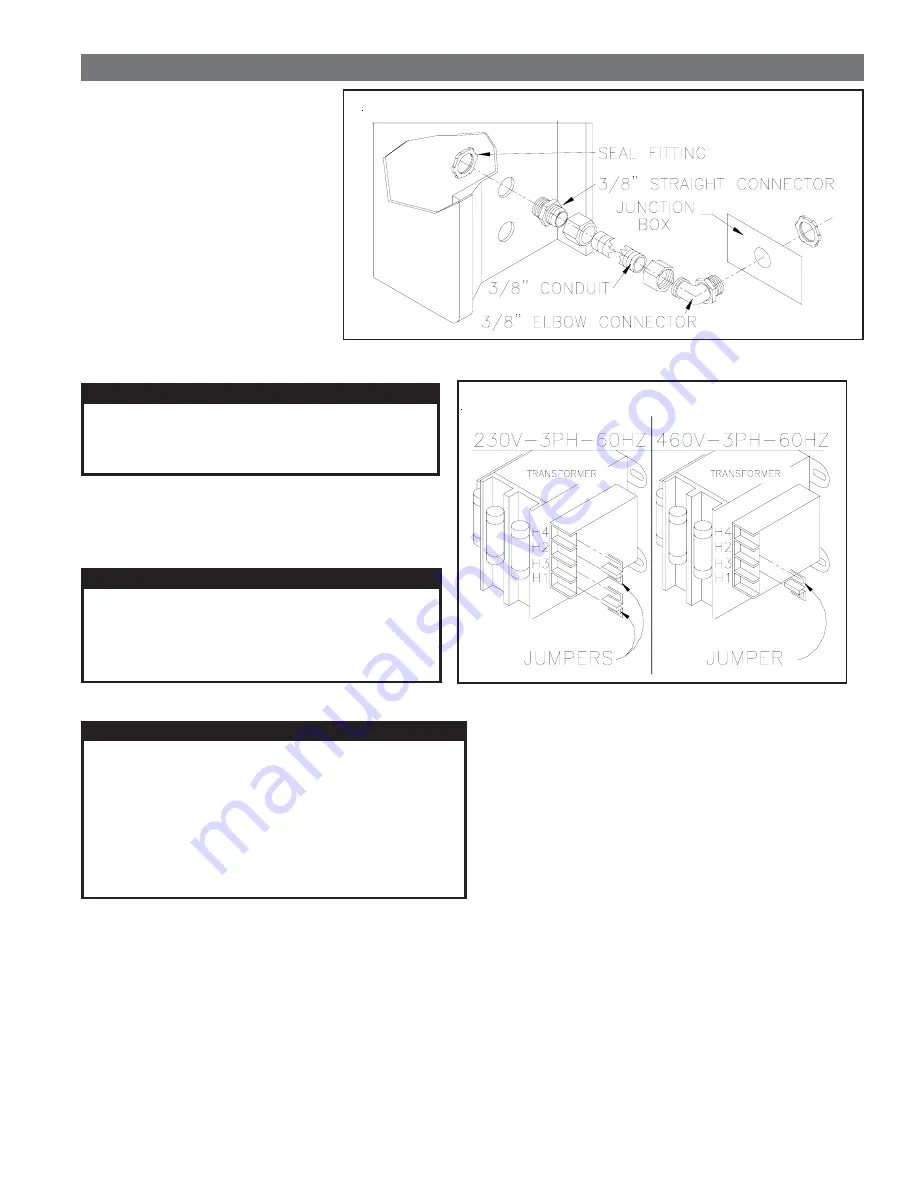
PAGE 3
SECTION 2
INSTALLATION
2.4 INSTALLING THE CONDUIT
Install the straight conduit connector
on the control box. Reference Figure
2-D.
The supplied conduit will be used to
run between the aftercooler and the
control box. Connect the conduit to
the straight connector.
Install the 90 degree elbow connector
on the aftercooler. Reference Figure
2-D.
FIGURE 2-D INSTALLING THE CONDUIT
2.5 INSTALLING THE TRANSFORMER JUMPERS
WARNING
BEFORE STARTING THIS PROCEDURE, TURN OFF
ELECTRICAL POWER. FAILURE TO HEED THIS
WARNING MAY RESULT IN SERIOUS PERSONAL
INJURY AND/OR DAMAGE TO THE UNIT.
This kit was designed to operate at 230V-3PH-60Hz or
460V-3PH-60Hz. Two jumpers were shipped inside the
control box. They must be installed on the transformer
before connecting the power to the control box. Install the
jumper(s) as shown in Figure 2-E for the desired voltage.
CAUTION
It is important that this procedure be properly
completed before continuing with installation.
This kit will not operate without the jumpers.
Damage to the control box will occur if the jumpers
are improperly installed.
FIGURE 2-E INSTALLING THE TRANSFORMER JUMPERS
2.6 ELECTRICAL CONNECTIONS
WARNING
BEFORE STARTING INSTALLATION PROCEDURES
OR ATTEMPTING TO MAKE ANY WIRING CHANGES,
TURN OFF ELECTRICAL POWER. FAILURE TO HEED
THIS WARNING MAY RESULT IN SERIOUS
PERSONAL INJURY AND/OR DAMAGE TO THE UNIT.
WHEN INSTALLING THIS KIT ALWAYS COMPLY WITH
THE NATIONAL ELECTRICAL CODE AND ALL OTHER
APPLICABLE FEDERAL, STATE AND LOCAL CODES.
A 7/8" hole in the top right side of the control box is provided
for incoming power conduit. The hole can be enlarged if
necessary.
The control box is designed for 230V-3PH-60Hz or 460V-
3PH-60Hz operation. The transformer jumpers must be
installed as outlined in Section 2.5 for the desired voltage.
Make the necessary wiring runs and connections for the
main power supply.
Remove the junction box cover on the aftercooler for access
to the junction box. Make the necessary wiring runs through
the conduit from the aftercooler to the control box. Fasten the
conduit to the connector on the aftercooler. Reference
FIGURE 2-D.
Make the wire connections at the junction box on the
aftercooler. Reference FIGURE 2-F. Fasten the junction box
cover to the aftercooler.
Complete the wire connections inside the controller as
shown in FIGURE 2-F.
Once all wiring connections have been properly made, the
rotation of the fan should be checked. The fan must rotate in
the proper direction for maximum performance. Reference
the operator's manual supplied with the aftercooler for the
correct rotation direction. Also, check the aftercooler for a
rotation direction label.
To check the rotation, turn on the power supply to the
aftercooler. If the fan does not rotate in the proper direction,
any two of the power leads to the motor can be switched.