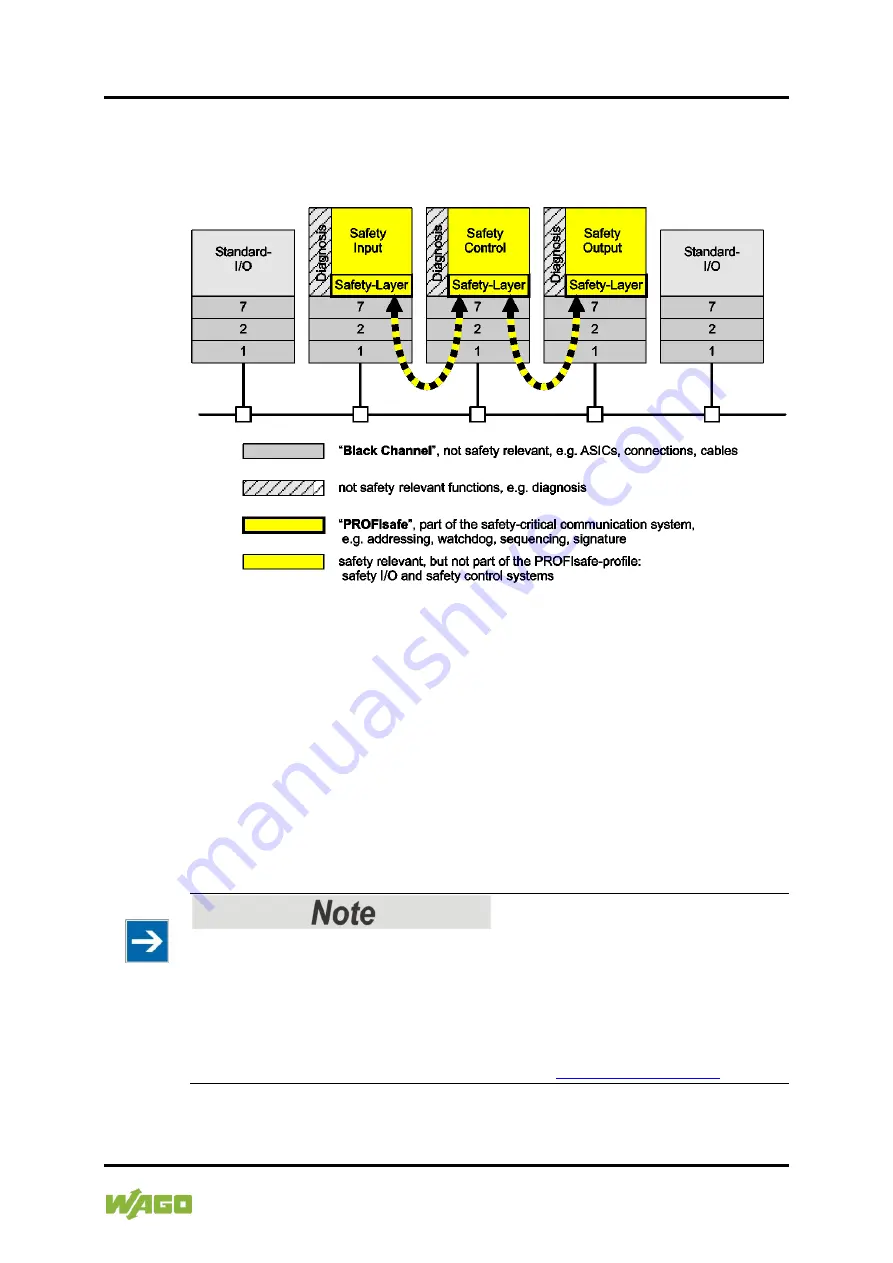
WAGO-I/O-SYSTEM 750
Appendix 147
753-668/000-004 4FAI 0/4-20 mA Diff PROFIsafe
Manual
Version 1.0.0, valid from HW/SW Version 01/01
Data is exchanged between the safe F I/O modules and the safe PLC via
PROFIBUS or PROFINET as the basis. Data is exchanged in the form of
PROFIsafe telegrams that correspond to the PROFIsafe protocol profile
according to IEC 61784-3-3.
Figure 52: PROFIsafe Layer Model
The PROFIsafe telegrams are transferred between the safe PLC and F
I/O module via the so-called "black channel". The "black channel" extends from
the PROFIBUS or PROFINET connection of the PLC via the fieldbus
coupler/controller, the local bus in the node to the I/O module. The PROFIsafe
telegrams are only evaluated in the safe PLC and in the F I/O module.
When detecting communication errors, the F I/O modules are passivated in that
all safe outputs are switched off and the substitute values are transferred to the
safe PLC as an input process image.
Evaluation of the input process image and output of the output process image via
the F I/O modules with digital outputs are controlled by the safe PLC.
Note the following guidelines and information when setting up PROFIsafe
applications:
•
Guideline PROFIsafe - Requirements for Installation, Immunity and electrical
Safety (PROFsafe Environmental Requirements, current version)
•
Installation recommendations (PROFIBUS Installation Guidelines, current
version)
These documents are available on the Internet at