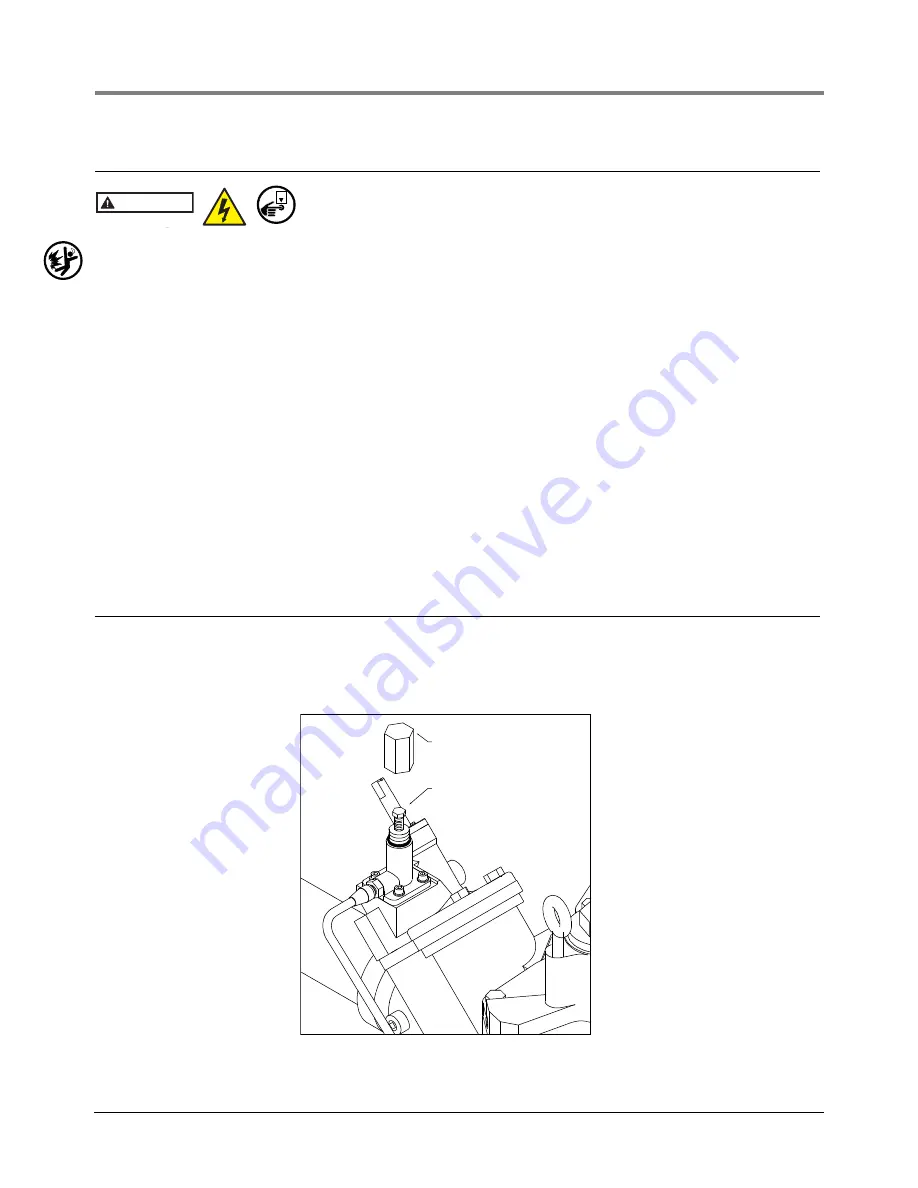
Testing the Installation
Testing the Tank
27
Testing the Tank
Disconnect, lock out, and tag power at the panel before servicing the
pump.
When servicing equipment, use non-sparking tools and use caution when removing or installing
equipment to avoid generating a spark.
1.
Lock down the pump check valve by turning the check valve lock down screw clockwise as far as it will turn
(see Figure 17).
2.
Remove the Tank Test Plug from the riser flange.
3.
Apply tank test pressure at the tank test port.
4.
After the completion of the test, release the pressure by:
a.
Turning the check valve lock down screw counter clockwise as far as it will go.
b.
Remove the protective cover from the Pressurstat (see Figure 18) and turn the Pressurstat adjustment
screw counter clockwise until the screw protrudes 3/4”, this will relieve the line pressure to “0” psi.
Apply an adequate amount of fresh, UL classified for petroleum, non-setting thread sealant on the 1/4”
NPT line test port plug and replace it. Torque the plug to 14 - 24 ft-lbs (19.4 - 29 N•m).
Adjust desired relief pressure per instructions on page 28 and replace the protective cover.
Purging the System
1.
Pump a minimum of fifteen gallons (57 liters) of product through each dispenser.
2.
Start with the dispenser furthest from the pump and work toward the pump.
Figure 18. Pressurstat - Pressure Adjustment
OFF
WARNING
rj/051-301-20.eps
Protective cover
Adjustment screw
(as shown 0 - 3 psi setting)
Содержание Red Jacket Maxxum Big-Flo Quick-Set Series
Страница 47: ......
Страница 50: ...For technical support sales or other assistance please visit www veeder com...