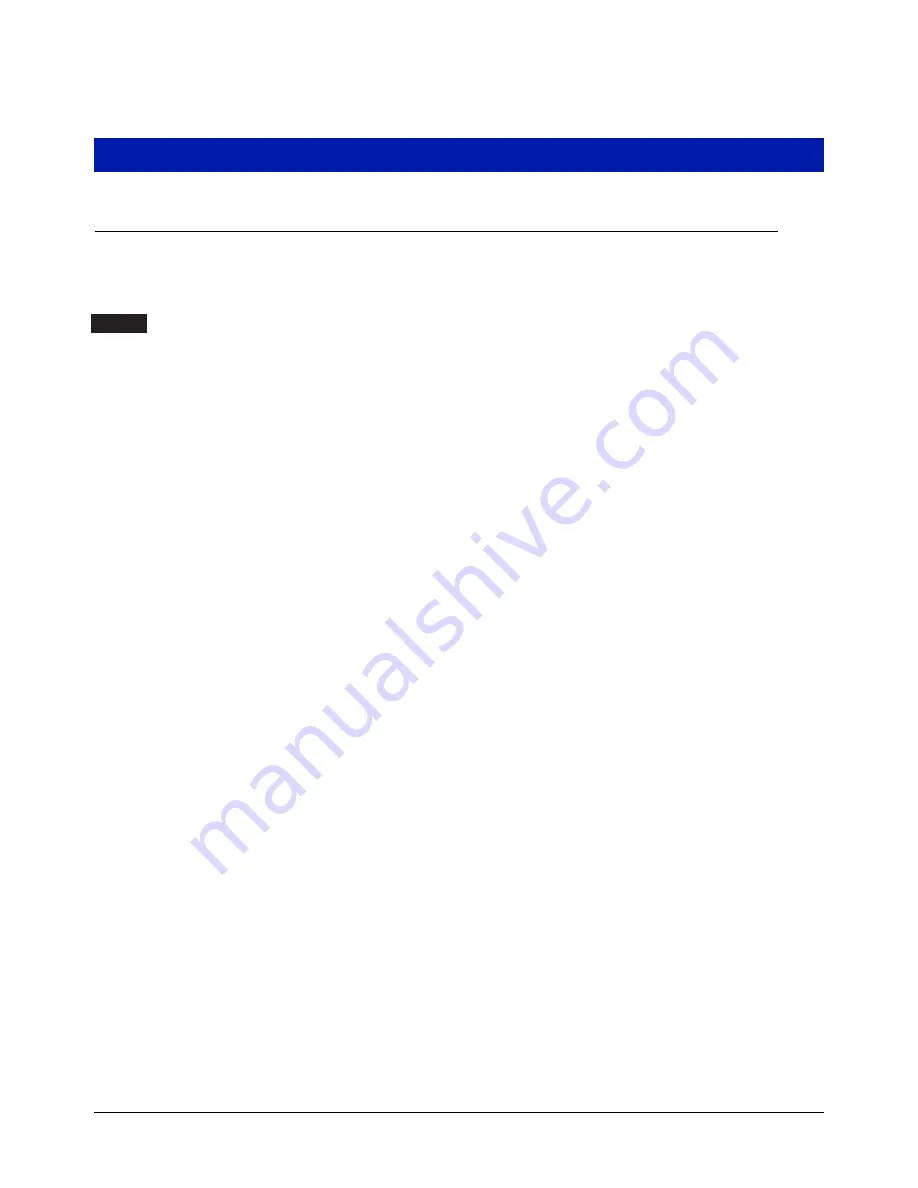
1
Introduction
Overview
The Red Jacket Submersible Turbine Pump (STP) assembly for international markets is engineered for advanced
safety, environmental protection, serviceability and flow. The Red Jacket STP fits 4-inch NPT threaded thin-wall
risers and is available in a variety of horsepowers and lengths.
This information is generated as a consequence of carrying out the ignition hazard assessment.
Newly designed safety features of The Red Jacket STP
Industry-leading design enhancements for the Red Jacket submersible motor and The Red Jacket STP enable the
latest European ATEX safety standards (EN 15268) to be easily complied with. The motor has Encapsulation and
Increased Safety protections using increased isolation and clearances between electrical and moving components
to reduce the possibility of generating sparks in addition to Flameproof protection with the structural strength and
tightness to withstand and contain an explosion.
The unique design enhancements have created multiple levels of safety protection allowing The Red Jacket
Submersible Turbine Pump to be certified to be safe and reliably operated even in the most risky and adverse
conditions – when a gas group IIA fuel storage tank nears being empty and contains potentially explosive vapors.
The pump staging is designed with electrically conductive materials to prevent creation of static electricity.
The packer’s extractable section incorporates Increased Safety and Flameproof protections utilizing an improved
electrical yoke connection that provides a secondary vapor barrier to prevent fuel vapors from the tank entering the
manifold’s electrical compartment. In the event of improper power supply shut off during extraction of the pump
assembly, it also prevents electrical sparks from coming into contact with vapors or fuel that may be present in the
tank chamber or manhole. Separation of Zone 0 (inside the storage tank) and Zone 1 (tank chamber or manhole) is
accomplished by the male connector partition wall between the packer and manifold connection. Connection of
the UMP wiring is within the Zone 0 boundary (Category 1) and Increased Safety measures inside the flameproof
enclosure must be ensured during field wiring connections. The manifold is certified as Category 2 equipment for
Zone 1 areas.
An external connection terminal for an equipotential bonding conductor is provided on the side of the manifold.
Service spill elimination
The check valve can be raised to provide a larger path to depressurize the line and return fuel to the tank.
Vacuum monitoring applications
The vacuum sensor-siphon is a monitoring-grade siphon system. It is designed specifically for use in vacuum
monitoring applications and to integrate with vacuum sensors. The two-port vacuum sensor-siphon system
incorporates a check valve poppet assembly with an inline filter screen that reduces the clogs and failures that can
cause false alarms and downtime in vacuum monitoring applications.
Plug-in yoke electrical connection
Safety practice when servicing other STPs requires turning off the circuit breaker, backing off the bolts by up to
one inch, and then manually pulling the electrical yoke connection apart. With The Red Jacket STP you turn off the
circuit breaker and then simply back off the two nuts holding the extractable in place and the yoke electrical
connection is disconnected as the extractable is removed. After service is complete, the electrical circuit
reconnects when the two nuts are re-tightened. Safe, simple and easy.
NOTICE