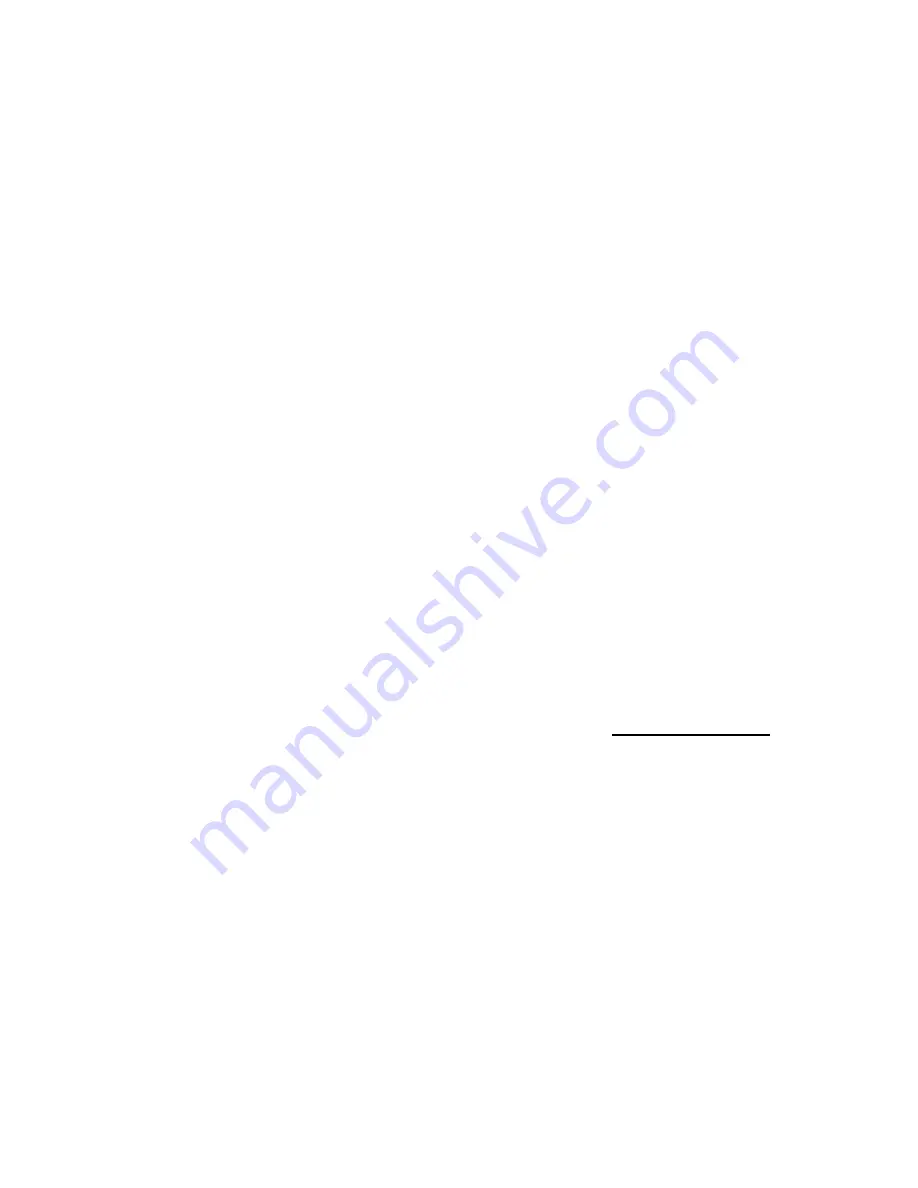
The “0” on your head setting scale references the top of the ½” sub-plate supplied with your machine. For
example if you were milling a ¾” piece of stock you would set the machine head at the ¾” setting. Adjusting
your machine head to this scale setting will give you a full pass cut and a completely finished profile. This is a
multi-pass machine and with multi-pass you can add 3/16”, in this example, to the 3/4” dimension for a first
pass setting of 15/16”. In this example you may set the machine head to any scale setting between 3/4” and
15/16” for a first pass. These settings allow you to achieve proper roller tension for holding the stock and
providing a safe operation.
Be sure to
check for sufficient feed roller contact
before proceeding to use this setup and be sure to rotate
your moulding knives to
check for knife rotation clearance with the chip extractor installed
and the power
off before starting the machine. Turn the knife arbor by turning the motor pulley at the inner guard opening.
Other moulding tips
Stock height should be within 3/16” of finished moulding size. If making one pass only it should be within
1/32”.
Stock width should be uniform and to finished moulding size. Saw ripping to width will not make the stock
uniform enough for smooth flow through the guides, and thus, will not result in a satisfactory molding. We
recommend that all stock be planed in both width and height to finished moulding size before setting up to do
the profile.
When tightening the knives, push them firmly against the lip and sideways against the bolts in the direction of
the tube side of the machine for an exact profile match up. Hold secure while tightening bolts.
Set the head height to within 3/16”of your stock height. This will give you proper roller tension on your
moulding stock. This is the correct way to mold. It is acceptable to leave 3/16” of the cut for multiple passes.
But for safety reasons leave no more than 3/16”.
On some extremely deep or wide cuts, some prior stock removal will be required before molding. You may
remove this stock using one of the rabbet/dado knives found in our catalog. You may also use a dado blade on a
table saw.
Failure to set your head height within 3/16” of the stock height will create an extreme safety hazard in that
possibly not enough roller pressure will be applied, or that no roller pressure at all will be applied.
Do not cut a wider stock area than the knife was designed to cut. This will cause excessive heat in the knife,
burn your stock and puts a harmful load on the feed system.
The roll pressure screws are set at maximum molding pressure from the factory. They are screwed into the head
as far as possible and the check nut is tightened.
When you use the machine for planing you will need to reduce the roller pressure. Loosen the pressure screw
lock nut and screw out each pressure to a setting ¼” higher than the fully seated position and retighten the lock
nut.
To change the molding knives, remove the chip extractor. Set one knife at a time in place with the bevel edge
toward the in-feed end of the machine. Firmly push the knife down against the arbor lip and sideways against
the bolts in the direction of the tube side of the machine. Hold secure while tightening bolts with a 7/32” allen
wrench or drive.
6