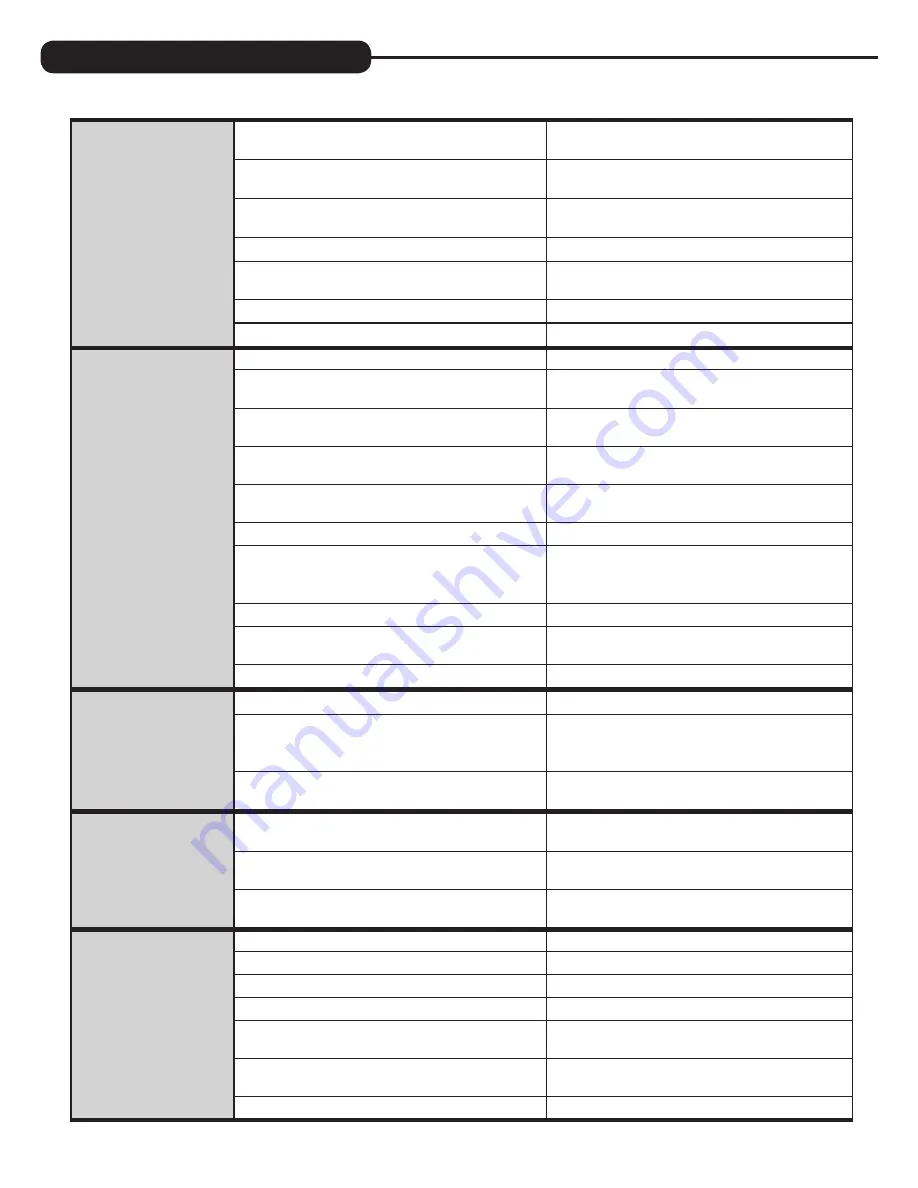
14
7. Control valve does not
regenerate automatically
but does when the correct
button(s) is depressed and
held. For timeclock valves
the buttons are
▲
&
▼
.
For all other valves the
button is REGEN.
A. Bypass valve in bypass position
A. Turn bypass handles to place bypass in
service position
B. Meter is not connected to meter connection on PC
board
B. Connect meter to three pin connection labeled
METER on PC board
C. Restricted/stalled meter turbine
C. Remove meter and check for rotation or
foreign material
D. Incorrect programming
D. Check for programming error
E. Meter wire not installed securely into three
pin connector
E. Verify meter cable wires are installed securely into
three pin connector labeled METER
F. Defective meter
F. Replace meter
G. Defective PC board
G. Replace PC board
8. Hard or untreated water
is being delivered
A. Bypass valve is open or faulty
A. Fully close bypass valve or replace
B. Media is exhausted due to high water usage
B. Check program settings or diagnostics for abnormal
water usage
C. Meter not registering
C. Remove meter and check for rotation or
foreign material
D. Water quality fluctuation
D. Test water and adjust program
values accordingly
E. No regenerant or low level of regenerant in
regenerant tank
E. Add proper regenerant to tank
F. Control fails to draw in regenerant
F. Refer to Troubleshooting Guide number 12
G. Insufficient regenerant level in regenerant tank
G. Check refill setting in programming. Check refill
flow control for restrictions or debris and clean or
replace
H. Damaged seal/stack assembly
H. Replace seal/stack assembly
I. Control valve body type and piston type
mix matched
I. Verify proper control valve body type and
piston type match
J. Fouled media bed
J. Replace media bed
9. Control valve uses too
much regenerant
A. Improper refill setting
A. Check refill setting
B. Improper program settings
B. Check program setting to make sure
they are specific to the water quality and
application needs
C. Control valve regenerates frequently
C. Check for leaking fixtures that may be exhausting
capacity or system is undersized
10. Residual regenerant
being delivered to
service
A. Low water pressure
A. Check incoming water pressure – water pressure
must remain at minimum of 25 psi
B. Incorrect, damaged, or restricted injector
B. Replace injector with correct size for
the application
C. Restricted drain line
C. Check drain line for restrictions or debris
and clean
11. Excessive water in
regenerant tank
A. Improper program settings
A. Check refill setting
B. Plugged injector
B. Remove injector and replace
C. Drive cap assembly not tightened in properly
C. Re-tighten the drive cap assembly
D. Damaged seal/stack assembly
D. Replace seal/stack
E. Restricted or kinked drain line
E. Check drain line for restrictions or debris and or
unkink drain line
F. Plugged backwash flow controller
F. Remove backwash flow controller and clean
or replace
G. Missing refill flow controller
G. Replace refill flow controller
PROBLEM
CAUSE
CORRECTION
TROUBLESHOOTING GUIDE
Содержание CareSoft Elite RC Twin
Страница 7: ...7 This page intentionally left blank...
Страница 22: ...22 REPLACEMENT PARTS...
Страница 30: ...30 This page intentionally left blank...