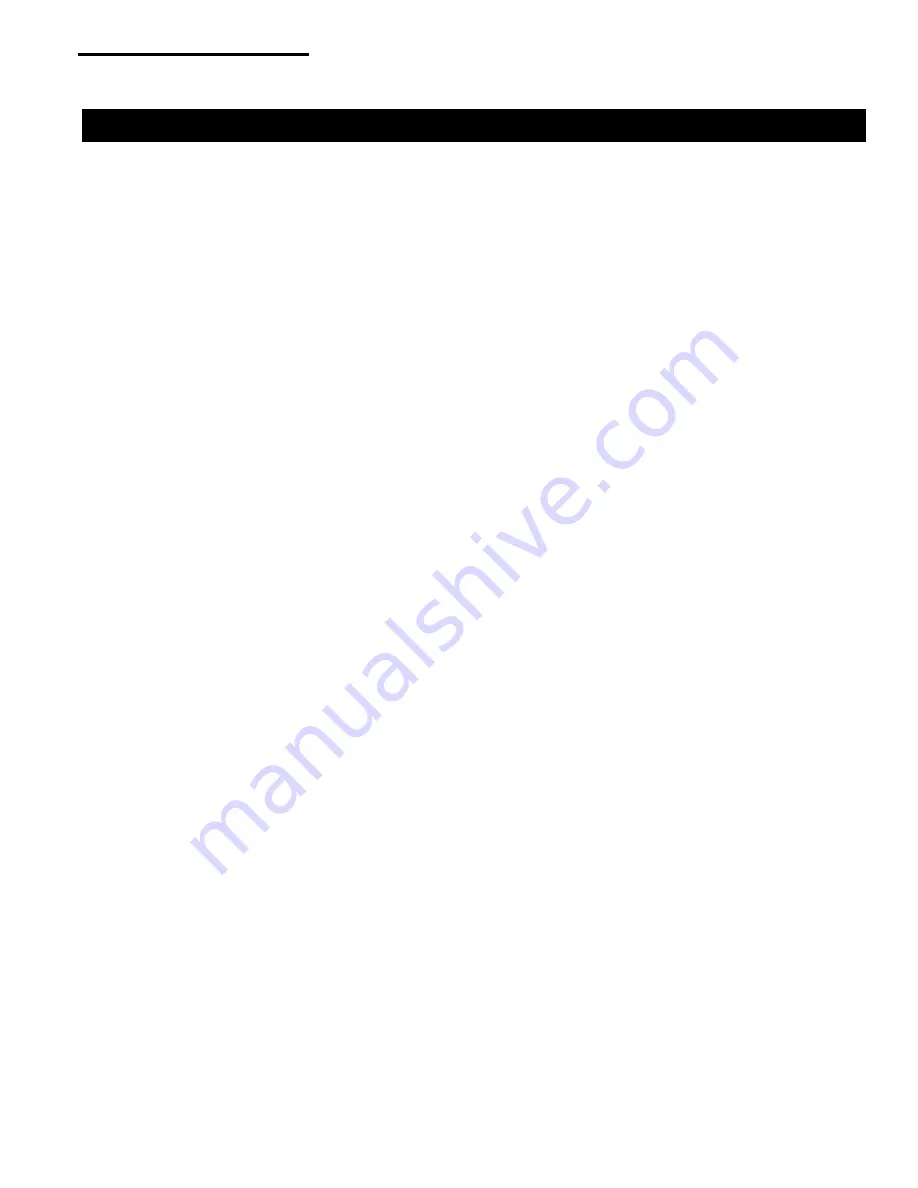
3
Vermont Castings Jefferson Direct Vent/Natural Vent Gas Heater
20002191
The Jefferson Direct Vent/Natural Vent Room Heater,
Model Nos. 2820, 2822, 2823, 2825, 2827 and 2828, is a
vented gas appliance listed to the ANSI Standard Z21.88b-
2001 and CSA-2.33b-2001 for Vented Room Heaters, and
CSA 2.17-M91, Gas-Fired Appliances For Use at High Alti-
tudes.
The installation of the Jefferson Direct Vent/Natural Vent
Room Heater must conform with local codes, or in the ab-
sence of local codes, with National Fuel Gas Code, ANSI
Z223.1 — latest edition and CSA B-149.1 Installation Code.
(EXCEPTION: Do not derate this appliance for altitude.
Maintain the manifold pressure at 3.5 inches w.c. for Natu-
ral Gas and 10 inches w.c. for LP gas at maximum input.)
This appliance is only for use with the type of gas indi-
cated on the rating plate. This appliance is not convertible
for use with other gases unless a certified kit is used.
Installation and replacement of gas piping, gas
utilization equipment or accessories, and repair and
servicing of equipment shall be performed only by a
qualified agency. The term “qualified agency” means
any individual, firm, corporation, or company that either
in person or through a representative is engaged in
and is responsible for (a) installation or replacement of
gas piping, or (b), the connection, installation, repair,
or servicing of equipment, who is experienced in such
work, familiar with all precautions required, and has
complied with all the requirements of the authority
having jurisdiction.
The Jefferson Direct Vent/Natural Vent Room Heater
should be inspected before use and at least annually
by a qualified service agency. It is imperative that
control compartments, burners, and circulating air
passageways of the appliance be kept clean.
The Jefferson Direct Vent/Natural Vent Room Heater
and its individual shut-off valve must be disconnected from
the gas supply piping during any pressure testing of that
system at test pressures in excess of 1/2 psig (3.5 kPa).
The Jefferson Direct Vent/Natural Vent Room Heater
must be isolated from the gas supply piping system by clos-
ing its individual manual shutoff valve during any pressure
testing of the gas supply piping system at test pressures
equal to or less than 1/2 psig.
'Direct Vent' describes a sealed combustion system in
which incoming outside air for combustion and outgoing
exhaust enter and exit through two separate concentric
passages within the same sealed vent system. The sys-
tem does not use room air to support combustion. The
Direct Vent system permits the gas appliance to be vented
directly to the outside atmosphere through the side of the
house or vertically through the roof. Conventional venting
systems (Natural Vent) take air from the room for combus-
tion and vent the exhaust vertically through the roof to the
atmosphere.
This appliance is approved for bedroom installations in
the U.S. and Canada.
This appliance may be installed in an aftermarket*
manufactured (mobile) home, where not prohibited by
state or local codes.
WARNING: Operation of this heater when not con-
nected to a properly installed and maintained venting
system can result in carbon monoxide (CO) poisoning
and possible death.
The Jefferson Direct Vent/Natural Vent Room Heater,
when installed, must be electrically grounded in accordance
with local codes or, in the absence of local codes, with the
National Electrical Code ANSI/NFPA 70, (latest edition), or
of the current Canadian Electrical Code C22.1.
Due to high temperatures this appliance should be
located out of traffic and away from furniture and
draperies.
WARNING: This appliance is hot while in operation.
Keep children, clothing, and furniture away. Contact
may cause burns or ignition of combustible materials.
Children and adults should be alerted to the hazards
of high surface temperatures and should stay away to
avoid burns or clothing ignition. Young children should
be carefully supervised when they are in the same
room as the appliance.
Clothing or other flammable materials should not be
placed on or near the appliance.
Any safety screen, glass or guard removed for
servicing an appliance must be replaced prior to
operating the appliance.
The appliance area must be kept clear and free from
combustible materials, gasoline, and other flammable
vapors and liquids.
The flow of combustion and ventilation air must not
be obstructed. The installation must include adequate
accessibility and clearance for servicing and proper
operation.
WARNING: Do not operate the Room Heater with the
glass panel removed, cracked or broken. Replacement
of the panel should be done by a licensed or qualified
service person.
Do not use this appliance if any part has been under
water. Immediately call a qualified service technician
to inspect the appliance and to replace any part of the
control system and any gas control which has been
under water.
Do not burn wood, trash or any other material for
which this appliance was not designed. This appliance
is designed to burn either natural gas or propane only.
This gas appliance must not be connected to a chimney
flue serving a separate solid-fuel burning appliance.
CAUTION: Label all wires prior to disconnection
when servicing controls. Wiring errors can cause
improper and dangerous operation.
Verify proper operation after servicing.
Proposition 65 Warning: Fuels used in gas,
woodburning or oil fired appliances, and the products of
combustion of such fuels, contain chemicals known to the
State of California to cause cancer, birth defects and other
reproductive harm.
California Health & Safety Code Sec. 25249.6
*
Aftermarket: Completion of sale, nor for purpose of resale,
from the manufacturer.
Installation & Operating Instructions