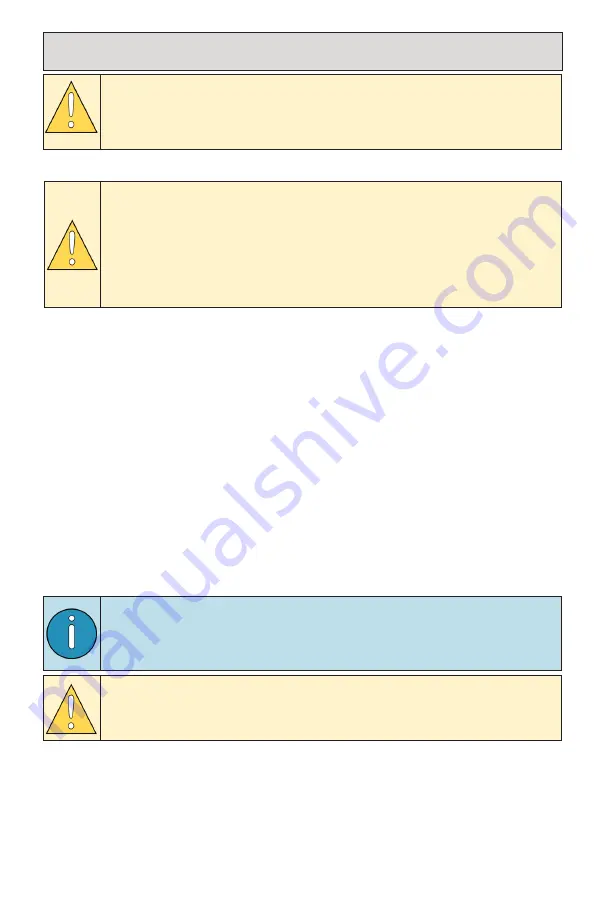
VMAC - Vehicle Mounted Air Compressors
VMAC Technical Support: 888-241-2289
VMAC Knowledge Base: kb.vmacair.com
29
Extreme Climates and Elevation
The G300004 has been designed to operate in moderate climates of
0 °C to 40 °C (32 °F to 104 °F)below 3,500 feet. Operating outside
of this range may result in performance issues with the engine and
compressor.
Cold Environment Operation
While the unloader valve is manually opened, the compressor will
only produce approximately 40 psi. Once the engine has reached
normal operating temperature, close the unloader valve to allow the
system to build to full system pressure.
The optional Cold Climate Kit (P/N: A500044) is a starting aid only.
Contact a Honda dealer for recommendations when operating the
engine below -15 °C (5 °F).
Cold Environment Recommendations
•
Ensure the following conditions are met before starting the compressor:
•
Use the choke in cold environments, or for first start of the engine.
•
The system’s components must all be at, or above 0 °C (32 °F). Starting the
system while any of the components are below 0 °C (32 °F) may result in
excessive engine cranking while starting, the engine failing to start, belt
slippage, and engine stalling. Use the optional Cold Climate Kit
(P/N: A500044) or store the system indoors and start it while the components
are still warm.
•
For engine oil recommendations in temperatures below 0 °C (32 °F), refer to
the Honda Owner’s Manual supplied with the system. Failure to follow the
recommendations in the Honda Owner’s Manual may result in poor engine
performance or engine damage.
•
The unloader valve should be manually activated to aid start up; this will
reduce the load on the compressor, resulting in less load on the engine during
warm up (Figure 5 on page 23).
The G300004 system is not designed or recommended for use in
cold climates (below 0 °C / 32 °F) unless equipped with a VMAC cold
climate kit (P/N: A500044).
If equipped with the optional VMAC Cold Climate Kit
(P/N: A500044), the cold climate kit must be turned off prior to
starting the engine, and must remain off for the duration of engine
operation.
Содержание G300004
Страница 2: ......
Страница 14: ......
Страница 22: ......
Страница 24: ......
Страница 97: ......
Страница 107: ...VMAC Vehicle Mounted Air Compressors VMAC Technical Support 888 241 2289 VMAC Knowledge Base kb vmacair com 105 Notes...
Страница 108: ...VMAC Vehicle Mounted Air Compressors VMAC Technical Support 888 241 2289 VMAC Knowledge Base kb vmacair com 106 Notes...
Страница 109: ...VMAC Vehicle Mounted Air Compressors VMAC Technical Support 888 241 2289 VMAC Knowledge Base kb vmacair com 107 Notes...
Страница 111: ......