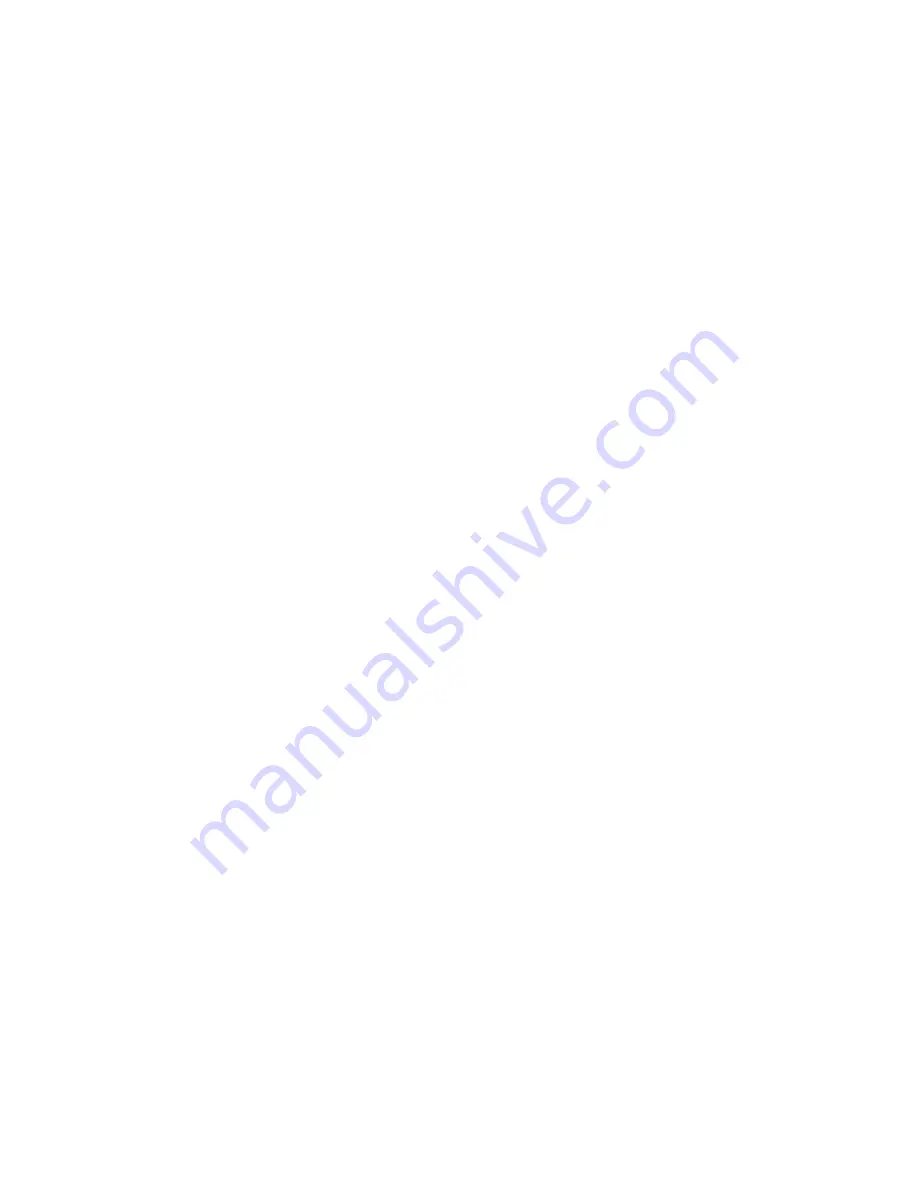
15
2) If the blade is running too far from the
wheel flange, the wheel rim low on the
outside, too close to the frame plate, see
"A," Figure 4, below, turn both threaded
spacers, equally, top and bottom of the case
¼ turn counterclockwise, drawing the gear
case closer to the frame plate, pushing the
wheel rim away from the frame plate. NOTE:
Do not over-compensate. Turn
the threaded spacers ¼ turn only.
3) Tighten the hex lock screws.
Tension the blade and run it 30 seconds.
Shut down the machine. Check that the
blade is not still running too far away from, or
scrubbing on the wheel flange. .010" to .030"
clearance is ideal.
4) If the blade is running too close to the
wheel flange, scrubbing, see "B," Figure 4,
below, the wheel rim high on the outside,
turn both spacers clockwise, equally, ¼ turn,
pushing the gear case away from the frame
plate, drawing the outside wheel rim closer
to the frame plate.
5) Tighten the hex lock screws and check
the clearance as in step (3).
3. Blade tension adjustment. Factory-set
blade tension is for size and type blades
used in general purpose sawing.
The blade tension control must be in the
Tension position while sawing.
The dial indicator needle at the operator's
control console must come exactly to the
green dot on the dial.
If the tension indicator needle does not
reach, or passes the green dot, inaccurate
sawing or blade break results.
For maximum feed, speed and blade life
consult a reliable blade supplier for recent
research in tooling.
Request test cuts on the machine and the
work piece with his recommended blade.
Tension the blade to manufacturer speci-
fications with a precision tension gauge
mounted on the blade.
The supplier will install his gauge on the
blade.
Tension the blade.
When the needle on the control console dial
reaches the green dot, the blade supplier will
determine from his gauge whether to
increase or decrease tension for his recom-
mended blade.
To change blade tension, remove the cover
on the lower front of the operator's control
console.
Increase or decrease blade tension with the
double lock knob hydraulic valve, inside left
wall of the cabinet.
With tension adjusted for the choice of
blades, lock the valve.
Move the green dot to the new needle
location on the face of the gauge.
When changing blade types for other work,
tension the new blade to blade manufacturer
specifications.
Before each cut, make sure the tension
needle is at the green dot.
4. Sawing force check.
The dual hydraulic servo-controlled sawing
force system measures work piece
resistance to the blade while sawing,
applying uniformly controlled force to the
blade for accurate sawing regardless of
configuration, size or type of material.
Sawing force range for this machine is 0 to
400 pounds, adjusted at the operator's
control console.
See controls 20 and 21 on page 6.
Too much or too little sawing force results in
uneven sawing or broken blades.
With each blade change, inspect the blade
guides for chips and sludge build up. They
prevent blade guides and metering valve
linkage from working properly, producing
other than the sawing force adjusted at the
control console.
Sludge in the coolant or hydraulic fluid, a
malfunctioning sawing force dial, metering
valve or linkage from the blade to the
metering valve alters the dial reading from
actual force the blade applies to the work