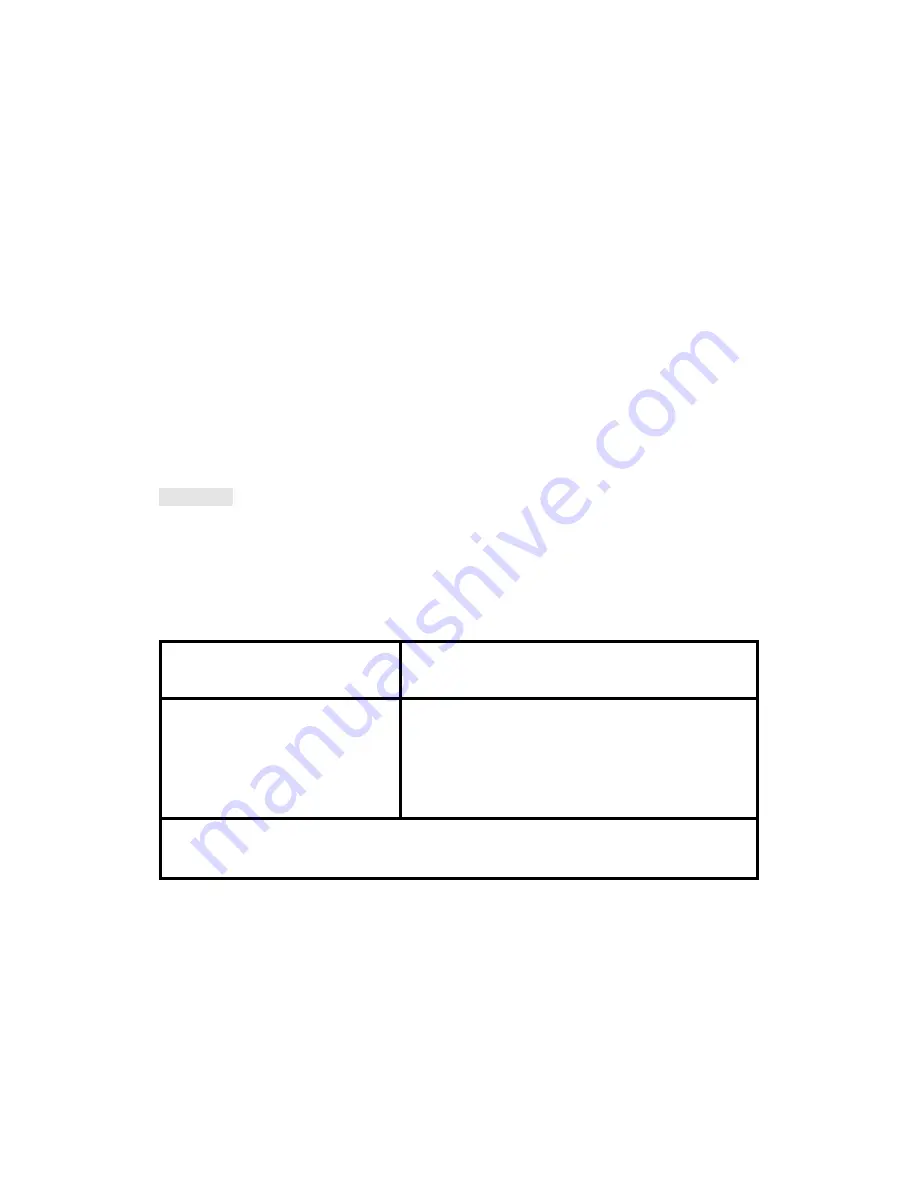
WARNING: ALL OPERATING AND MAINTENANCE PROCEDURES SHOWN ON THE NEXT
PAGE OF THIS MANUAL MUST BE FOLLOWED DAILY FOR PROPER OPERATION OF
YOUR WASCOMAT MACHINE.
PLEASE ENTER THE FOLLOWING INFORMATION AS IT APPEARS ON THE WASHER
DATA PLATE LOCATED AT TOP LEFT OF THE REAR PANEL. SERIAL NUMBER IS ALSO
LOCATED ON A STICKER ON THE INSIDE OF THE DOOR.
MAKE CERTAIN TO KEEP THIS MANUAL IN A SECURE PLACE FOR FUTURE
REFERENCE.
MACHINE TYPE OR MODEL
MACHINE SERIAL NUMBER(S)
ELECTRICAL CHARACTERISTICS: ________ VOLTS, _______ PHASE, ______ HZ.
OPERATING & MAINTENANCE MANUAL
WASCOMAT
W75ES – W105ES – W125ES – W185ES
EMERALD SERIES
471 1562-66/01
95.32