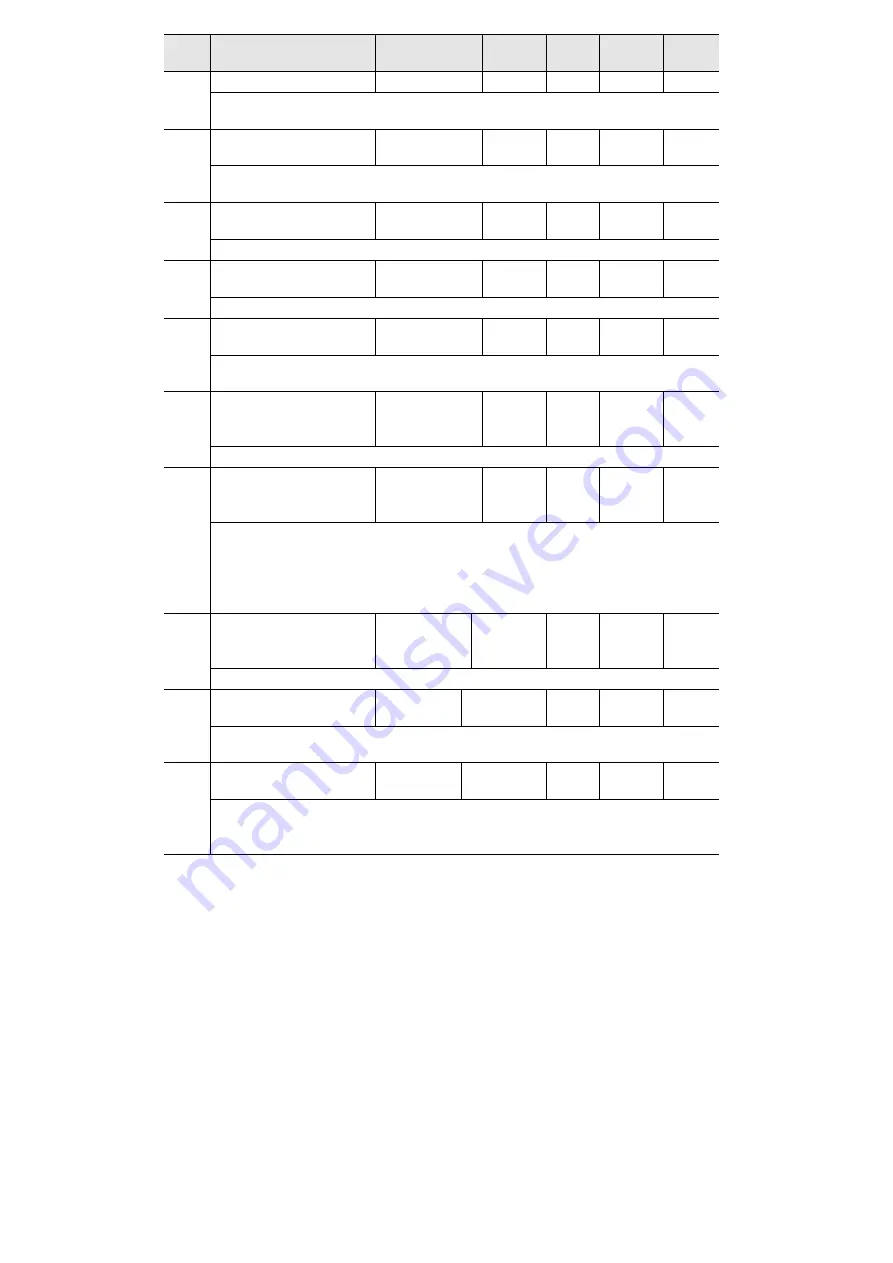
26
Function
code
Parameter name
Range
Default value Company Postal address
Effective
way
feedforward gain
effect
The forward position instruction is used to adjust the forward response individually. When the parameter is used, the
torque feedforward increases rapidly, and the positioning time can be shortened appropriately.
Pn245
Model tracking control reverse torque
feedforward gain
0~1000
100.0
%
0x0245
Immediate
effect
When the negative position instruction is used to adjust the negative response individually, using this parameter, the
torque feedforward increases rapidly, and the positioning time can be shortened appropriately.
Pn246
Second model tracking control gain
1~2000
50.0
1/s
0x0246
Immediate
effect
When the model is valid, the second gain is used.
Pn247
Second model tracking control
attenuation coefficient
50~200
100.0
%
0x0247
Immediate
effect
When the model is valid, the second gain is used.
Pn249
Speed feedforward / torque
feedforward selection
0x00~0x01
0
-
0x0249
Immediate
effect
0- does not use model tracking control and external speed and torque feedforward at the same time 1- using model
tracking control and external speed and torque feedforward at the same time
Pn250
External encoder for full closed loop
control
Use method
0~3
0
-
0x0250
Power
failure
effective
0-Do not use full closed loop function 1- to use in standard operation direction 2-to use in reverse direction of operation.
Pn252
Coefficient of deviation between
motor loads during one full-closed
rotation
0~100
20
%
0x0252
Immediate
effect
This parameter indicates the coefficient processing of the motor-load deviation after setting the motor for 1 revolution. If
this parameter is set to 0%, the deviation after one revolution is 1000. At the beginning of the second run, the deviation is
accumulated based on 1000 and set to 20%.
Accumulate based on the deviation of 200 (1000 20%
200
) at the start
of the second run. The setting of this value may be too large to detect Er.d10 normally. It is necessary to set the tolerance
setting according to the load and inter motor installation.
Pn253
External grating resolution
4~1048576
32768
Pulse/r
0x0253
0x0254
Power
failure
effective
Set the resolution of the external scale when the motor runs for 1 revolution (after 4 times the frequency).
Pn257
Excessive deviation between motor
and load
0~1073741824
1000
Command
unit
0x0257
0x0258
Immediate
effect
Set the alarm threshold of excessive motor-load deviation. If the value is set too small, Er.d10 may be detected by
mistake.
Pn260
Location close to signal width
1~1073741824
1073741824
Command
unit
0x0260
0x0261
Immediate
effect
During position control, the host device can receive the positioning approach signal before confirming the positioning
completion signal, preparing for the sequence of operations after positioning completion, which can reduce the time
required for the operation when positioning is completed, the number of command pulses and servo The signal is output
Содержание SD700-1R1A series
Страница 10: ...10 1 10 Example of location control connection...
Страница 11: ...11 1 11 Example of speed control connection...
Страница 12: ...12 1 12 Example of torque control connection...