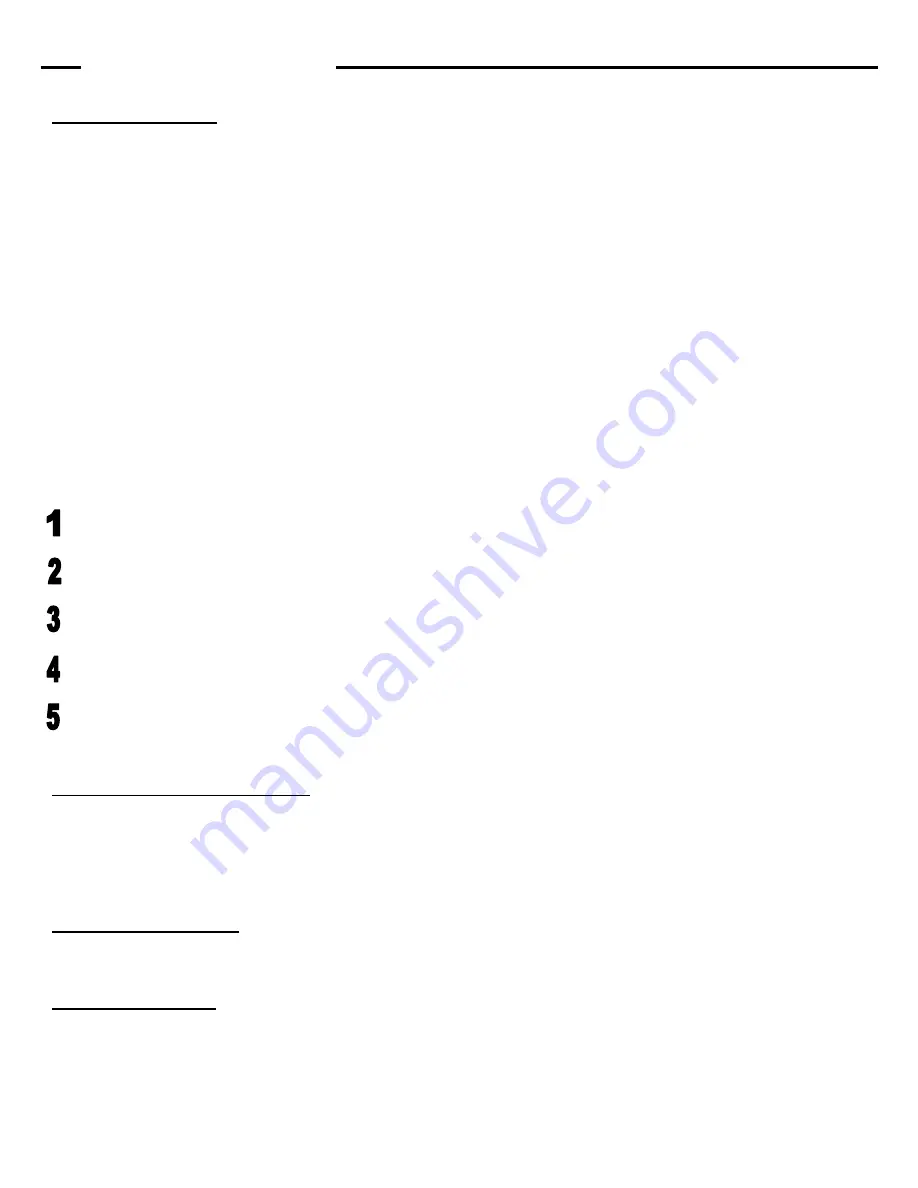
Curing Plastisol with infrared:
Plastisol ink can fully cure in approximately 20-30* seconds. The ink must achieve 310°-320°F (154
°-160°C)
to cure and fuse to
the garment. We recommend* a starting temperature 800°F (427
°C)
, 3” heater height and a belt speed of 25 seconds in the
chamber
Discharge or water based:
Water based products require more time than plastisol to cure due to the fact that the water/moisture must be evaporated before
the ink can cure. We have seen cure times from 50 to 90* seconds to achieve a full cure or discharge and not damage the gar-
ment. Please note as the time is increased the temperature must be decreased to protect the garment from scorching.
*Actual cure times can vary depending on conditions such as garment moisture and color, ink color, ink thickness, and
environmental conditions. All three variables should be used to maximize production while insuring a proper cure.
How to determine Temperature set point:
The sensor is located directly under the heater so it will read a much higher temperature than seen at the garment. Set the tem-
perature several hundred degrees higher to compensate for this difference. A non contact heat gun can be used to read the
temperature of the ink at the end of the dryer while it is still under the last heater. Take into consideration the thickness of the
ink when using the heat gun. It will measure the top layer of the ink. If the ink is very thick you must add a buffer to be sure cure
temperature is reached throughout the ink. Temperature set point, heater distance to the garment, and belt speed will all effect
the ink temp.
Operation Tips
While machine is in operation, it is necessary to have the belt moving while the heater is above 300°F(149°C).
Allow approximately 15 minutes for dryer to reach 700°F - 800°F (371° - 427°C).
If no garments are being run through the dryer for more than 10 minutes, it is recommended to lower the heat set point
to 500°F (260°C). It will take approximately 10 minutes to return to operating temperature.
Periodically check ink temperature at the exit of the dryer. It is recommended that you check the temperature of the ink
towards the outside of the printed image.
When checking temperature with a laser gun, shoot the ink while it is still under the heater
Startup Procedure
Turn on Power Switch
:
Power is sent to the heater switch, belt speed controller, and the exhaust fan will start.
Turn on Conveyor
:
Set speed to desired setting.
Turn on Heat Switch
:
Turn on the Temperature Controllers.
Check belt path:
Remove any objects from the conveyor and belt.
Control System Summary:
The control system in your dryer is called a “closed loop system”. The system includes a Digital Controller mounted to the
control panel, a Sensor mounted in a shield under the heater, a relay and an Infrared Heater. The digital controller is set to
the desired temperature and the Sensor measures the temperature at the face of the heater. The sensor reports back to the
control, and the relay switches the heat on and off to the heater.
Rotate main power
switch to ON:
The red Power Light will illuminate. Main Power Switch located on side of control box.
Dryer Operation
(1of2)
Pg. 14