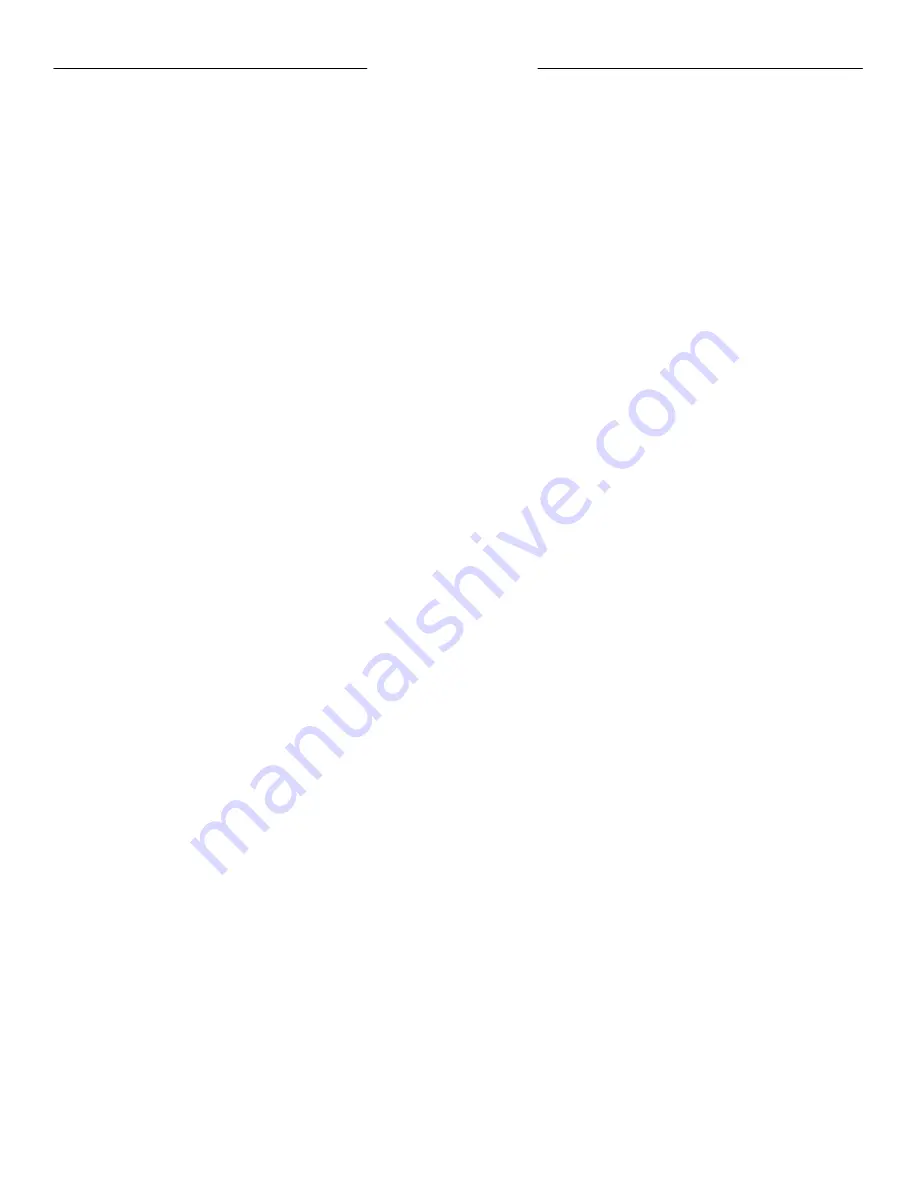
F
−
1031, Section 2407
Page 3 of 8
Introduction
System Overview
NOTE: Read and understand the operating instruc-
tions for the Foam Manager System prior to operating.
(Refer to Figure 1 for system components.)
The Foam Manager
t
System consists of an Advantus
t
Foam Management System mounted on a Waterous CM
or CS fire pump.
Advantus
t
3/6 Foam Management System
The ADVANTUS
t
foam system uses advanced conductiv-
ity
−
based technology to monitor both supply water and
foam solution in order to deliver optimal foam at every call.
Regardless of the foam concentrate or the quality of the
water being pumped, the ADVANTUS automatically adjusts
for both, providing you with the most accurate fire suppres-
sion capabilities in the industry.
Foam Pump
The 12 or 24
−
volt electric motor driven, Hydra
−
Cell positive
displacement foam concentrate pump is constructed of
brass and stainless steel components which may come in
contact with foam concentrate, making the pump resistant
to chemical and corrosive attack. The pump is capable of
handling suspended abrasives without sustaining any dam-
age and can run dry for extended periods without sustain-
ing damage.
The foam pump for the Advantus 3 is rated at 3 GPM (11.3
l/min) at 150 psi (10 bar) and 6 GPM (22.6 l/min at 150 psi
(10 bar) for the Advantus 6, with operating pressures up to
450 psi (32 bar). The system draws a maximum electrical
load of 40 amps @ 12 VDC or 21 amps @ 24 VDC (Ad-
vantus 3) or 80 amps @ 12 VDC or 40 amps @ 24 VDC
(Advantus 6).
A pump motor electronic driver, located inside the controller
housing receives signals from the microcontroller and
powers the electric motor in a variable speed duty cycle to
ensure that the correct amount of foam concentrate as set
by the pump operator is injected into the water stream.
Process Manifold
The foam system process manifold, constructed of stain-
less steel with Victaulic
®
groove connections provided at
each end of the manifold for connection to the apparatus
plumbing. The process manifold includes an incoming
water conductivity probe, paddlewheel flowmeter, foam
injection check valve, Akron Brass
®
waterway check valve
and foam solution conductivity probe. An Akron full
−
flow
brass body check valve in the foam process manifold
waterway prevents foam contamination of fire pump and
water supply. A brass and stainless steel check valve
provided in the foam concentrate line at the foam injection
point to prevents water backflow into the foam supply res-
ervoir(s). Stainless steel conductivity probes include gap
spacers and a reverse charge feature to prevent build
−
up
of deposits on the probe surfaces.
The system also incorporate a sensor to measure water
temperature to ensure the proper amount of concentrate is
injected.