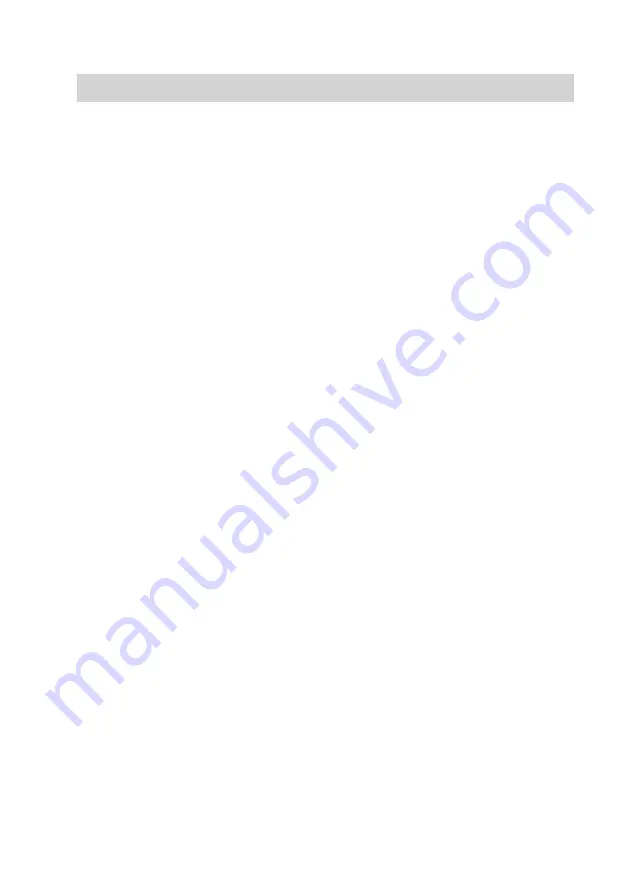
5
Commissioning, inspection, maintenance
Steps - commissioning, inspection and maintenance..........................................
............................................................................................ 46
............................................................................................. 48
Fault display......................................................................................................... 56
Fault codes........................................................................................................... 57
Faults without fault display................................................................................... 64
Burner control unit flow chart
........................................................................... 65
Burner control unit connection diagram................................................................ 67
Mains filter unit connection diagram..................................................................... 71
......................................................................................... 73
Ordering parts...................................................................................................... 76
Overview of the assemblies................................................................................. 76
Parts not shown.................................................................................................... 76
Boiler assembly.................................................................................................... 77
Thermal insulation assembly................................................................................ 77
Burner assembly, 400 kW.................................................................................... 80
Burner assembly, 500 kW.................................................................................... 81
Burner assembly, 620 kW.................................................................................... 84
Index
Index
5794 780 GB