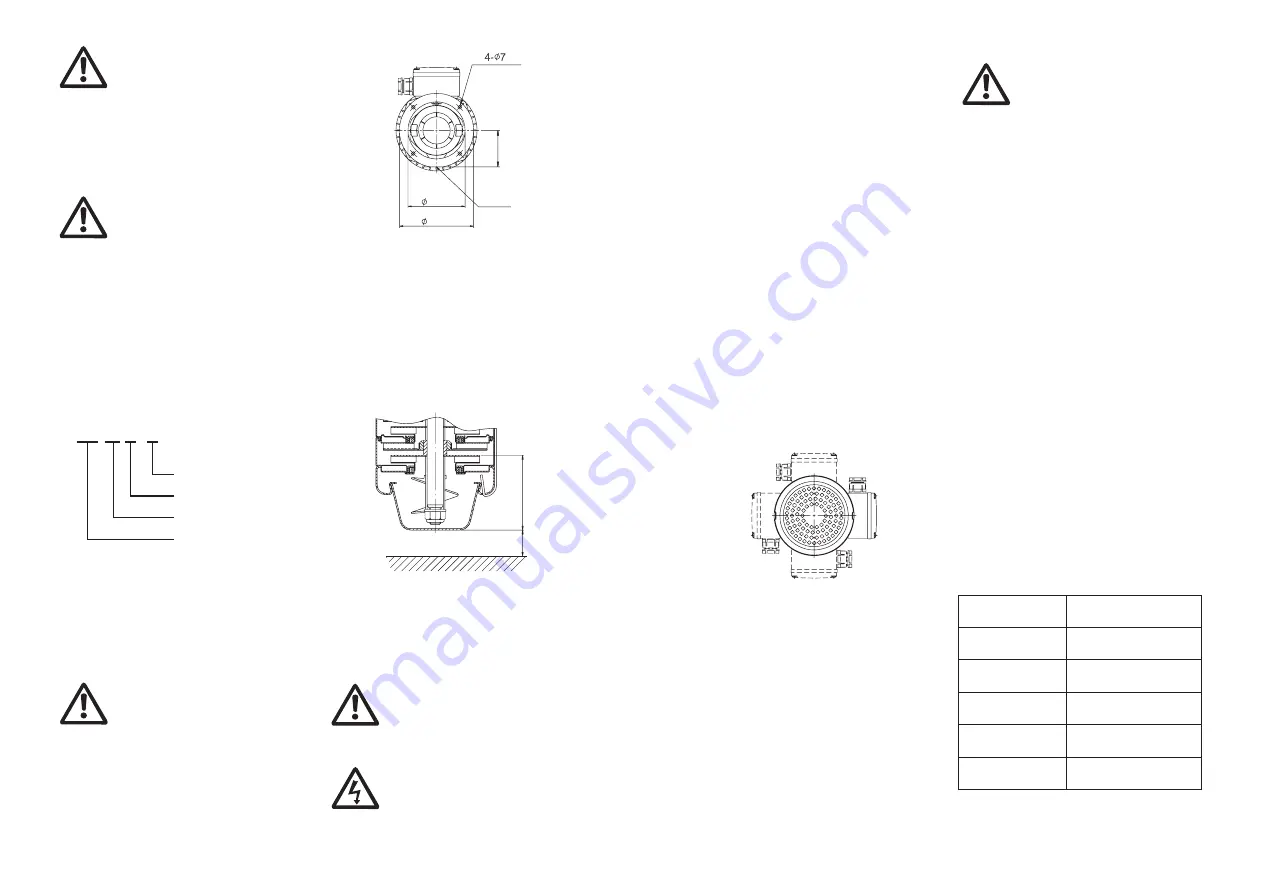
Please read this installation and
operating instructions carefully
before beginning installation and
operation.
1. Application
1.1 The TPK series is multi-stage centrifugal
pump designed for transferring liquid
used in machine tools.
1.2 The pump can not be used to transfer
explosive liquids, such as gasoline,
diesel oil and other similar liquids.
It is only suitable for water diluted,
low viscosity, uncorrosive cooling
or lubricant liquids.
2. Model Explanation
The pump models are coded based on the
number of pump stages. Standard stages
consist of both diffusers and impellers, and
null stages, for special installation
considerations, contain diffuser chamber only.
The pump model is shown on the pump
nameplate.
Example:
TPK 2T 3 - 3
Number of Impellers
Number of Diffuser
Standard Capacity(m /hr)
Model Code
3
3. Technical Data
Liquid Temperature: +0
ƨ
~ +90
ƨ
Ambient Temperature: Max. +50
ƨ
Enclosure Class: IP54
Discharge Pressure: Max. 10 kg/cm
2
4. Installation
The motor surface temperature is
extremely high. It must be mounted
in the save place to avoid accidental
touch.
4.1 Mounting Position
The pump must be mounted vertically.
Installation is simply done by inserting the
pump into the hole on the tank top, and
fixed by four bolts in mounting flange.
Flange dimensions are shown in Fig 1.
64
100
130
PCD 115
Fig. 2
Fig. 1
PF 3/4"
Outlet
4.2 Submerged Depth
To avoid dry running and damage the
pump during operating, the minimum
pump submerged depth is 60mm, as
shown in Fig. 2. In addition, a minimum
25mm gap between pump suction inlet
and tank bottom is required to allow for
sediment build up.
Min. 60
25
5. Electrical Connection
5.1 Electrical installation should be carried
out in accordance with the local
electrical code. Make sure that the
electricity supply has been switched
off before electrical connection.
5.2 Resulting in electrical hazard
warning mark has been marked
outside the connecting box. Be
careful.
~ 2 ~
Fig. 3
5.3 Electrical specifications (voltage, hertz)
are shown on the pump nameplate. Verify
that the power supply voltage and hertz
match pump requirement. An external
ON/OFF switch must be installed.
5.4 Electrical connection should be in
accordance with diagram shown on
connecting box, and motor current should
be within rated amps as shown on
nameplate. Three phase pump requires
extra magnetic starter with protection.
5.5 Three phase motor must check rotating
direction. The rotating direction indicated
on the fan cover, is counterclockwise
viewing from fan cover end. Interchanging
any two leads with power off can reverse
the pump rotation.
5.6 The position of the motor connecting box
is adjustable. Referring to Fig.3, the
adjustment can be done by removing the
motor fan cover, unscrewing the frame
bolts, turning the motor casing and
connecting box subassembly together to
proper position. Finally, screw the frame
bolts tight, and put the fan cover back.
90
0
180
270
o
o
o
o
6. Start-Up
Before start the pump, re-verify the
following items.
6.1 Verify if three phase pump rotation is
correct. The rotating direction should be
counterclockwise viewing from fan cover
end.
6.2 Piping and joints should be fitted carefully
to prevent leak. Leak in the piping will
cause the pump hydraulic lost.
6.3 The pump has been filled with liquid.
6.4 No any foreign objects block the suction
filter.
7. Operation and Maintenance
The pump can not be operated
under the fully closed of discharge
outlet continuously, because it will
raise the liquid temperature
abnormally, and damage the pump
after 5 minutes.
7.1 Lubrication
The mechanical seal and shaft sleeves
inside the pump are lubricated by working
liquid.
7.2 Suction Filter
Suction filter should be always kept clean
to make sure no any foreign objects block
the filter in order to have best
performance.
7.3 Periodic Examination
The following check items should be
carried out periodically to ensure the
normal operation.
7.3.1 Check the discharge and output
pressure of working liquid.
7.3.2 Check the leak of piping and joints.
7.3.3 Examine the motor starter/container.
7.3.4 Test all the pump control function.
7.4 The pump can not be used to transfer
explosive liquids. Extra protective device is
required if the working liquid temperature
exceeds 60
ƨ
to avoid scald hazard.
7.5 The pump should not be used in the
transferring of toxic or contaminated
liquid. Service and maintenance will not
be provided, if the pump application is not
in compliant with the installation and
operation procedures. The user must take
the responsibility for the damage.
8. Sound Pressure Level
MODEL
TPK2T3-3
TPK2T5-5
TPK4T3-3
TPK4T5-5
[ dB(A) ]
<70
<70
<70
<70
<70
TPK4T8-8
~ 3 ~