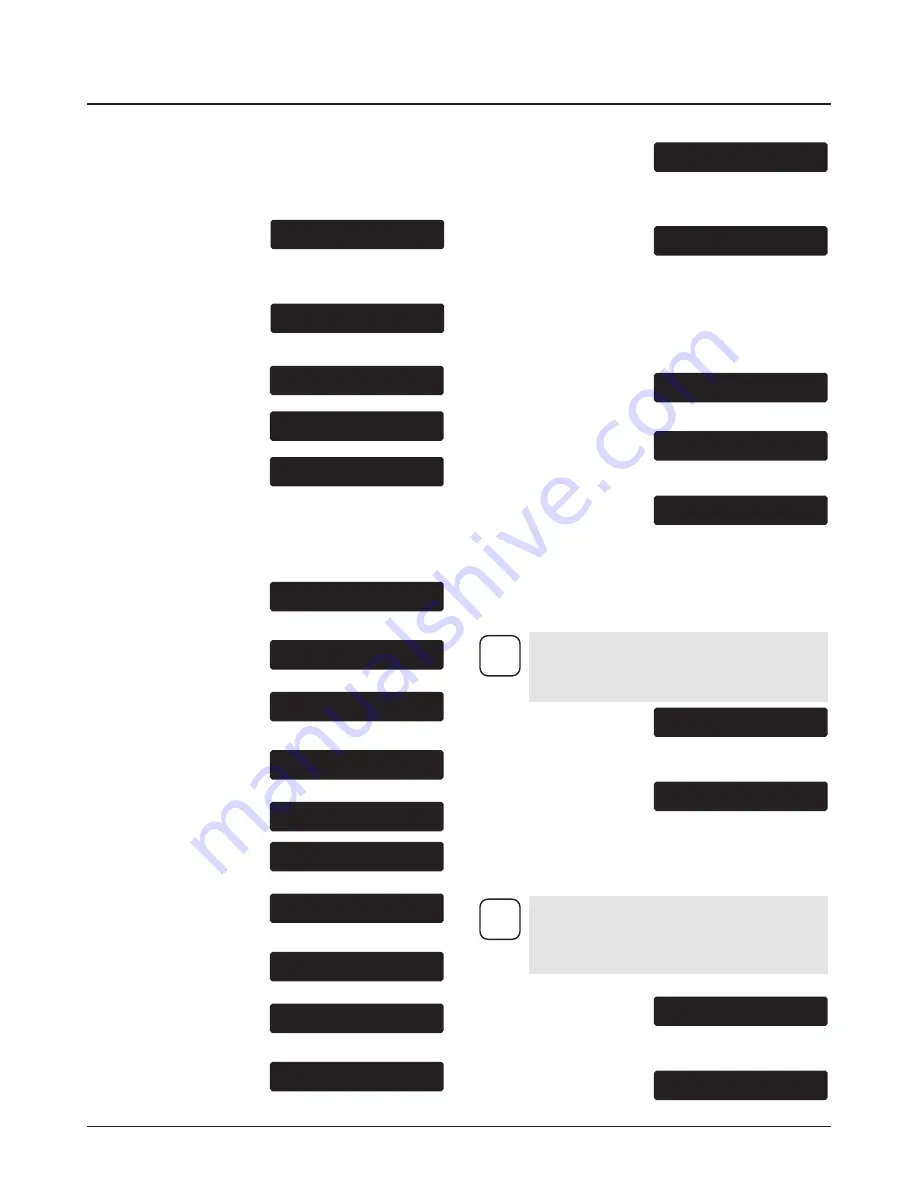
ProSpray 30 • 34
g
Service Time Screen
The Service Time screen
allows the user to set a service
time interval (in hours). Below
the set time, the screens shows the current amount of hours on
the sprayer. To select the Service TImer screen, press the #4
key.
The screen will toggle between
the service hours and a screen
that allows the user to change
the service time interval.
When the service time interval is set and met by the run hours,
the display will toggle between the "Main screen" and a
"Service Required" screen at sprayer startup. To stop the
toggling, scroll to the "Service Time" screen and either set a
new service time interval or set the service time to "0".
Pressure Screen
The Pressure screen allows
the user to see the current set
point pressure as well as the
actual working pressure.
To select the Pressure screen,
press the #4 key. This screen
is also the Main Screen.
Security Code Screen
The Security Code screen
allows the user to set a four
digit security code to prevent
unauthorized use of the sprayer. If a security code has been
set, the control system display will ask for the code at startup.
If the correct code is entered, the display will show the Main
Screen and the sprayer will operate. If the wrong code is
entered, the display will continue to ask for the correct code
and the sprayer will be disabled. To set or change the security
code, press the #2 key.
Enter the old security code
number to access the screen
that allows the code change. If
the wrong code is entered, the display will continue to ask for
the correct code and the security code cannot be changed.
Enter the new security code.
Once the new code is entered,
the display will automatically
ask that the new code be re-entered for verification. If the same
new code is re-entered, the display will confirm that the new
code has been accepted and return to the Main Screen. If the
new code is re-entered incorrectly, the display will return to the
“Enter New Code Number” screen and the process will repeat.
Prime Screen
The Prime screen appears
when the pressure control knob
is set at the “Min” setting in the
yellow zone.
Clean Screen
The Clean screen appears
when the pressure control knob
is set at the CLEAN position in
the blue zone and the relief valve is in the PRIME position.
CLEAN
PRIME
To inactivate the security function, enter “1111” at
the “Enter New Code Number” screen (this is the
default code that leaves the sprayer unlocked).
As a result, the Main Screen will appear at sprayer
startup.
i
ENTER NEW CODE
NUMBER
ENTER OLD CODE
NUMBER
If the sprayer is new, no security code is set and
the Main Screen will appear at startup. Also,
when setting a security code for the first time, the
“Enter Old Code Number” screen will not appear.
i
SECURITY CODE
SELECT-4
MENU-1
SET MPa
23.0
ACTUAL MPa
22.5
PRESSURE
SELECT-4
MENU-1
SERVICE @ XXXHR
RUN HOURS XX
SERVICE TIME
SELECT-4
MENU-1
Menu Screens
Several menu screens are available for the user to customize
and monitor sprayer operation. They include Main Screen,
User Pre-Sets, Volume Pumped, Job Volume, Unit Serial #,
TImers, Job Timers, Service Time, Pressure, Security Code,
Prime, and Pulse Clean.
Main Screen
The Main Screen is the default
screen for the control system at
sprayer startup.
Pressing the #2 key switches between PSI
and MPa units of measure.
Press the #1 key to scroll
through the remaining menu screens.
User Pre-Sets Screen
The User Pre-Sets screen
allows the user to set four
different pressure settings and save them for future use. To
select the User Pre-Sets screen, press the #4 key.
Press keys 1 through 4 from
the Select screen to select or
change a pre-set pressure.
Press the #4 key to select the
setting and the Main Screen
will appear.
Press the #2 key to change the
setting. On the following
screen, use the #2/+ key to
increase the setting or the #3/- screen to decrease the setting.
Once the desired setting has been reached, press the #4 key
to set and the Main Screen will appear. To select or change
the remaining three pre-sets, scroll to the User Pre-Sets screen
and repeat the above procedure.
Volume Pumped Screen
The Volume Pumped screen
shows the total number of
gallons or liters sprayed by the
sprayer.
To select the Volume Pumped
screen, press the #4 key.
Job Volume Screen
The Job Volume screen allows
the user to reset a gallon
counter to track usage on
specific jobs.
To select the Job Volume
screen, press the #4 key.
Unit Serial # Screen
The Unit Serial # screen shows
the sprayers serial number.
To select the Unit Serial #
screen, press the #4 key.
Timers Screen
The Timers screen shows the
total time the sprayer has been
turned on as well as the total
time the sprayer has been running (pumping).
To select the Timers screen,
press the #4 key.
Job Timers Screen
The Job Timers screen allows
the user to reset the “ON TIME”
and “RUN TIME” to track time
on specific jobs.
To select the Job TImers
screen, press the #4 key. The
screen will toggle between the
timers and a screen that allows the user to reset the timers.
ON TIME XXXXX:XX
RUN TIME XXXX:XX
JOB TIMERS
SELECT-4
MENU-1
ON TIME XXXXX:XX
RUN TIME XXXX:XX
TIMERS
SELECT-4
MENU-1
SER # XXXXXXXXXX
PRESS 1 FOR MENU
UNIT SERIAL #
SELECT-4
MENU-1
JOB LITERS
XXXX
MENU-1
RESET-3
JOB VOLUME
SELECT-4
MENU-1
LITERS XXXXXX
PRESS 1 FOR MENU
VOLUME PUMPED
SELECT-4
MENU-1
PRE-SET #1
5.2
PRESS +/- TO CHG
MPa SETTING
5.2
SELECT-4
CHG-2
SELECT
PRE-SETS 1-4
USER PRE-SETS
SELECT-4
MENU-1
SET MPa
23.0
ACTUAL MPa
22.5
Starting operation