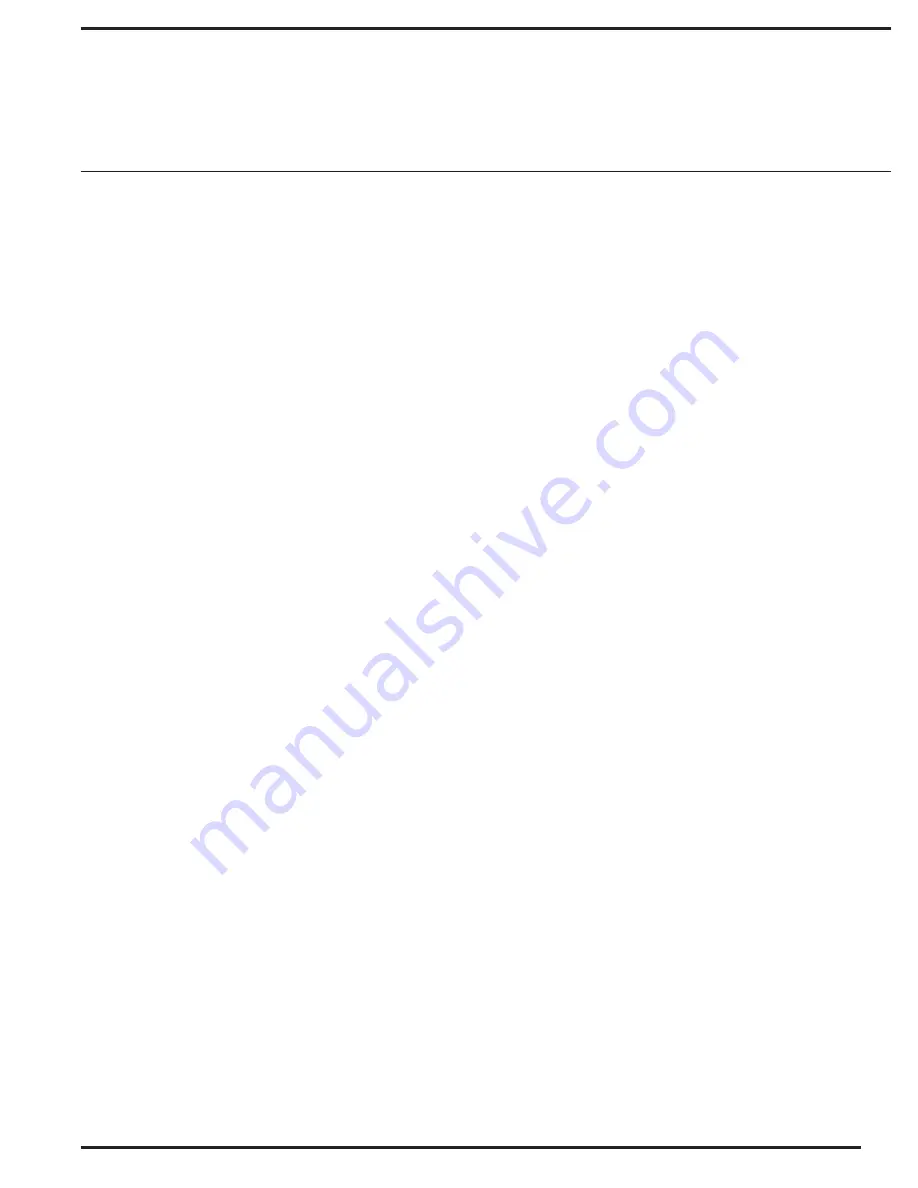
9
Observation
Possible Cause
Remedy
1.) Table does not raise but motor is
running or humming.
2.) Table raises too slowly.
3.) Motor labors, or is excessively hot.
4.) "Spongy" or "jerky" table operation. Do not
confuse spongy operation with small surges caused
by foreign material on the roller tracks.
5.) Table lowers too slowly when loaded.
a. Motor may be single-phasing (humming)
if three phase unit.
b. Voltage at motor terminals may be too low
to run pump at existing load.
c . Hose or hydraulic line is leaking.
d. Fluid level in reservoir is low.
e. Load exceeds capacity requirements. Relief valve
is bypassing the fluid back into the reservoir.
f . Suction filter is clogged, starving pump.
g. Suction line may be leaking air, due to loose fittings.
h. Filler/Breather cap on tank may be clogged.
i. Down Valve may be energized by faulty wiring or
stuck open.
j. Hydraulic pump may be inoperative.
a. Foreign material stuck in Down Solenoid, causing
some fluid to bypass back into tank.
b. Foreign material clogging suction filter, breather cap,
or a pinched hose.
c . Low motor voltage.
d. Table overloaded.
e. Pump is inoperative.
a. Voltage may be low.
b. Incorrect wiring, or single-phasing.
c . Oil starvation causes pump to bind. High internal
heat is developed. If this occurs, pump may be
permanently damaged.
d. Binding cylinders.
a. Fluid starvation.
b. Air in system.
a. Down valve filter clogged.
b. Pinched tube or hose.
c . Foreign material in flow control valve.
d. Binding cylinders
e. Foreign material in velocity fuse.
a. Ascertain that all 3 phase lines are present
at the motor.
b. Measure voltage at motor terminals or as near as
possible, while pump is running under load. If
voltage is sufficient, check for inadequate or
incorrect wiring as this can starve the motor.
Correct as necessary.
c . Correct as necessary.
d. Add fluid. Refer to Owner's Manual for proper
fluid levels.
e. DO NOT CHANGE RELIEF VALVE SETTING.
Instead, reduce the load to rated capacity.
f . Remove and clean.
g. Inspect all fittings for proper fit.
h. Remove and clean.
i. Remove Solenoid Valve. Check and clean.
(Refer to Hydraulic Section of Owner's Manual).
j. Disconnect hydraulic line at power unit. Put
pressure line in a large container and cycle pump.
If no output, check the pump motor coupling, which
may be defective, and correct as necessary. If
pump is worn, consult factory for replacement
parts service.
a. Lower the platform onto its maintenance props.
Remove the solenoid valve and clean. (Refer to
Hydraulic Section of Owner's Manual).
b. Correct as necessary. (See also, 1(f), (h).
c . See 1(b).
d. See 1(e).
e. See 1(j).
a. See 1(b).
b. Check that one leg of the motor lines is not
connected to ground. Check motor leads for proper
connection for the voltage being supplied; 1(a).
c . See 1(d), (f), (g), (h), (j).
d. Align cylinders correctly.
a. See 1(d), (f), (g), (j).
b. See air bleed procedure p.9.
a. Remove Solenoid Valve and clean filter.
b. Correct as necessary. (In case of pipe, check for
obstruction in line.)
c . Remove and clean Flow Control Valve. (Refer to
Hydraulic Section of Owner's Manual).
d. Align cylinders correctly.
e. Remove and clean Velocity Fuse. (Refer to
Hydraulic Section of Owner's Manual.)
TROUBLESHOOTING GUIDE FOR HYDRAULIC EQUIPMENT
BEFORE PREFORMING ANY MAINTENANCE WORK ALWAYS INSTALL MAINTENANCE SAFETY BLOCKS
Содержание EHLTT Series
Страница 3: ...3 ELECTRICAL SCHEMATIC ...
Страница 4: ...4 PRIMARY WIRING FOR CONTROL TRANSFORMER ...
Страница 5: ...5 POWER CONVERSION ...
Страница 7: ...7 HYDRAULIC SCHEMATIC ...