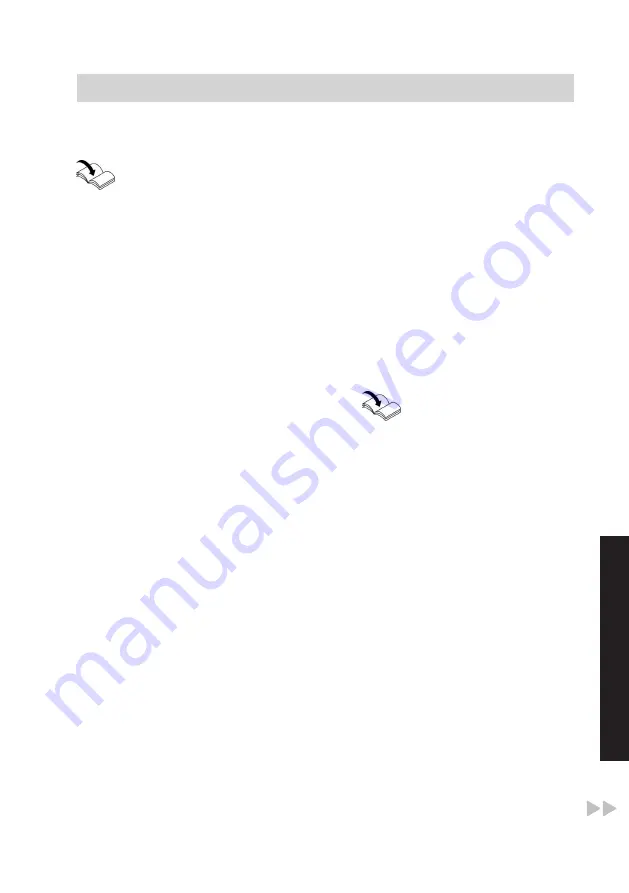
11
Commissioning the system
Details provided by the burner
manufacturer and regarding
accessories
0
1.
Open the boiler doors and check
that the turbulators (if fitted) are fully
pushed into the hot gas flues.
0
2.
Check that the installation room
ventilation is unobstructed.
0
3.
Filling the heating system with water
and venting it.
!
Please note
Unsuitable water quality can
damage the boiler body.
Fill and operate the heating
system with water that com-
plies with the "Water quality
guidelines" from page 22
onwards.
Note
Record the fill volume and total
hardness on page 20.
0
4.
Check the system pressure.
0
5.
Check all fitted components, such
as pipework, valves, controllers,
pumps etc. for function and leaks.
0
6.
Check the fuel supply for leaks and
pressure.
0
7.
Open the flue gas damper (if instal-
led).
0
8.
Check that the cleaning aperture on
the flue outlet is closed.
0
9.
Check that the dewatering line (if
installed) is correctly connected to
the condensate connection.
The condensate connection must
be sealed when not in use.
10.
Open the shut-off valves in the oil
lines (at the oil tank and filter) or
open the gas shut-off valve.
11.
Switch ON the main isolator, the
ON/OFF switch for the boiler drives
and burner in this order.
Burner manufacturer's oper-
ating instructions
12.
Start the boiler at a low output (max.
30 %) and heat up to a temperature
of approx. 30 K below the operating
temperature.
The condensate drains must be
open and any condensate must be
correctly collected or drained.
13.
After the required flow temperature
has been achieved, open the boiler
return valve, the feedwater valve if
required and then, very slowly, the
boiler flow valve.
14.
Only then, enable the full burner
load.
15.
While the system heats up, check
the correct function of all control and
safety equipment.
16.
Observe the pressure and temper-
ature test equipment.
Commissioning, inspection, maintenance
Further details regarding the individual steps
5727 529 GB
Service
Содержание Vitomax 200-LW M64A
Страница 30: ...30 5727 529 GB...
Страница 31: ...31 5727 529 GB...