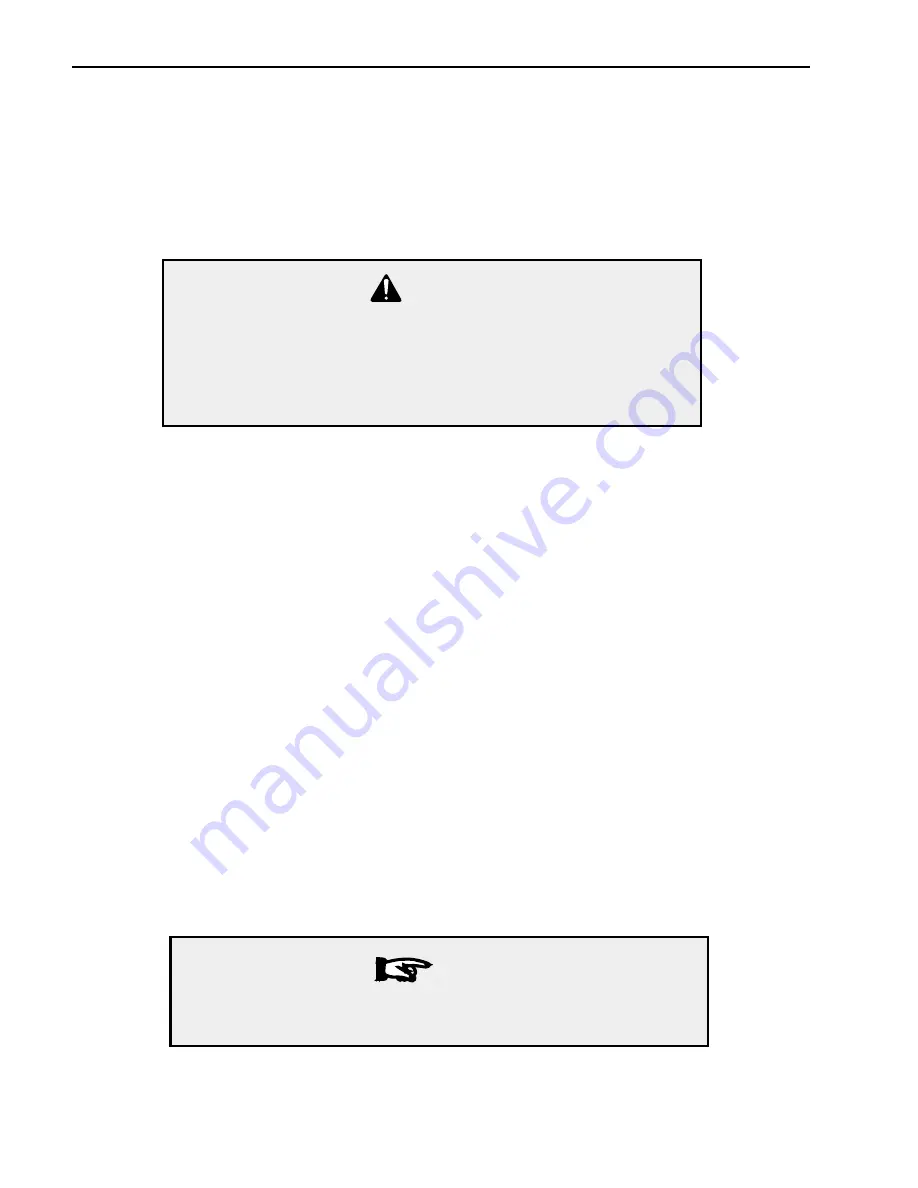
Specifications and Installation
1-4
1-2-2 Pump Oil Installation
a
The recommended oil charge for the VHS-10 and the VHS-400 diffusion pumps is 1000 cc.
b
The oil is normally poured into the pump inlet or the foreline or by removing the fill plug and
pouring it into the fill and drain assembly.
1-2-3 Vacuum System Connections
a
The diffusion pump must be installed with the body vertical and plumb. Check to ensure that
the pump inlet mating flange on the system is horizontal within ± one degree. The boiler plate
must be horizontal to prevent uneven fluid level. Failure to meet this requirement could result
in overheating of the diffusion pump boiler plate.
b
Prepare the inlet and foreline O-rings by wiping them with a clean, lint-free cloth. A small
amount of diffusion pump oil may be used to clean the O-rings.
c
Install the O-rings in the O-ring grooves. Be careful not to damage or scratch the sealing surface.
d
Check the fill plug for tightness. Apply light to medium torque, enough to compress the O-rings.
e
Using the appropriate lifting apparatus, align the bolt holes of the inlet flange with the bolt
holes of the mating flange. Using the appropriate mounting hardware, tighten the bolts evenly
until the O-ring is compressed and the flanges make light, metal-to-metal contact.
f
To ensure the integrity of the vacuum connections, they should be checked for leaks using a
helium mass spectrometer leak detector before operating the vacuum system.
1-2-4 Cooling Water Connections
a
The inlet water fitting (near the inlet flange at the top of the pump) should be connected to a
continuously running water supply at 0.4 gpm and at a temperature of 60 to 80°F.
WARNING
_____________
Utility failure can cause damage to the equipment, overheating, and
explosions. Designers of the equipment using diffusion pumps must
take appropriate system design action to protect personnel and prop-
erty from possible hazards.
Read the safety section at the beginning
of this manual.
NOTE
________
In the following step, discharge connections must be installed in accor-
dance with all Federal, State, and local laws and regulations.
Содержание VHS-10
Страница 13: ...x ...
Страница 25: ...Maintenance and Service 3 3 Figure 3 1 Jet Assembly VHS 10 and VHS 400 Pumps ...
Страница 28: ...Maintenance and Service 3 6 ...
Страница 33: ...Replacement Parts 5 3 Figure 5 1 Wiring Diagram VHS 400 Diffusion Pump ...
Страница 36: ...Replacement Parts 5 6 Old Style Typical New Style Typical Figure 5 5 Fill and Drain Assemblies ...