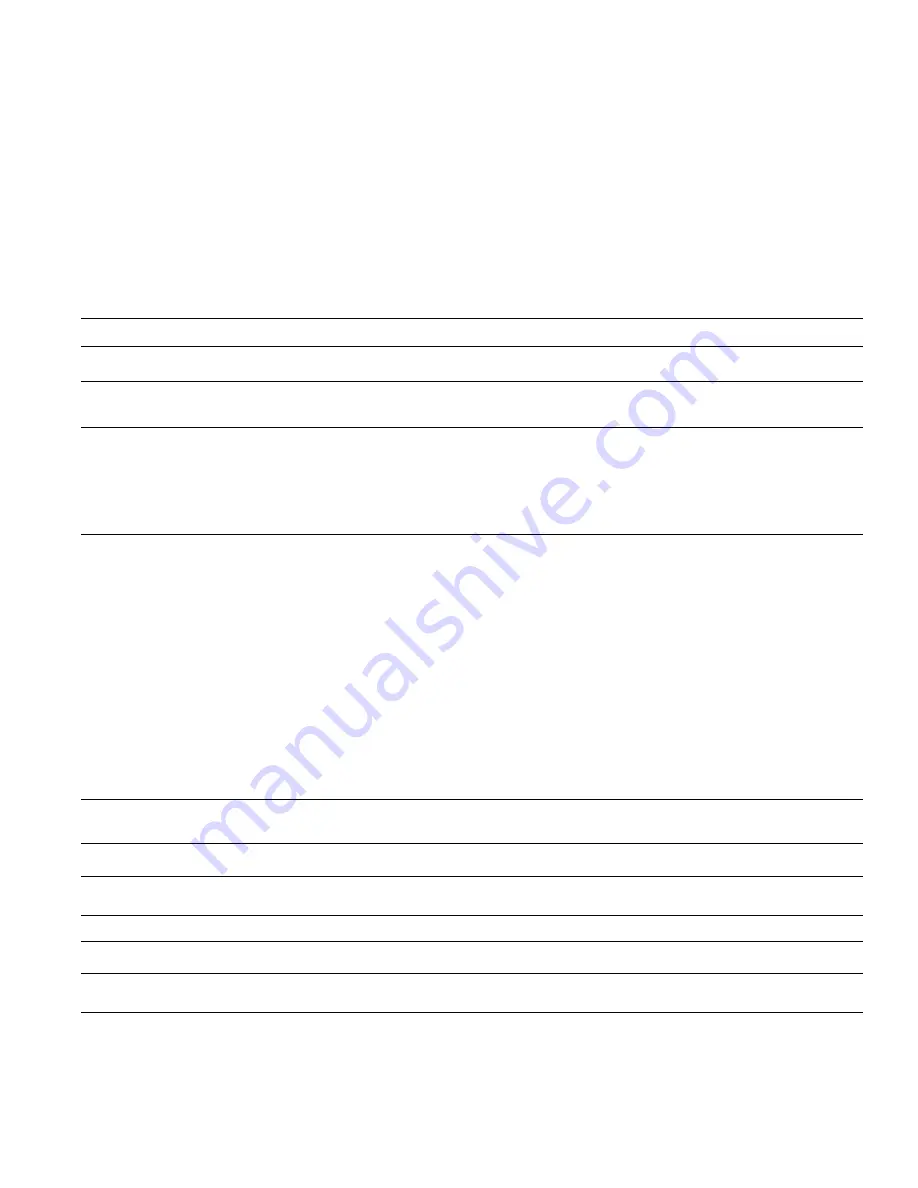
Warner Electric • 800-825-9050
P-0257-WE • 819-9027
21
TROUBLESHOOTING
Applies to MCS-203 Control, MCS-166, Power Supply,
and MCS-605-1 or TCS-605-5 Pivot Point Sensor
General: The chart below will be helpful when isolating exact problems which may occur in the control system. The
chart will also prove helpful when encountering problems with the initial start-up of the system. When the system
has been running for some time, the chart will also be helpful when checking for worn, broken or frayed wires; bent
or broken control system parts; blown fuses;* loose terminal connections and wire connections; loose or broken
sensor couplings; worn or loose mechanical parts for the tension stand (bearing, couplings, etc.); and dust or dirt
accumulation inside the control which has caused components to overheat.
Sympton A: Dancer will not raise from bottom position.
Probable Cause
Suggested Solution
Incorrect Dancer Position setting
Adjust dancer position setting until dancer moves to normal running position.
Dancer is not free to move because
of obstruction.
Remove obstruction, release any holding devices or safety locks.
No DC power to the control.
Check for power LED illumination on MCS-203
Check for power LED illumination on MCS-166
Check fuses
Check proper DC input connections to control (refer to tension control hookup
instructions).
Check AC power input to MCS-166 if used.
Brake is not engaging.
Check to be sure lead wires to the brake are at the brake terminals 1 and 2 of the
control.
Check to see if sensor is connected.
Using a voltmeter, check for approximately -1.8 to +28 VDC between the brake
terminals. If there is no voltage, check for approximately -1.8 to +28 VDC between
terminals and 2 of the control. If the voltage is present at the control and not at the
brake, wires to the brake are open.
If there is no voltage at terminals 1 and 2 of the control, replace the printed circuit
board assembly.
If there is voltage at the brake terminal, check the brake coil resistance with an
ohmmeter for shorted brake magnets or wrong coil voltage.
Check for proper pivot sensor alignment. Terminals 6 and 7 on MCS-203=7.5VDC
± 0.1 VDC w/dancer control: 6.1 VDC - shortest web loop. 8.9 VDC -longest web
loop.
Check to see that brake is wired properly.
Check to see that brake-off input is not activated.
Brake does not have the torque capacity
required for the application.
Verify that the correct brake was selected by repeating the selection procedure.
Symptom B: Dancer moves to and remains at,upper limit during initial systems start-up.
NOTE: Refer to symptom C if dancer moved to upper limit after it had been running normally at the proper position.
Probable Cause
Suggested Solution
Incorrect Dancer Position setting
Adjust dancer position setting until dancer moves to normal running position.
Roll shaft not free to rotate with control off.
Brake and shaft must be free to rotate with control off.
Sensor incorrectly connected to control Verify
sensor connections, terminals.
Verify sensor connections.
Содержание MCS-166
Страница 1: ...Tension Control System MCS 166 MCS 203 MCS 204 Installation Operation Instructions P 0257 WE 819 9027 ...
Страница 16: ...16 Warner Electric 800 825 9050 P 0257 WE 819 9027 Figure 13 Control Adjustment Locations MCS 166 MCS 203 ...
Страница 20: ...20 Warner Electric 800 825 9050 P 0257 WE 819 9027 Figure 14 Control Adjustment Locations MCS 166 MCS 204 ...