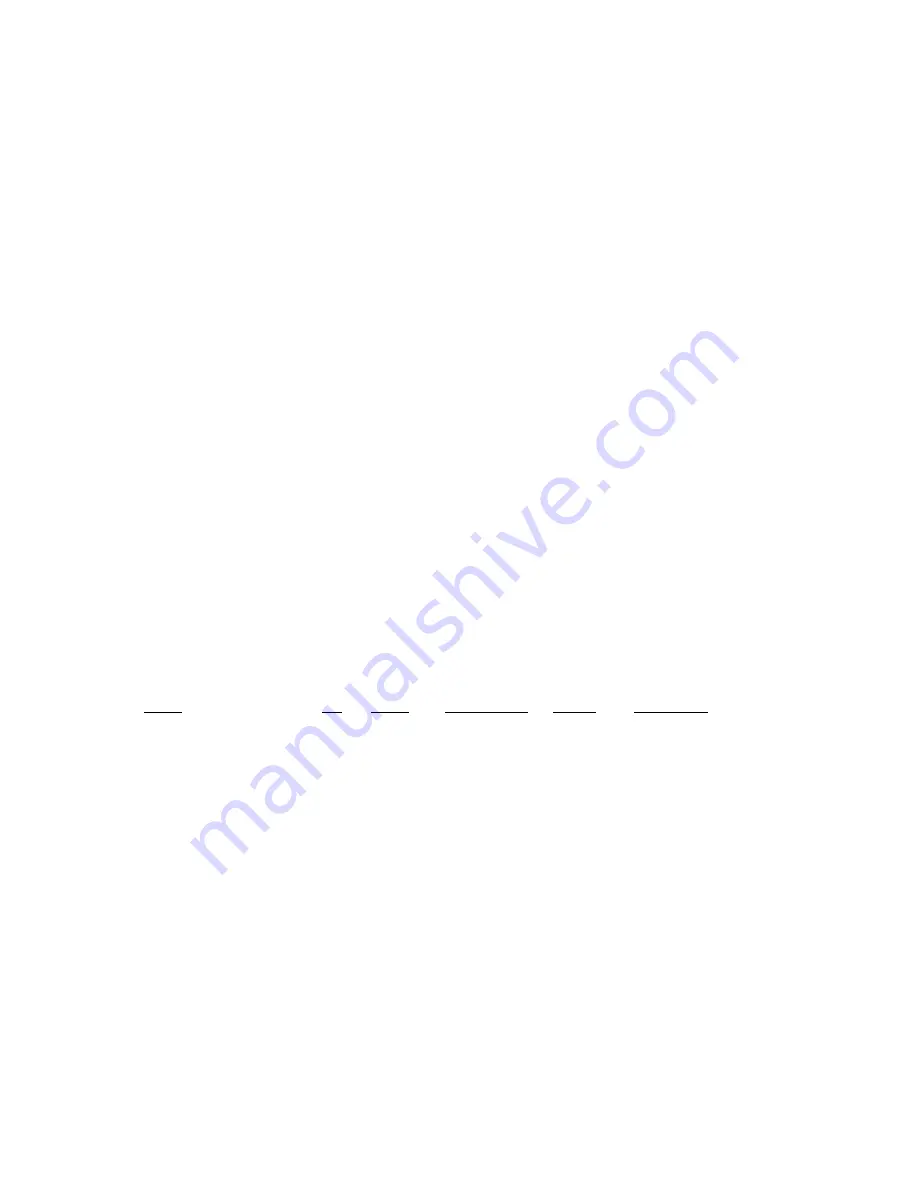
Watson Industries, Inc.
DMS-SGP02 Rev K 03/22/2018
10
Note: It is possible for both the “:” and the “+” commands to be active at the same time.
The “+” command determines whether the sensor is allowed to transmit data. So in this
case, the “:” command must also be turned off to allow the free flow of data.
11.
The “&” command calls a menu which allows any of several parameters to be set. From
this menu, the user can change system time constants, data channels for serial output,
heading source, velocity source and baud rate. Command mode is required for access to
this command.
There are two output format commands: “_” for decimal output and “^” for binary. See second part
of Appendix A for more information on changing output formats. There are several interface
commands as well: “:” will toggle the output to send a frame of data upon receiving any non-
command character and “+” will toggle the output for no output data. These and other changes
can be made permanent by keying in the quote (“) character.
The commands “~”, “@”, “#”, “$”, ‘(“, “)”, “{“, “}”, “|”, “<”, “>”,“?” and “S” are used by the
Watson factory to calibrate the unit and should be used only with the assistance of the factory. If
an undesired function is called, a “Q”, and sometimes Escape or a Delete will interrupt the
command and return to operation with the least disturbance to the system. All other unspecified
characters such as carriage return, line feed and space are ignored by the system.
If there are problems with the system “hanging up” during the binary output mode, check for cross
talk between the serial transmit and receive line in your installation. In addition, check to see that
the communications program used is not sending an echo. This will not happen in the decimal or
hexadecimal modes because command characters recognized by the system are not produced in
those modes. Please note that the signal and power ground are isolated from one another.
Analog Outputs
Analog signals are output from a 14 bit digital to analog converter through an operational amplifier.
Each analog output has a 300 ohm resistor in series to eliminate oscillations from high capacitance
loads. The output range for all of the analog output channels is
±
10 Volts with respect to the
common signal ground. The outputs include:
Signal
Pin
Range
Output Range
0 VDC
Scale Factor
Bank
14
±
180
°
±10V
0°
18°/s/V
Elevation
15
±
90
°
±5V
0°
18°/s/V
Heading
16
0-360
°
±10V
0° (North)
18°/s/V
Roll Rate (X Axis)
23
±
100
°
/s
±10V
0°/s
10°/s/V
Pitch Rate (Y Axis)
24
±
100
°
/s
±10V
0°/s
10°/s/V
Yaw Rate (Z Axis)
25
±
100
°
/s
±10V
0°/s
10°/s/V
X Acceleration
17
±
10g
±10V
0g
1g/V
Y Acceleration
18
±
10g
±10V
0g
1g/V
Z Acceleration
19
±
10g
±10V
0g
1g/V
Forward Acceleration
20
±
10g
±10V
0g
1g/V
Lateral Acceleration
21
±
10g
±10V
0g
1g/V
Vertical Acceleration
22
±
10g
±10V
0g
1g/V
Analog Inputs
In an effort to make this system more versatile, the DMS allows the user to input analog data that
can then be added to the serial data output. This allows the system to act as a data acquisition unit
for other vehicle information such as engine RPM, engine temperature, fuel remaining,