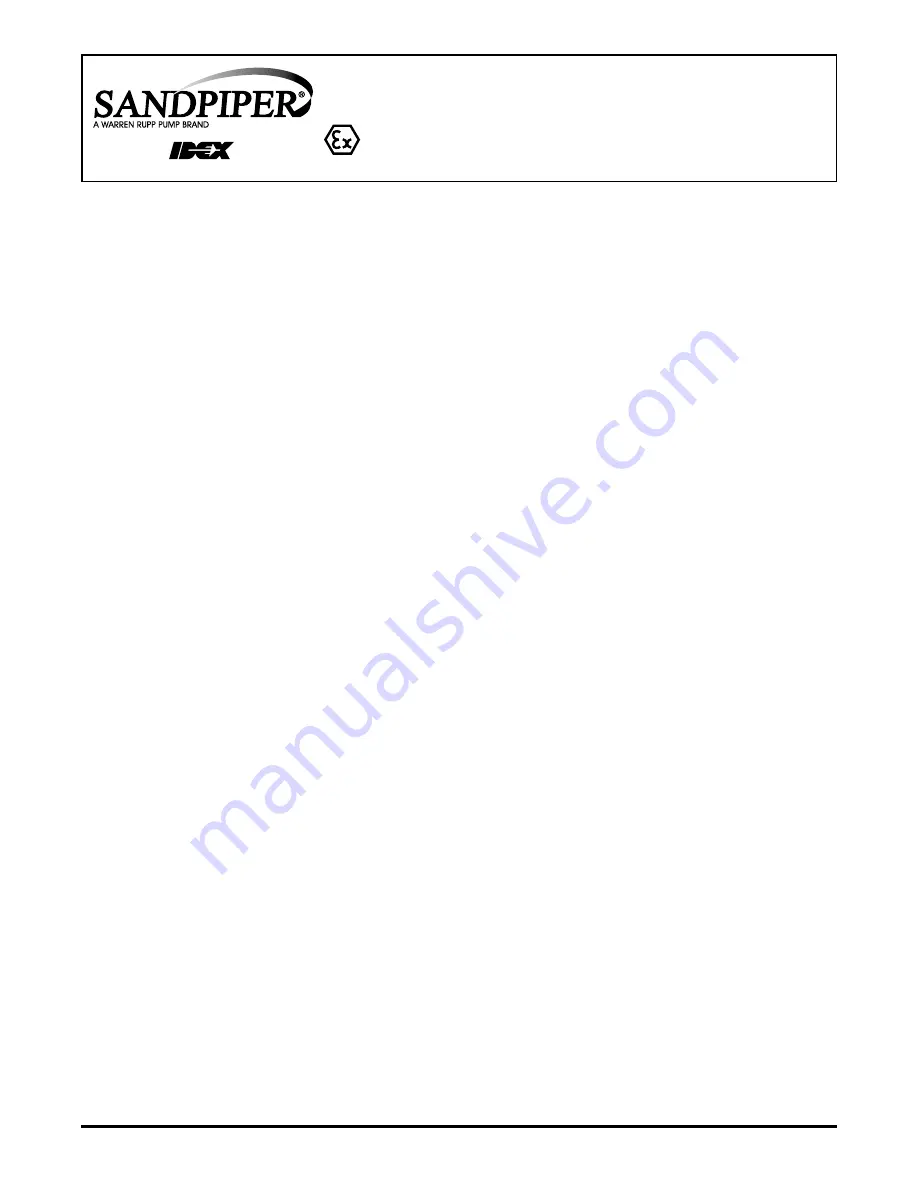
msa3dl7sm-REV0317
Models MSA3 Page 1
PRINCIPLE OF PUMP OPERATION
This flap swing check valve pump is powered by compressed air and is a 1:1
pressure ratio design. It alternately pressurizes the inner side of one diaphragm
chamber, while simultaneously exhausting the other inner chamber. This causes the
diaphragms, which are connected by a common rod, to move endwise. Air pressure
is applied over the entire surface of the diaphragm, while liquid is discharged from
the opposite side. The diaphragm operates under a balanced condition during the
discharge stroke, which allows the unit to be operated at discharge heads over
200 feet (61 meters) of water head.
Since the diaphragms are connected by a common rod, secured by plates to the
center of the diaphragms, one diaphragm performs the discharge stroke, while the
other is pulled to perform the suction stroke in the opposite chamber.
For maximum diaphragm life, keep the pump as close to the liquid being pumped
as possible. Positive suction head in excess of 10 feet of liquid (3.048 meters) may
require a back pressure regulating device. This will maximize diaphragm life.
Alternate pressuring and exhausting of the diaphragm chamber is performed
by means of an externally mounted, pilot operated, four-way spool type air
distribution valve. When the spool shifts to one end of the valve body, inlet air
pressure is applied to one diaphragm chamber and the other diaphragm chamber
exhausts. When the spool shifts to the opposite end of the valve body, the porting of
chambers is reversed. The air distribution valve spool is moved by an internal pilot
valve which alternately pressurizes one side of the air distribution valve spool, while
exhausting the other side. The pilot valve is shifted at each end of the diaphragm
stroke by the diaphragm plate coming in contact with the end of the pilot valve
spool. This pushes it into position for shifting of the air distribution valve.
The chambers are manifolded together with a suction and discharge check valve
for each chamber, maintaining flow in one direction through the pump.
INSTALLATION & START-UP
Locate the pump as close to the product being pumped as possible, keeping
suction line length and number of fittings to a minimum. Do not reduce line size.
For installations of rigid piping, short flexible sections of hose should be installed
between pump and piping. This reduces vibration and strain to the piping system.
A Warren Rupp Tranquilizer
®
Surge Suppressor is recommended to further reduce
pulsation in flow.
This pump was tested at the factory prior to shipment and is ready for operation.
It is completely self-priming from a dry start for suction lifts of 20 feet (6.096 meters)
or less. For suction lifts exceeding 20 feet of liquid, fill the chambers with liquid
prior to priming.
AIR SUPPLY
Air supply pressures cannot exceed 125 psi (8.61 bar). Connect the pump
air inlet to an air supply of sufficient capacity and pressure required for desired
performance. When the air line is solid piping, use a short length of flexible hose
(not less than 3/4" (19mm) in diameter) between pump and piping to eliminate
strain to pipes.
AIR INLET & PRIMING
For start-up, open an air valve approximately 1/2" to 3/4" turn. After the unit
primes, an air valve can be opened to increase flow as desired. If opening the valve
increases cycling rate, but does not increase flow rate, cavitation has occurred,
and the valve should be closed slightly.
For the most efficient use of compressed air and the longest diaphragm life,
throttle the air inlet to the lowest cycling rate that does not reduce flow.
SERVICE AND OPERATING MANUAL
Model MSA3, MSA3-C
Type 7
Mine/Construction-Duty
CE
II 2GD T5
II 2G c T5
II 2Dc T100°C