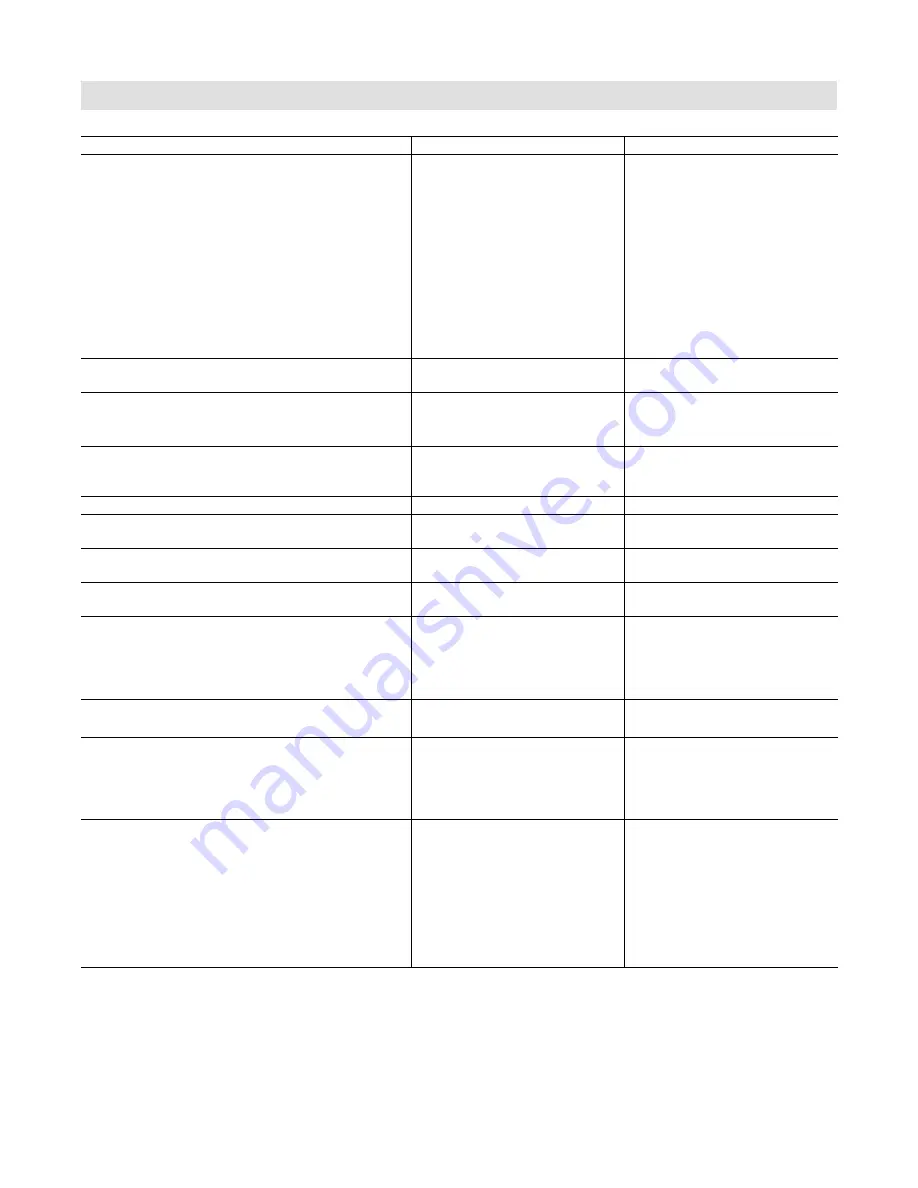
5461 889 - 16
56
Vitodens 222-F, B2TB 19, 35, 68, 125 Installation
Technical Data
Additional Information
Boiler Model No. 222-F B2TB
19, 68
35, 125
CSA input Natural Gas (NG)
CSA input Liquid Propane Gas (LPG)
CSA output/DOE
*1
heating capacity NG
CSA output/DOE
*1
heating capacity LPG
Net AHRI rating
*2
MBH
(kW)
MBH
(kW)
MBH
(kW)
MBH
(kW)
MBH
(kW)
12-68
(3.5-20)
12-68
(3.5-20)
11-64
(3.2-19)
11-64
(3.2-19)
55
(16)
19-125
(5.5-37)
31-125
(9-37)
18-117
(5-34)
29.5-117
(8.6-34)
102
(30)
Heat exchanger surface area
ft.
2
m
2
12.96
1.2
12.96
1.2
Min. gas supply pressure
Natural gas
Liquid propane gas
“w.c.
“w.c.
4
10
4
10
Max. gas supply pressure
*3
Natural gas
Liquid propane gas
“w.c.
“w.c.
14
14
14
14
A.F.U.E.
%
95
95
Weight
(including installation fittings)
lbs
(kg)
302
(137)
302
(137)
Boiler water content
USG
(L)
1.02
(3.88)
1.02
(3.88)
Boiler max. flow rate
*4
GPM
(L/h)
6.2
(1400)
6.2
(1400)
Expansion tank
*5
(for heating system side)
Precharge pressure
Capacity
psig
USG
(L)
12
3.2
(12)
12
3.2
(12)
Max. operating pressure
at 210ºF (99ºC)
psig
bar
45
3
45
3
Boiler water temperature
- Adjustable high limit (AHL) range
space heating (steady state)
- Fixed high limit (FHL)
ºF
(ºC)
ºF (ºC)
68 to 180
(20 to 82)
210 (99)
68 to 180
(20 to 82)
210 (99)
Boiler connections
Boiler heating supply and return
Pressure relief valve
Drain valve
Boiler supply/return for
indirect-fired DHW storage tank
(field supplied)
Gas valve connection
NPTM”
NPTF”
(male
thread)
NPT”
NPTF”
¾”
¾”
¾”
¾”
¾”
¾”
¾”
¾”
¾”
¾”
*1
Output based on 140ºF (60ºC), 120ºF (49ºC) system supply/return temperature.
*2
Net AHRI rating based on piping and pick-up allowance of 1.15.
*3
If the gas supply pressure exceeds the maximum gas supply pressure value, a separate gas pressure regulator
must be installed upstream of the heating system.
*4
See “Waterside Flow” starting on page 30 in this manual.
*5
Determine the required size of the expansion tank to be installed in the heating system.
If the integral expansion tank is insufficient, install a suitably sized expansion tank on site.