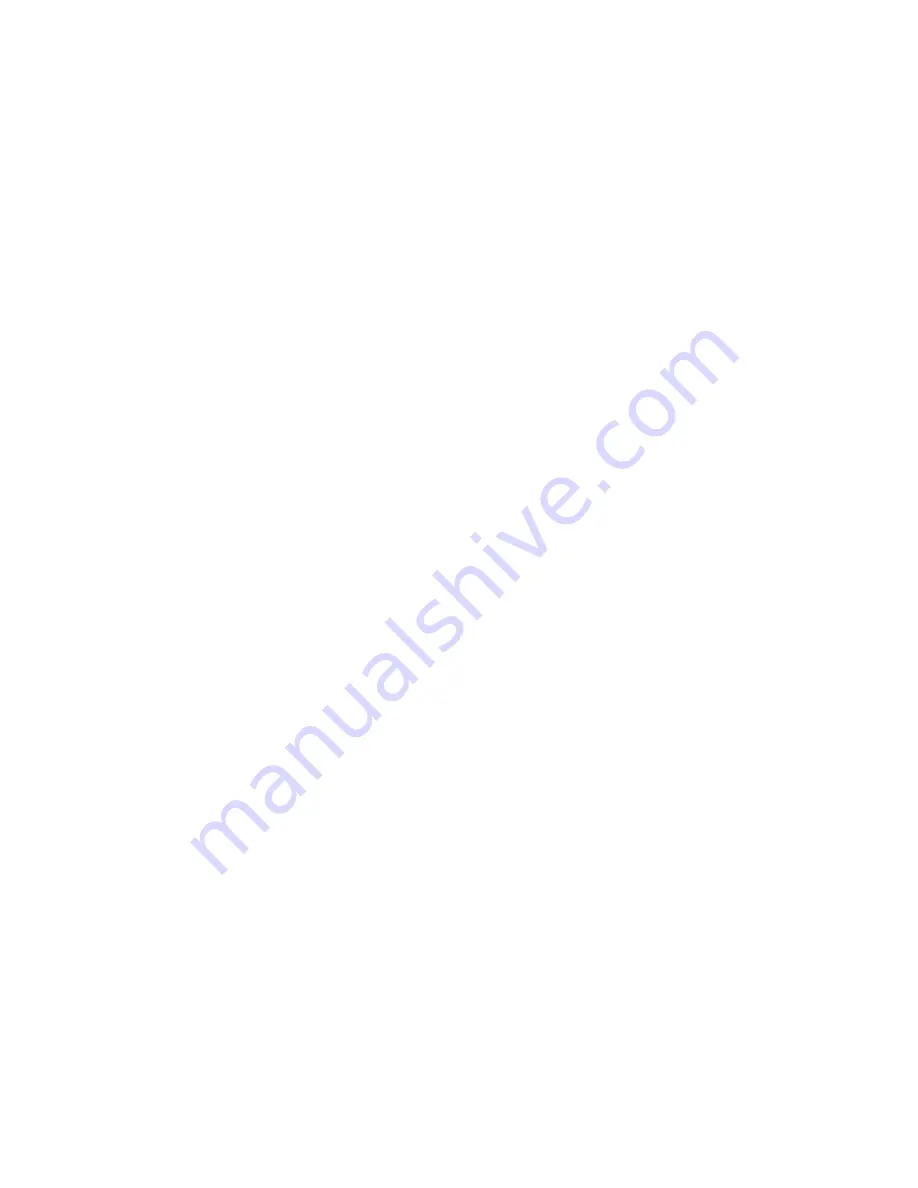
14
Warner Electric • 800-825-9050
P-0257-WE • 819-9027
❑
3 Brake-On/Brake-Off Switch Check
(optional)
❑
a. Place Brake-Off switch in brake-off
mode and note that the “brake” indicator
goes out.
❑
b. Return the Brake-Off switch to its normal
run mode.
❑
c. If used, turn on the Brake-On switch and
note that the “brake” indicator goes full on.
❑
d. Return Brake-On switch to its normal
Running , position.
NOTE: If operation of the Brake-On/Brake-Off
switches produced the opposite results in 3a and 3c
above, the wiring is reversed.
Refer to the MCS-166/MCS-203 wiring section for the
proper connections.
❑
4. Anti-Residual Adjustment
❑
a. Activate the Brake-Off switch (if used) or
move the dancer to the shortest web-
loop position.
❑
b. Check that the brake armature floats
away from the brake magnet with no
sticking.
❑
c. If the armature sticks to the magnet,
adjust the anti-residual potentiometer
CW or CCW until the armature is free
with no sticking.
❑
d. Reapply the brake either by moving
the dancer to its longest web-loop or
by returning the brake off switch to its
normal run position and activating the
brake-on input.
❑
e. Repeat steps 4a through 4d above.
❑
f. If brake releases freely, make no further
adjustments as the anti-residual is now set.
NOTE: CCW rotation decreases the anti-residual
output while CW rotation increases it. Excessive CW
rotation can cause brake engagement.
❑
5. Frequency Adjustment
The frequency adjustment changes
the modulation frequency to eliminate
brake “hum” or “howl” when the brake is
stationary. The frequency is factory set and
normally requires no adjustment.
❑
a. Turn CW if a low pitch hum is present
or CCW if hum is high pitched.
*CAUTION: To set the frequency, the control must
be unplugged from its housing. Do
not unplug control unless power is
off. Failure to turn power off before
unplugging will result in damage to
control module and/or power module.
C. Start-Up and Dynamic Adjustments
❑
1. Verify that power is on.
❑
2. Start the machine and draw material.
❑
3. After the Dancer has stabilized, adjust the
front panel “Dancer Position” potentiometer
for the desired dancer running position.
❑
4. If the system is providing stable dancer
operation, increase the “Gain” until the
dancer hunts or oscillates. Note the gain
position number where this occurs.
❑
5. Reduce the “gain” setting from step 4
above one to two digits.
❑
6. If dancer instability is apparent from initial
start, reduce the gain until it becomes
stable.
NOTE: This is only a preliminary gain setting. A final
gain setting is required at core diameter for optimum
system performance.
❑
7. Run the system until the unwind roll is
within two to four inches of core diameter.
❑
8. If the system has been stable, re-set the
front panel “gain” until dancer hunting or
oscillation occurs, noting the gain setting
number, then reduce the setting one or two
digits.
NOTE: This is the optimum gain setting. No further
adjustments are necessary.
❑
9. If system stability cannot be achieved
through front panel “gain” adjustment, it
may be necessary to adjust gain functions
internally.
CAUTION: Internal P-l-D gain adjustments should
be made only after all other attempts
to achieve system stability have failed.
These adjustments should be made by
qualified personnel only.
NOTE: Internal access is required for the set-up
adjustments which follow. This can be accomplished
with the TCS-900 set-up and diagnostic tester or by
removing the side panel plate from the housing, or, on
new versions with ribbon cable connectors, by sliding
the control module partially out of the housing.
CAUTION: If side panel plate on the control housing
is to be removed, insure the power is off
before removing the control module from
the housing. Failure to disengage power
before removing the module will result
in damage to the control and/or power
module.
IMPORTANT: Follow the sequence outlined below
to properly adjust the P-l-D circuit
gains. If the TCS-900 is used, follow
the instructions included with the
TCS-900.
*Applies only to “older style” units without ribbon cable
assemblies.
Содержание MCS-166
Страница 1: ...Tension Control System MCS 166 MCS 203 MCS 204 Installation Operation Instructions P 0257 WE 819 9027 ...
Страница 16: ...16 Warner Electric 800 825 9050 P 0257 WE 819 9027 Figure 13 Control Adjustment Locations MCS 166 MCS 203 ...
Страница 20: ...20 Warner Electric 800 825 9050 P 0257 WE 819 9027 Figure 14 Control Adjustment Locations MCS 166 MCS 204 ...