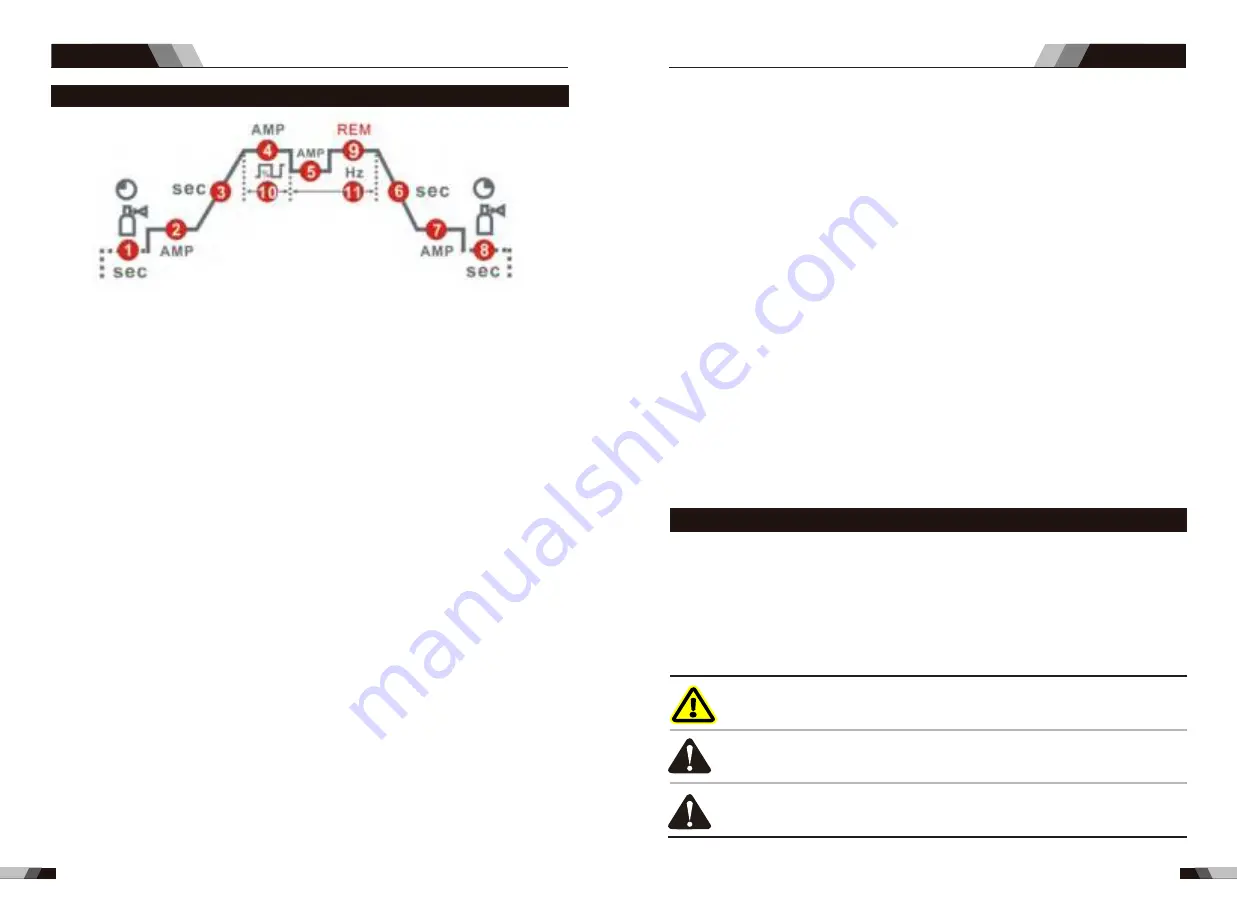
16
17
.
Gas Pre-Flow
1
Absolute setting range 0.1s to 5s (0.1S increments)
This parameter operates in TIG modes only and is used to provide gas to the weld zone
prior to striking the arc, once the torch trigger switch has been pressed. This control is
used to dramatically reduce weld porosity at the start of a weld.
2.Initial Current
The main current Setting range 10AMP to 170AMP
This parameter operates in (4T) TIG modes only and is used to set the start current for TIG.
The Start Current remains on until the torch trigger switch is released after it has been
depressed.
Note: The maximum initial current available will be limited to the set value of the base
Operation
Operation
DC PULSE
SERIES
EQUIPMENT
DC PULSE
SERIES
EQUIPMENT
3.Up Slope
Setting ranges :0.1S-10S (0.1S increments)
This parameter operates in (2T and 4T) TIG modes only and is used to set the time for the
weld current to ramp up, after the torch trigger switch has been pressed then released,
from Initial Current to High or base current.
4.Peak Current
Setting ranges
O241:10AMP to 170AMP (DC TIG mode), 10 to 170A (AC HF TIG mode)
This parameter sets the TIG WELD current. This parameter also sets the STICK weld
current.
5.Base Current
Setting ranges
O241:10AMP to 170AMP (DC TIG mode), 10AMP to 170AMP (AC HF TIG mode)
Secondary current (TIG)/pulse pause current.
6.Down Slope
Setting ranges 0.1-10s
This parameter operates in TIG modes only and is used to set the time for the weld current
to ramp down, after the torch trigger switch has been pressed to end current. This control
is used to eliminate the crater that can form at the completion of a weld.
7.End current
Setting ranges 10A-170A
This parameter operates in (4T) TIG modes only and is used to set the finish current for TIG.
The end Current remains ON until the torch trigger switch is released after it has been
depressed.
Note: The maximum crater current available will be limited to the set value of the base
current.
8.Post Flow
9. Remote Control
Setting ranges 1-10S
The system independently identifies the remote control, and when the indicator light is
on, the welding current can be adjusted by remote (foot or welding gun).
This parameter operates in TIG modes only and is used to adjust the post gas flow
time once the arc has extinguished. This control is used to dramatically reduce
oxidation of the tungsten electrode.
10.Pulse Width
Setting ranges 10%-90%
This parameter sets the percentage on time of the PULSE FREQUENCY for High
weld current when the PULSE is ON.
11.Pulse Frequency
Setting ranges 1HZ -200HZ
This parameter sets the PULSE FREQUENCY when the PULSE is ON.
3.3 Setup For STICK (MMA) Welding
WARNING
Before connecting the work clamp to the work and
inserting the electrode in the electrode holder make
sure the mains power supply is switched off.
CAUTION
CAUTION
Remove any packaging material prior to use. Do not
block the air vents at the front or rear of the Welding
Power Source.
Loose welding terminal connections can cause
overheating and result in the male plug being fused
in the bayonet terminal.
For Alkaline Electrode,connect the electrode holder to the positive welding termimal
Electrode,please connect the electrode holder to the negative welding termimal and
manufacturer. Welding current flows from the Power Source via heavy duty bayonet type
terminals. It is essential, however, that the male plug is inserted and turned securely to
achieve a sound electrical connection. Select STICK mode with the process selection
control.
a n d c o n n e c t t h e w o r k l e a d t o t h e n e g a t i v e w e l d i n g t e r m i n a l , w h i l e f o r t h e A c i d
connect the work lead to the positve welding terminal.If in doubt consult the electrode
3.2 Control Panel