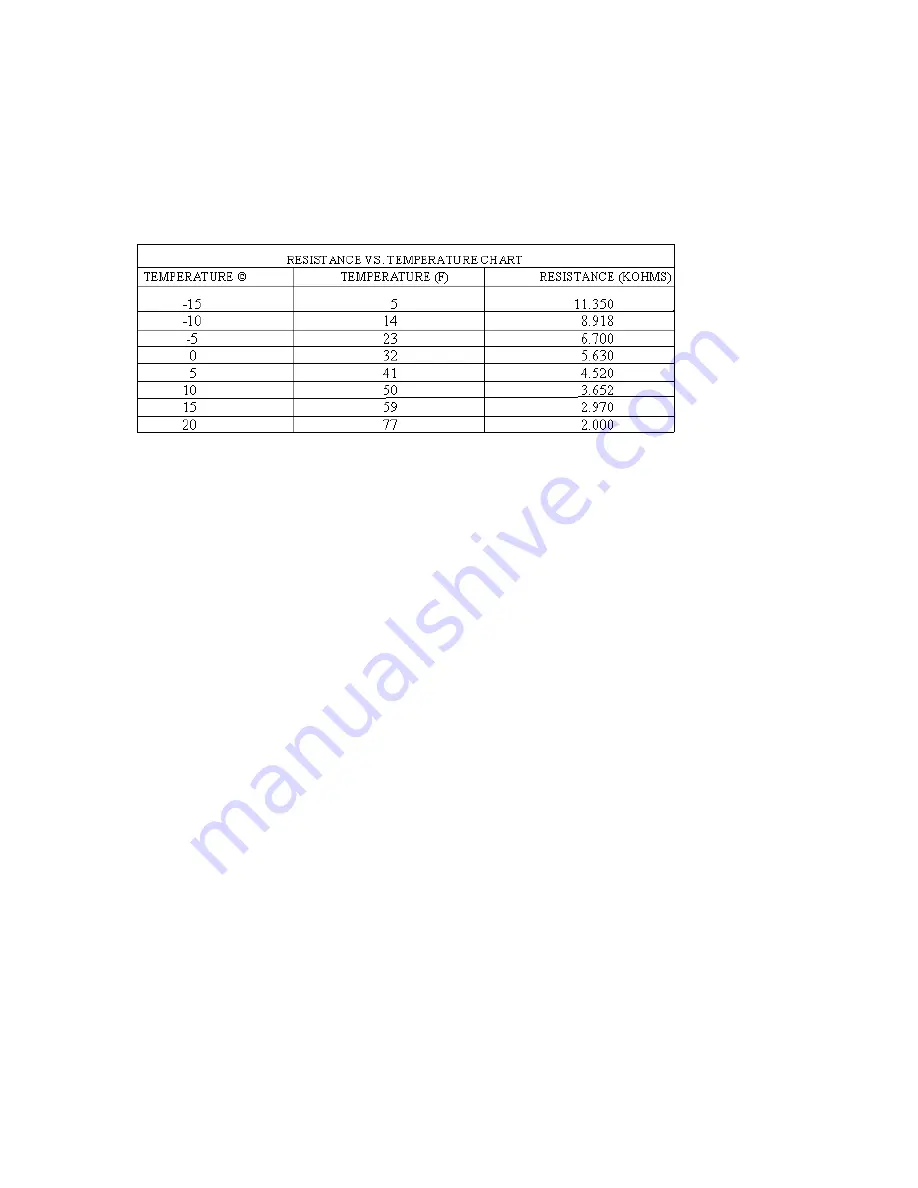
2.
Use a reference temperature point that is known (such as an ice bath) and measure
the resistance across the wire leads.
3.
Check the recorded resistance with that in the table 5.1 below.
If measured resistance falls outside the resistance given in the table 5.1 within 4% of the
value, the thermistor is bad and will need to be replaced.
Table 5.1
If the thermistor has been tested and is found to be good then check the temperature of
the evaporator plate and the resistance of the thermistor. If the temperature of the
evaporator plate does not correspond to a proper resistance from the thermistor then
check for proper and secure connection of the thermistor to the evaporator plate bracket.
The use of a heat sink compound can be used between the thermistor and the evaporator
bracket if needed. The recommended heat sink compounds are:
Radio Shack part number 276-1372
General Electric part number 10-8108
To access and replace the evaporator thermistor:
1.
Remove any ice and drain the reservoir by pulling the drain plug.
2.
Disconnect power, water line, and drain line.
3.
Remove the access panel and rear panel from the rear of the unit (see figure 3.3).
4. Disconnect the red and black wires to the “EVAPORATOR THERMISTOR”
terminals on the electronic control (there should also be a tag on the gray wire
insulation with part number 41006205 for the evaporator thermistor).
5.
From inside the unit, remove the escutcheon panel.
6.
Remove the grid-cutter (see section 6.1).
7.
Remove the ice deflector.
8.
Remove the reservoir (see section 6.2).
9.
Remove the evaporator thermistor by removing the screw securing it.
10. Feed the thermistor”s wire out through the opening in the rear of the unit.
Installation
Reverse the removal procedure for installation. Be sure to thoroughly tighten the
thermistor’s screw for proper bracket to thermistor contact.
27
Содержание VUIM150
Страница 1: ...VIKING RANGE CORPORATION P O DRAWER 956 GREENWOOD MS 38930 USA...
Страница 34: ...Figure 7 2 35...