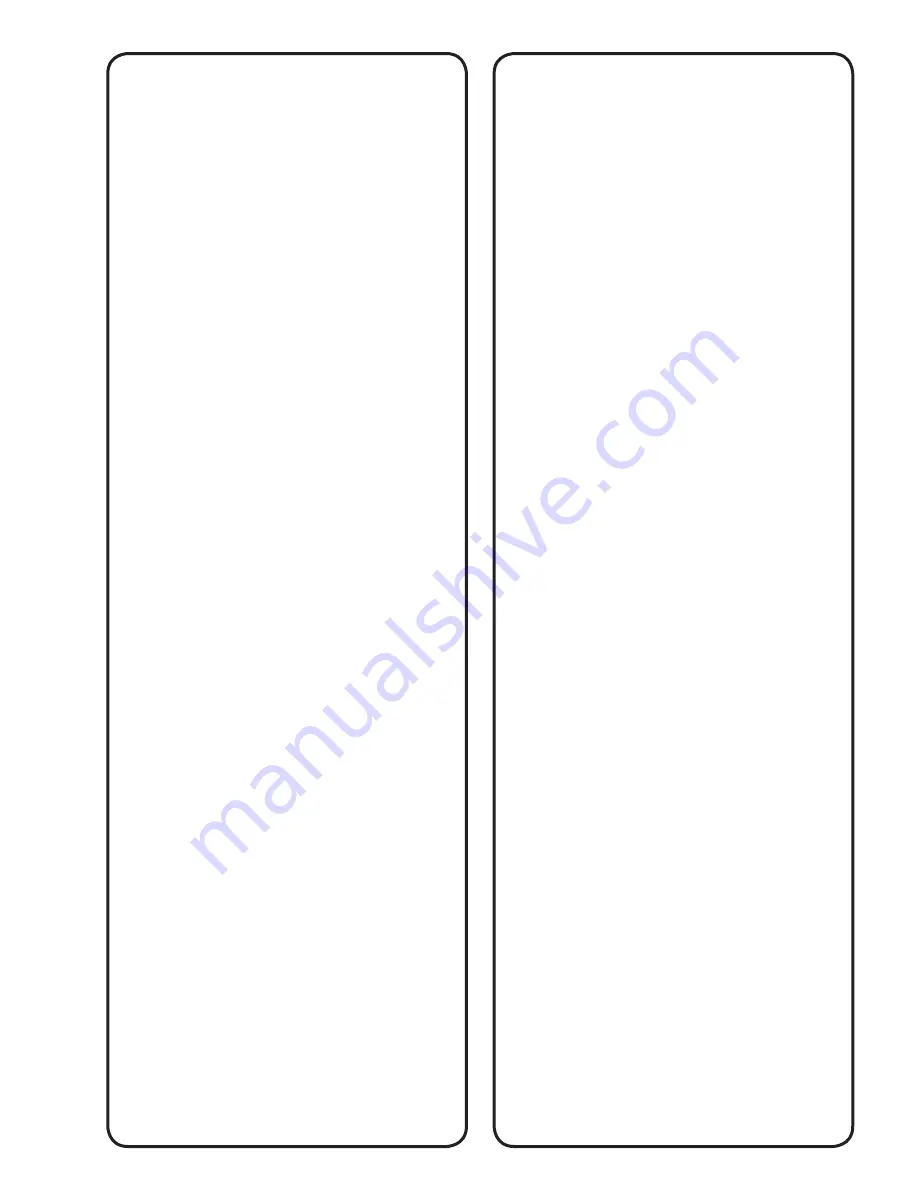
30119-16 Rev. 4.9/07-09
5
6. SEPARATOR/SUPPORT SPINDLE ASSEMBLY
(#12)
can be removed for replacement by removing the
four mounting screws (#13) which thread into the gear-
box. Separator O-ring (#14) should be replaced and the
new O-ring (#14) covered with a thin coat of silicone
grease. The separator/support spindle assembly (#12) can
then be replaced in the front of the gearbox (#16) with a
firm push, gently rotating the assembly at the same time.
Replace and tighten the four mounting screws (#13).
VII. REASSEMBLING METER
1. PROPELLER
INSTALLATION
is accomplished by
following these steps:
a)
The reverse thrust cartridge set screw (#7)
should be protruding out of the reverse thrust bearing
cartridge so it will not bind up on the spindle thread.
Note:
Look through the end of the propeller and
hole in the reverse thrust cartridge to be sure the
set screw is not showing.
b)
Slide the propeller assembly onto the support
spindle (#12) until the reverse thrust bearing car-
tridge (#6) contacts the threads on the end of the
spindle (#12). Using Tool T-2402X-1, thread the
reverse thrust bearing cartridge onto the spindle. If
you feel any resistance when threading the reverse
thrust cartridge on, stop at once and check to be
sure the set screw is not binding on the thread. Be
careful not to cross-thread the reverse thrust bearing
cartridge.
c)
Thread the reverse thrust bearing cartridge (#6)
onto the spindle (#12) until the trailing edge of the
propeller contacts the gearbox (#16). Set the proper
end play by inserting a 5/64” allen wrench into the
reverse thrust bearing set screw (through the side of
the propeller) and loosening the reverse thrust bear-
ing cartridge (#6) one half turn counterclockwise.
d)
Tighten the set screw in reverse thrust bearing
cartridge. There should be approximately .02” clear-
ance between the gearbox (#16) and trailing edge
of the propeller when the propeller in pulled forward
(away from the gearbox). The propeller must not
contact the gearbox.
2. THRUST BEARING CARTRIDGE ASSEMBLY (#5)
should be inspected for damage and replaced in the nose
of the propeller. The thrust bearing cartridge (#5) is used
to adjust the amount of longitudinal end play of the propel-
ler assembly on its spindle (#12), which should be about
1/64 inch. End play can be adjusted by turning the thrust
bearing cartridge assembly (#5) clockwise until it tightens
against the end of the support spindle (#12), then turning
thrust bearing cartridge (#5) counterclockwise 1/8 of a
turn. Tighten set screw (#3). Check the longitudinal end
play of the propeller to ensure it’s not excessive and does
not allow the propeller (#2) to contact the gearbox (#16).
Check the clearance between the propeller (#2) and
gearbox (#16). The clearance should be approximately
.01” between the gearbox (#16) and trailing edge of the
propeller when the propeller in pushed back (toward the
gearbox). The propeller assembly (#1) must spin freely.
3. PROPELLER BEARING (#8)
can be checked for
excessive radial play by rocking the propeller (#2) gently
from side to side on the spindle (#12). Some play is
required for proper operation of the water lubricated
ceramic sleeve bearing.
VIII. SENSOR AND FC101 DIGITAL INDICATOR-TOTAL-
IZER
1. FC101 DIGITAL INDICATOR (#34)
should not be
removed from the meter unless battery or sensor replace-
ment is required. If the unit must be removed, proceed
as follows:
2. FC101
(#34)
can be removed from meter head by
removing the four screws (#32), then slightly lifting unit
up and turning over to disconnect the 2-lead sensor wires
from the bottom of the FC101. If the meter is equipped
with a transmitter, the transmitter wires must also be
disconnected.
3. SENSOR
HOUSING
should be removed only if re-
placement is necessary. The sensor can be taken out of
the separator after removing the gearbox backplate (#17).
Once the backplate is removed, pull the sensor wire and
sensor assembly out the back of the gearbox.
4. BEFORE REPLACING THE SENSOR
be sure the
separator is dry. Slide sensor housing and wire assem-
bly into the separator until it stops against the inside of
separator.
Note:
It does not make any difference what
rotation position sensor is installed; however, wire must
be positioned toward back (open end) of separator. Feed
the sensor wire up through the gearbox and out the meter
head.
5. LITHIUM
BATTERY
should offer 6 to 10 years of
operation. The FC101 has a low battery display that comes
on when approximately six months of life is remaining.
The battery should test at least 2.8 to 3.6 volts to be
considered good.
NOTE: Batteries should be disposed
of in an environmentally safe manner.
6. THE FC101 DIGITAL INDICATOR-TOTALIZER
(#34) can now be installed in one of four positions for
more convenient reading with four screws (#32).
IX. PRIOR TO INSTALLING METER
1. PROPELLER ASSEMBLY (#1)
should be dipped in
water to lubricate the propeller ceramic sleeve bearing
(#8). Spin the propeller (#2) gently to make certain the
meter operates smoothly and no bind or drag is appar-
ent.
Содержание LP04D
Страница 7: ...30119 16 Rev 4 9 07 09 7 NOTES...