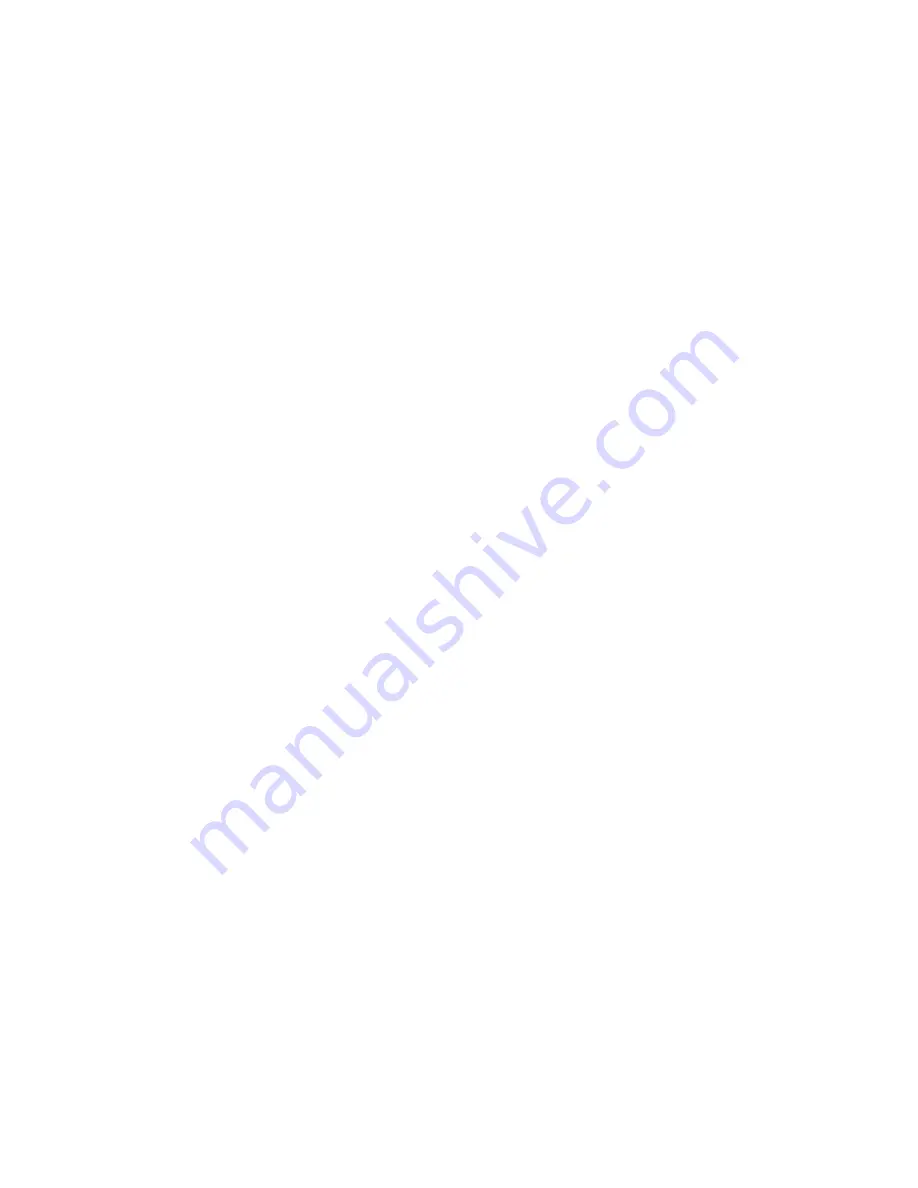
6
General Warnings
The control valve, fittings and/or bypass are designed to accommodate minor plumbing misalignments but are not designed to sup-
port the weight of a system or the plumbing.
Do not use Vaseline, oils, other hydrocarbon lubricants or spray silicone anywhere. A silicone lubricant may be used on black o-
rings but is not necessary.
Avoid any type of lubricants, including silicone, on the clear lip seals.
The nuts and caps are designed to be unscrewed or tightened by hand or with the special plastic wrench. If necessary a pliers can
be used to unscrew the nut or cap. Do not use a pipe wrench to tighten or loosen nuts or caps. Do not place a screwdriver in the
slots on caps and/or tap with a hammer.
Do not use pipe dope or other sealants on threads. Use Teflon tape on the threaded inlet, outlet and drain fittings. Teflon tape is not
necessary on the nut connection or caps because of o-ring seals.
After completing any valve maintenance involving the drive assembly or the drive cap assembly and pistons, unplug power source
jack from the printed circuit board (black wire) and plug back in or:
For valves that use a TC circuit board (three buttons) press and hold SET and DOWN buttons for 3 seconds. The cover button
may have other names like “SET HOUR”, “CLOCK” or “SET CLOCK” but the circuit board is labeled with SET.
For all other valves press and hold NEXT and REGEN buttons for 3 seconds.
This resets the electronics and establishes the service piston position. The display should flash all wording, then flash the software
version, and then reset the valve to the service position.
All plumbing should be done in accordance with local plumbing codes. The pipe size for the drain line should be a minimum of ½”.
Backwash flow rates in excess of 7 gpm (26.5 lpm) or length in excess of 20’ (6.1m) require ¾” drain line.
Solder joints near the drain must be done prior to connecting the drain line flow control fitting. Leave at least 6” between the drain
line control fitting and solder joints when soldering pipes that are connected on the drain line control fitting. Failure to do this could
cause interior damage to the drain line flow control fitting.
When assembling the installation fitting package (inlet and outlet), connect the fitting to the plumbing system first and then attach
the nut, split ring and o-ring. Heat from soldering or solvent cements may damage the nut, split ring, or o-ring. Solder joints should
be cool and solvent cements should be set before installing the nut, split ring, and o-ring. Avoid getting primer and solvent cement
on any part of the o-rings, split rings, bypass valve, or control valve.
Plug into an electrical outlet. Note: All electrical connections must be connected according to local codes. (Be certain the outlet is
uninterrupted.)
Install grounding strap on metal pipes.
Control Valve Function and Cycles of Operation
This glass filled Noryl (or equivalent) fully automatic control valve is designed as the primary control center to direct and regulate all
cycles of a water softener or filter. When the WS1 control valve is manufactured as a softener, the control valve can be ordered to
perform downflow or upflow regeneration. The WS1.25 control valve is only available in downflow regeneration. When the WS1 or
WS1.25 control valve is set up as a filter, the control valve can be set to perform downflow regeneration or simply backwash. The
control valve can be set to regenerate on demand (consumption of a predetermined amount of water) and/or as a time clock
(passage of a particular number of days). The control valve can be set so that a softener can meet the Water Quality Association
(WQA) Standard S100 or NSF/ANSI Standard 44 efficiency rating.
It is not recommended to change control valves from downflow to upflow brining or vice versa in the field. The valve bod-
ies for downflow and upflow are unique to the regeneration type and should not be interchanged. A mismatch of valve
body and regeneration piston will result in hard water bypass during service.
The control valve is compatible with a variety of regenerants and resin cleaners. The control valve is capable of routing the flow of
water in the necessary paths to regenerate or backwash water treatment systems. The injector regulates the flow of brine or other
regenerants. The control valve regulates the flow rates for backwashing, rinsing, and the replenishing of treated water into a regen-
erant tank, when applicable.
The control valve uses no traditional fasteners (e.g. screws); instead clips, threaded caps and nuts and snap type latches are used.
Caps and nuts only need to be firmly hand tightened because radial seals are used. Tools required to service the valve include one
small blade screw driver, one large blade screw driver, pliers, and a pair of hands. A plastic wrench is available which eliminates the
need for screwdrivers and pliers. Disassembly for servicing takes much less time than comparable products currently on the market.
Control valve installation is made easy because the distributor tube can be cut ½” above to ½” below the top of tank thread. The
distributor tube is held in place by an o-ring seal and the control valve also has a bayonet lock feature for upper distributor baskets.
The AC adapter power pack comes with a 15 foot power cord and is designed for use with the control valve. The AC adapter power
pack is for dry location use only. The control valve remembers all settings until the battery power is depleted if the power goes out.
After the battery power is depleted, the only item that needs to be reset is the time of day; other values are permanently stored in
the nonvolatile memory. The control valve battery is not rechargeable but is replaceable.