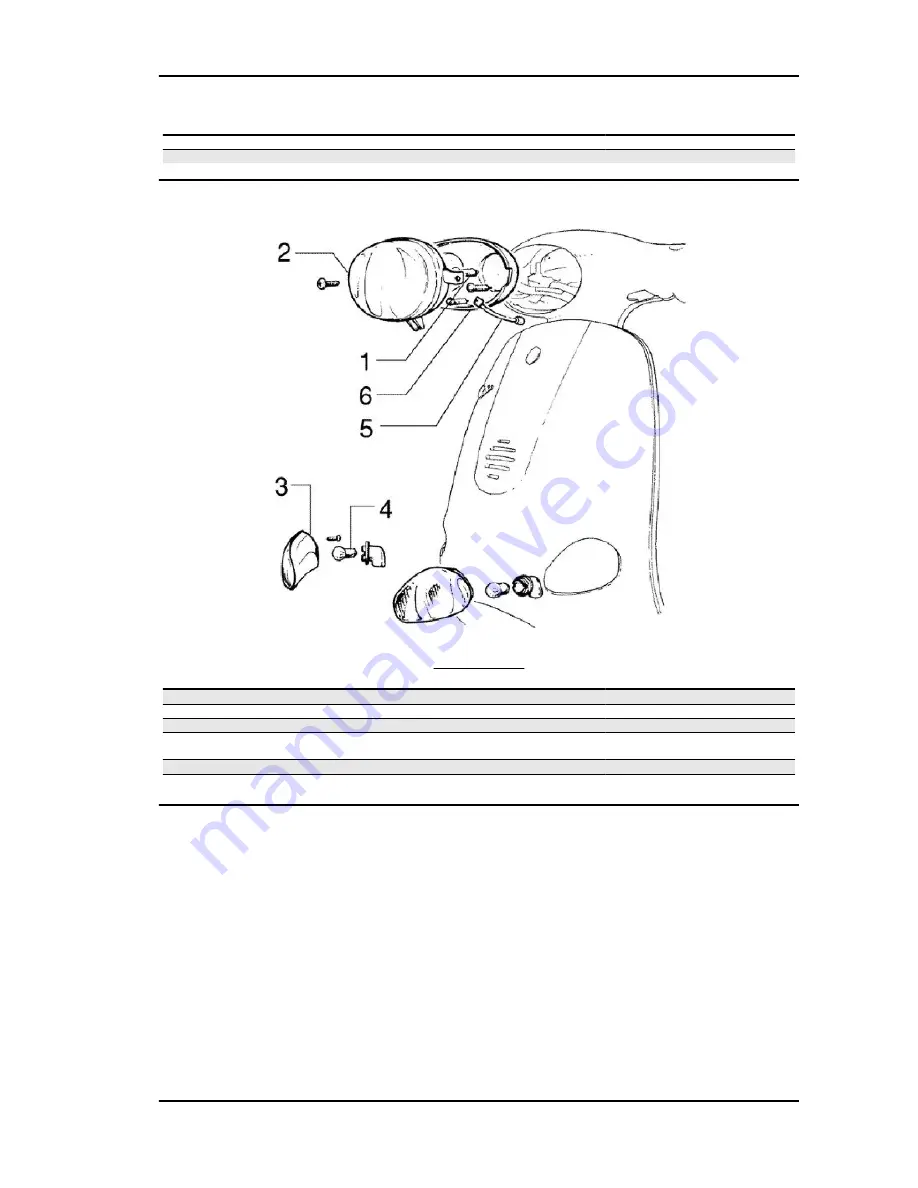
Code
Action
Duration
4
003063
Tyre pressure - Check
5
006018
Wheel rim - Paintwork
Electric devices
HEADLIGHT
Code
Action
Duration
1
005008
Front headlamp bulbs - Replacement
2
005002
Front headlamp - Replacement
3
005012
Front turn indicator - Replacement
4
005067
Front turn indicator bulb - Replace-
ment
5
005044
Front lights cable unit- Replacement
6
004020
Headlight frame - Replacement
ET4 50
Time
TIME - 175
Содержание ET4 50
Страница 1: ...WORKSHOP MANUAL 633367 ET4 50 ...
Страница 4: ......
Страница 6: ...INDEX OF TOPICS CHARACTERISTICS CHAR ...
Страница 16: ...INDEX OF TOPICS TOOLING TOOL ...
Страница 24: ...INDEX OF TOPICS MAINTENANCE MAIN ...
Страница 33: ...494929Y Exhaust fumes analyser 020331Y Digital multimeter ET4 50 Maintenance MAIN 33 ...
Страница 34: ...INDEX OF TOPICS TROUBLESHOOTING TROUBL ...
Страница 40: ...INDEX OF TOPICS ELECTRICAL SYSTEM ELE SYS ...
Страница 56: ...INDEX OF TOPICS ENGINE FROM VEHICLE ENG VE ...
Страница 58: ...INDEX OF TOPICS ENGINE ENG ...
Страница 120: ...INDEX OF TOPICS SUSPENSIONS SUSP ...
Страница 130: ...INDEX OF TOPICS BRAKING SYSTEM BRAK SYS ...
Страница 136: ...INDEX OF TOPICS CHASSIS CHAS ...
Страница 144: ...INDEX OF TOPICS PRE DELIVERY PRE DE ...
Страница 148: ...INDEX OF TOPICS TIME TIME ...
Страница 150: ...Crankcase CRANKCASE Code Action Duration 1 001133 Engine crankcase replace Crankshaft Time ET4 50 TIME 150 ...
Страница 184: ...BRAKE LEVER Code Action Duration 1 002002 Shoes Rear brake pads Replace ment Time ET4 50 TIME 184 ...