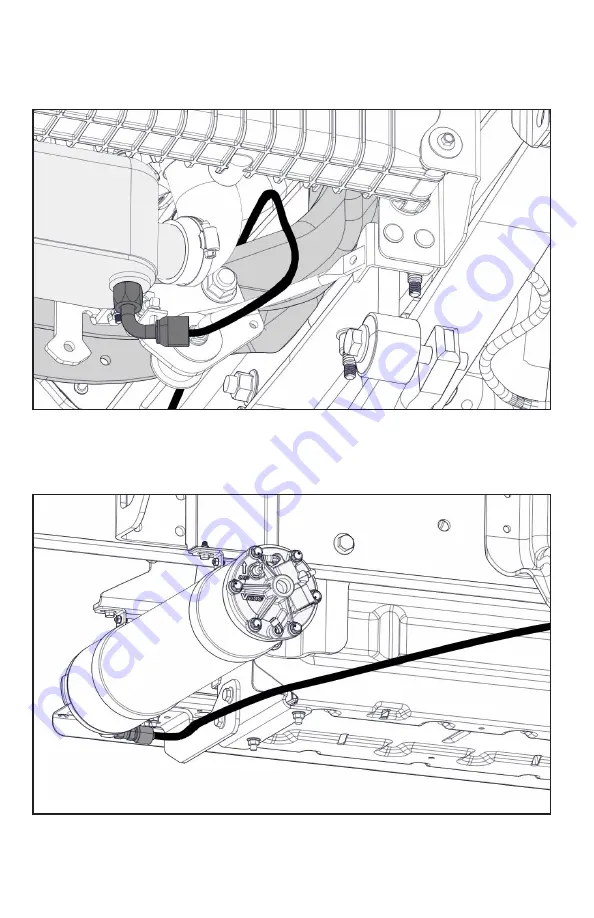
VMAC - Vehicle Mounted Air Compressors
VMAC Technical Support: 888-241-2289
VMAC Knowledge Base: www.kb.vmacair.com
34
☐
Connect the 90° fitting on the longer 1/2 in hose to the driver side fitting of the
VMAC oil cooler.
☐
Route the 1/2 in hose over the engine cross member, following the transmission
cooler lines, then down toward the bottom of the driver side frame rail (Figure 46).
☐
Continue to route the 1/2 in hose along the same path as the transmission
cooler lines, then loop the hose toward the AOST along the bottom of the
battery box (Figure 47).
Figure 46 — Connect compressor oil return hose
Figure 47 — Connect compressor oil return hose