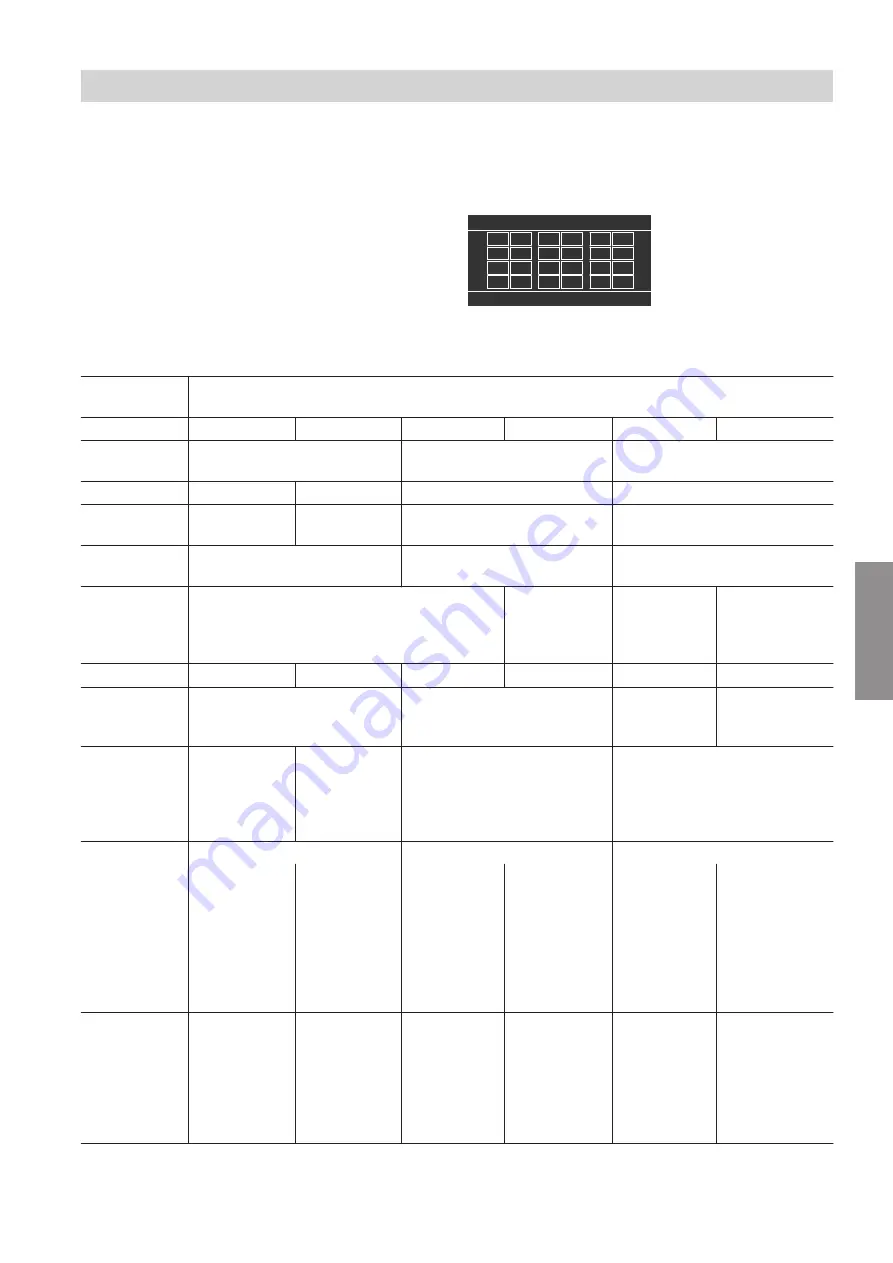
63
Brief scan
In the brief scan, you can call up temperatures, soft-
ware versions and connected components,
for example.
1.
Press
OK
and
å
simultaneously for approx. 4 s.
2. "Diagnosis"
3. "Brief scan"
.
4.
Press
OK
.
The display shows 9 rows with 6 fields each.
Diagnosis Brief scan
2:
1:
3:
4:
Select with
Ø
0
0
0
1
F
0
0
0
0
0
0
0
A
0
0
0
0
0
0
1
2
0
0
0
Fig. 29
For an explanation of the relevant values in the individual rows and fields, see the following table:
Row (brief
scan)
Field
1
2
3
4
5
6
1:
System scheme 01 to 10
Software version
Control unit
Software version
Programming unit
2:
0
0
Appliance version
Appliance ID CU-ID
3:
0
0
Number of KM-BUS subscrib-
ers
Software version, solar control
module SM1
4:
Software version
Burner control unit
Type
Burner control unit
Version, burner control unit
5:
Internal details for calibration
0
Software ver-
sion,AM1 ex-
tension
Software ver-
sion, EA1 exten-
sion
0 = No EA1
6:
0
0
0
0
0
0
7:
LON
Subnet address/system num-
ber
LON
Node address
0
0
8:
LON
SBVT config-
uration
LON
Software ver-
sion, commu-
nication cop-
rocessor
LON
Neuron chip software version
Number of LON subscribers
9:
Heating circuit A1/HC1
Heating circuit M2/HC2
Heating circuit M3/HC3
Remote con-
trol
0: None
1: Vitotrol
200-A/
200-RF
2: Vitotrol
300-A
Software ver-
sion, remote
control
Remote con-
trol
0: None
1: Vitotrol
200-A/
200-RF
2: Vitotrol
300-A
Software ver-
sion, remote
control
Remote con-
trol
0: None
1: Vitotrol
200-A/
200-RF
2: Vitotrol
300-A
Software ver-
sion, remote
control
11:
0
0
Software ver-
sion
Mixer exten-
sion, heating
circuit M2
0: No mixer
extension
0
Software ver-
sion
Mixer exten-
sion, heating
circuit M3
0: No mixer
extension
0
Diagnosis and service scans
Diagnosis, weather-compensated control unit
(cont.)
5839829
Diagnosis