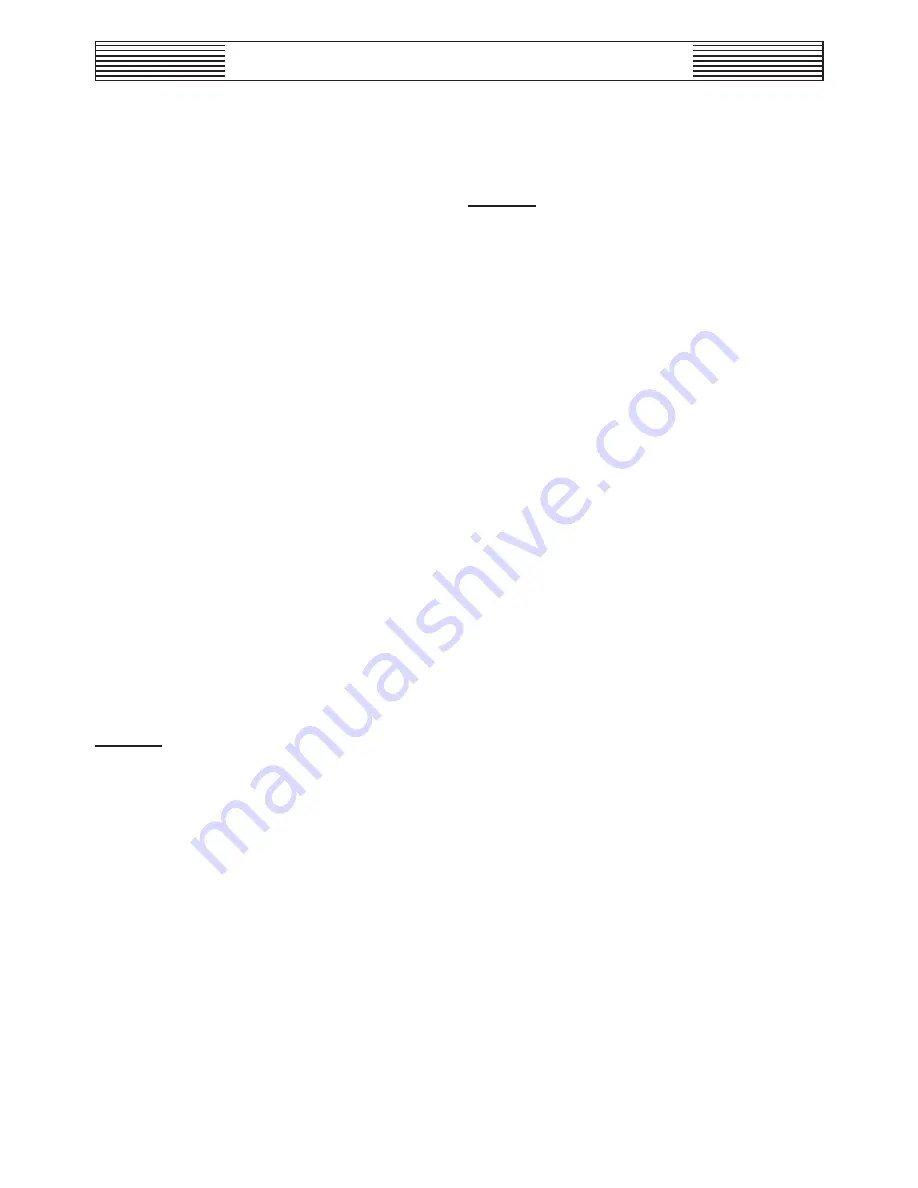
WT.025.000.001.UA.IM.0614
PAGE 9
CHLORINE HANDLING MANUAL
EVOQUA
W3T98244
tank car pressure is the only force causing the chlorine to
discharge, many cars are padded with dry air by the producer
or the user. Reference to Chlorine Institute Pamphlet 66,
Chlorine Tank Car Loading, Unloading, Air Padding, Hydro-
static Testing, should be made for information on user air
padding. It is essential that air padding pressure be kept as
low as possible for satisfactory operation of the chlorination
equipment since excessive air padding pressures can have a
negative impact on evaporator performance. The depletion
of the liquid chlorine supply in the car is accompanied by a
sharp drop in tank car pressure.
After the angle valve is closed and the discharge line emptied,
the piping may be disconnected. The valve outlet plugs should
be replaced and the discharge piping capped immediately.
4 PIPING
4.1 PIPING MATERIALS AND JOINTS
If the chlorinator capacity is low enough, the vacuum regula-
tor or the complete chlorinator may be mounted directly on
a cylinder or ton container valve, totally eliminating pressure
piping. In this case, reference to the equipment instruction
book provides all necessary details.
Pressure connections from all chlorine containers are nor-
mally made by means of flexible connections made of copper
tubing. Use yoke type connections at container valves. The
chlorinator or vacuum regulator instruction book should be
referred to for details for use of flexible connections along
with the required auxiliary cylinder or ton container valves,
header valves, and auxiliary header valves (if required).
WARNING: ALWAYS REPLACE FLEXIBLE CONNECTIONS
ANNUALLY (OR SOONER IF THERE IS EVIDENCE OF DE-
TERIORATION).
The usual practice for chlorine liquid or gas pressure lines, at
the commonly encountered pressures and temperatures at
chlorinator installations, is the use of 3/4 or 1.0 inch schedule
80 carbon steel seamless pipe with Class 3000 forged steel
fittings; two-bolt flanges (commonly referred to as oval am-
monia unions) are also often used. Both screwed and socket
welded construction are common. Threaded joints should be
made up using litharge and glycerine for permanent joints,
white lead or TFE tape for others.
To facilitate maintenance, the number of line valves should
be kept to a minimum. Insulation is required only in those
cases where it is necessary to prevent chlorine gas lines from
becoming chilled, or liquid lines from becoming overheated.
More complete details, along with ASTM and ANSI specifi-
cations, can be obtained by referring to Chlorine Institute
Pamphlet 6, Piping Systems For Dry Chlorine.
WARNING: TWO COMMON CAUSES OF CHLORINE PIP-
ING LEAKS ARE:
1. RE-USE OF GASKETS. THIS SHOULD NEVER BE DONE.
ALWAYS HAVE AN ADEQUATE SUPPLY ON HAND AND
ALWAYS USE NEW GASKETS OF THE CORRECT MATE-
RIAL AND SIZE AS IDENTIFIED ON THE EQUIPMENT
PARTS DRAWING.
2. IMPROPERLY MADE-UP THREADED PIPE JOINTS. SEE
CHLORINE INSTITUTE MANUAL OR PAMPHLET 6 FOR
RECOMMENDED PROCEDURE.
4.2 GAS PIPING INSTALLATION REQUIREMENTS
Reliquefaction of a gas should be avoided. If liquid chlorine
is carried downstream to the chlorinator or vacuum pip-
ing, it may soften the plastic components and affect their
structural strength. Liquid can wash any collected contami-
nants into the vacuum regulator and can also cause erratic
surging, freezing, and pressure release, which can damage
the diaphragm and control valves. Cold conditions in a gas
pipe line (cold to the touch, dripping of water condensed
from the atmosphere, frost, ice) are an indication that liquid
chlorine is present in the line and is flashing to gas. Refer to
the proper guidelines that follow.
It is important to observe the correct temperature condi-
tions in conducting chlorine gas under pressure from the
location of the containers to the point of use. To avoid dif-
ficulty with reliquefaction of chlorine, pressure piping and
control equipment receiving gas under pressure should be
at a higher temperature than that of the chlorine contain-
ers. In general, a difference of 5° to 10° F is recommended.
Pitch pressure lines uphill from the gas source toward the
chlorinators if possible.
Install a pressure reducing valve or the chlorinator vacuum
regulator close to, but higher than, the source of gas. The use
of a chlorine pressure reducing valve is also recommended
in those localities where severe temperature changes are
likely to be encountered during a 24-hour period.
It is preferable to run chlorine pressure gas lines overhead
through relatively warm areas rather than along the floor
or through basement areas where lower temperatures may
be encountered. Do not run these gas lines along exterior
walls that may be cold in winter months. Do not run pres-
sure gas lines under windows from which cold air descends
in winter months.
Содержание SERIES V-2000
Страница 1: ...SERIES V 2000 CHLORINATOR 3000 Lb 24 Hr Manual Control BOOK NO WT 025 055 004 UA IM 0814 W3T109620...
Страница 2: ...W3T109620 SERIES V 2000 CHLORINATOR 3000 LB 24 HR MANUAL CONTROL BOOK NO WT 025 055 004 UA IM 1009...
Страница 11: ...WT 025 055 004 UA IM 0814 MANUAL CHLORINATOR 3000lb 24hr EVOQUA W3T109620...
Страница 12: ......
Страница 17: ......
Страница 32: ......
Страница 43: ......
Страница 71: ...56 WT 025 055 004 UA IM 0814 MANUAL CHLORINATOR 3000lb 24hr EVOQUA W3T109620...
Страница 72: ......
Страница 112: ...96 WT 025 055 004 UA IM 0814 MANUAL CHLORINATOR 3000lb 24hr EVOQUA W3T109620...
Страница 113: ......
Страница 115: ......
Страница 116: ...CHLORINE HANDLING MANUAL Cl2 BOOK NO WT 025 000 001 UA IM 0614 W3T98244...