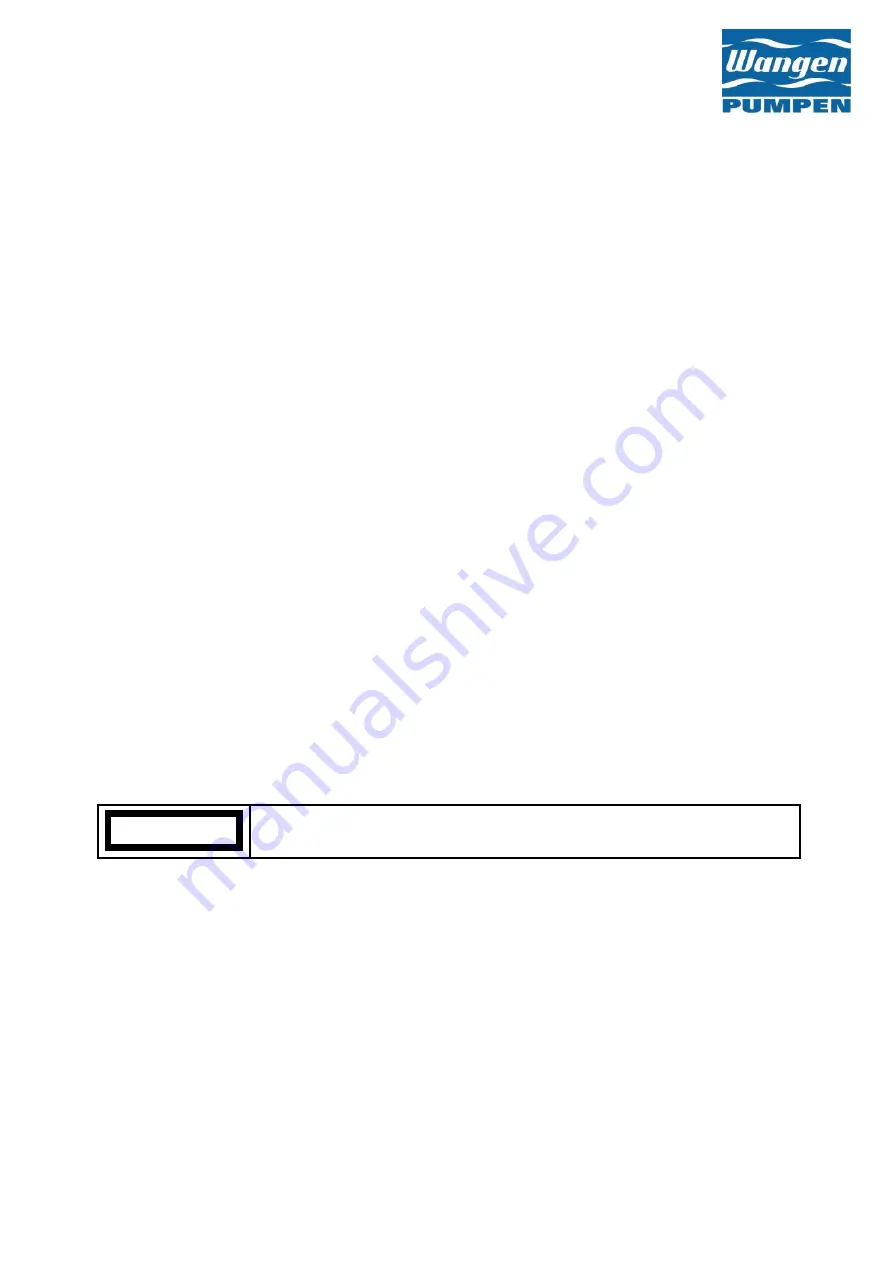
Instruction Handbook KL
Chapter 5
BA KL V11 en
10/2014
page 5-2
5.1.4 Pumps for food applications
If the WANGEN pump is to be used to convey food, you will have to clean it before putting it into
operation and before each production run. This cleaning can be performed as follows:
Basically, by disassembling the pump and cleaning its various parts with the necessary
cleaning products.
In individual cases by the so-called C.I.P. - Cleaning (cleaning in place), provided the form
of cleaning is allowed for this medium.
It is a submersible pump or a suction pump in a dead-space design with a special tangential CIP
–
socket
and
the system is configured so that the operation as well the cleaning without removal or
reconstruction can be performed.
In Hopper pumps or suction pumps with conveying screw further activities must be taken for
cleaning, such as the use of spray lances or high pressure cleaning equipment so that the hopper
and the conveying screw be clean.
After the first time, following changes to the system, to the cleaning process, or the cleaning medium
must, under the CIP cleaning by disassembling the pump, the effectiveness of cleaning to be
checked, i.e. whether the pump is clean.
A recommended C.I.P. procedure is as follows:
Towns water pre.-rinse to get out product left over inside the pump.
Temperature 10
– 20°C, max.70°C
1
– 2 % volume Sodium Hydroxide / water,
for 10
– 20 min at 60 – 80°C
Towns water,
for 5
– 10 min at 60 – 80°C
1
– 1.5% volume Nitric acid / water
for 5
– 10 min at 50 – 70°C
Towns water for 5
– 10 min
Temperature normal 10
– 20°C, max. 70°C, for a period of 5 – 10 min
The flow rate of the rinsing liquids should not be lower than 1.5 m/s during C.I.P. procedure.
Possible damage
Prove the chemical resistance by using stators made from solid materials (plastics,
bronze)
When under C.I.P treatment, the stator has to undergo thermal and chemical stress. It is therefore
important to ensure that the pump is operating in STOP AND GO function during C.I.P. treatment
which is two to three starts with one to two rotations in the course of one minute. This will provide
sufficient cleaning of the rotor / stator conveying cavities and it is also reduces the mechanical stress
additionally on the stator through deformation work.
ATTENTION