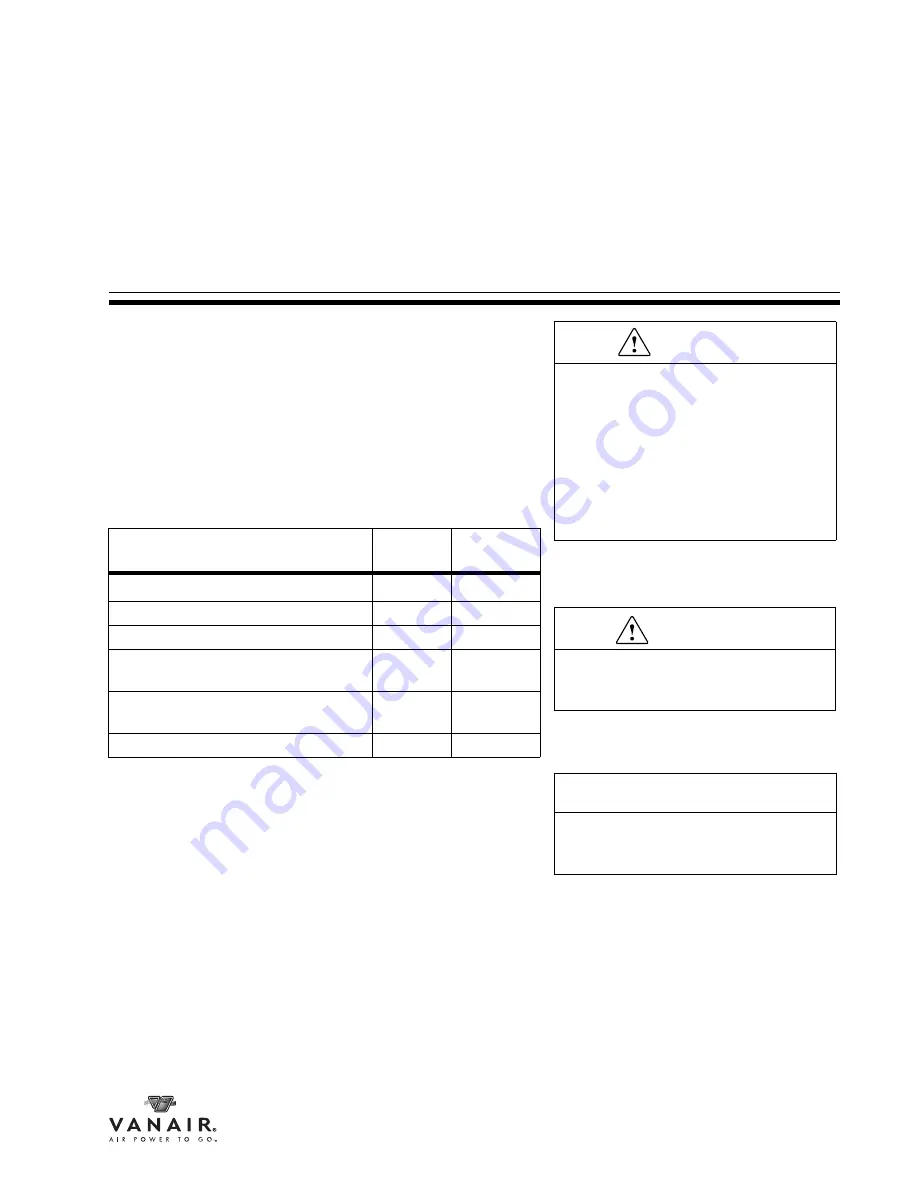
AIR N ARC
®
200 SERIES ALL-IN-ONE POWER SYSTEM
®
SECTION 6: MAINTENANCE
090019-OP_r0
PAGE - 55
6.1 GENERAL INFORMATION
A strict maintenance program is the key to long life for the
Air N Arc 200 Series All-In-One Power System package.
Below is a program that, when adhered to, should keep
the package in top operating condition. Refer to
Section
6.5, Parts Replacement and Adjustment Procedures
in this section of the manual for detailed descriptions of
specific compressor system components. The following
table lists the main topics in order of appearance for this
section:
6.2 ROUTINE MAINTENANCE
SCHEDULE
Vanair
®
Manufacturing, Inc. considers the maintenance
schedule given in
Section 6.3, Maintenance Schedule
Table
, to be part of the warranty agreement with the
customer. This maintenance regimen must be followed in
order to protect the warranty of the machine package.
Vanair Manufacturing, Inc. especially requires that a
consistent service regimen be established for engine oil
changes, and engine and compressor air filter servicing.
The following schedule is designed so that many of the
other maintenance tasks are completed when the engine
and compressor air filters are serviced, and the engine oil
is changed.
System Component or
Component Group
Manual
Section
Location
Routine Maintenance Schedule
6.2
page 55
Maintenance Schedule Table
6.3
page 57
Replacement Parts
6.4
page 64
Parts Replacement and Adjustment
Procedures
6.5
page 61
Servicing the System Fuses and Cir-
cuit Breakers
6.6
page 96
Storage and Intermittent Use
6.7
page 98
SECTION 6: MAINTENANCE
WARNING
DO NOT remove caps, plugs and/or other
components when compressor is
running or pressurized. Stop compressor
and de-pressurize system prior to
maintenance of system.
Wear personal protective equipment
such as gloves, work boots, and eye and
hearing protection as required for the
task at hand.
NOTE
Operating the machine package in a
severe environment may require more
frequent service intervals.
WARNING
Follow all applicable safety
recommendations as outlined in
Section
1: Safety
of this manual.
Содержание AIR N ARC RELIANT 250 Series
Страница 3: ...Addendum 090044 AIR N ARC 250 SERIES ALL IN ONE POWER SYSTEM ADDENDUM PAGE III BLANK PAGE...
Страница 18: ...GLOSSARY AIR N ARC 200 SERIES ALL IN ONE POWER SYSTEM PAGE X 090019 OP_r0 BLANK PAGE...
Страница 22: ...WARRANTY PROCEDURE AIR N ARC 200 SERIES ALL IN ONE POWER SYSTEM PAGE XIV 090019 OP_r0 BLANK PAGE...
Страница 56: ...SECTION 3 SPECIFICATIONS AIR N ARC 200 SERIES ALL IN ONE POWER SYSTEM PAGE 34 090019 OP_r0 BLANK PAGE...
Страница 76: ...SECTION 5 OPERATION AIR N ARC 200 SERIES ALL IN ONE POWER SYSTEM PAGE 54 090019 OP_r0 BLANK PAGE...
Страница 132: ...SECTION 7 TROUBLESHOOTING AIR IN ARC 200 SERIES ALL IN ONE POWER SYSTEM PAGE 110 090019 OP_r0 BLANK PAGE...
Страница 139: ...AIR N ARC 200 SERIES ALL IN ONE POWER SYSTEM SECTION 9 ILLUSTRATED PARTS LIST 090019 OP_r0 PAGE 117 NOTES...
Страница 168: ...SECTION 9 ILLUSTRATED PARTS LIST AIR N ARC 200 SERIES ALL IN ONE POWER SYSTEM PAGE 146 090019 OP_r0 BLANK PAGE...
Страница 178: ...APPENDIX A ADDITIONAL INFORMATION AIR N ARC 200 ALL IN ONE POWER SYSTEM PAGE 156 090019 OP_r0 BLANK PAGE...
Страница 182: ...APPENDIX B MAINTENANCE SERVICE LOG AIR IN ARC 200 ALL IN ONE POWER SYSTEM PAGE 160 090019 OP_r0 BLANK PAGE...
Страница 183: ...BLANK PAGE...