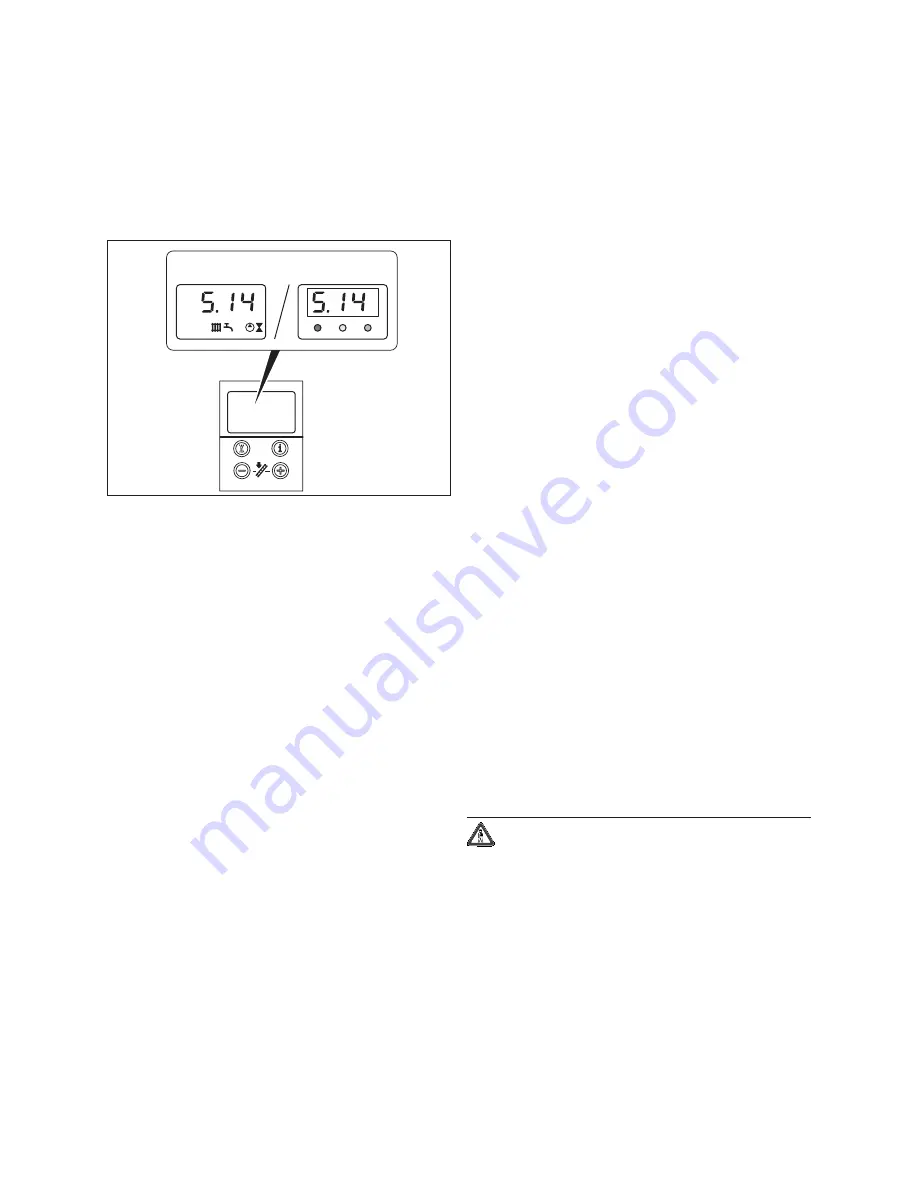
38
Installation and maintenance manual ecoTEC
6.1.3 Water heating (only 800 series)
• Switch on the appliance.
• Turn on a hot water plug fully.
• Press “
i
” to activate the status indicator.
If the water heating is working correctly, the display
shows the following: “
S.14
”.
plus
pro
Fig. 6.3 Display indicator during water heating
6.1.4 Final rinsing of the heating system (“hot”)
• Operate the appliance until the appliance and the
heating system are heated up.
• Check the heating system for leaks.
• Connect a hose to the drain valve located at the low-
est position of the heating system.
• Shut off the appliance, open the drain valve and all
vent valves on the heating elements and allow the
water to flow out of the heating system and the heater
quickly and fully.
• Close the drain valve.
• Fill the heating system again with water as described
in Section 5.4.4.
• Release water from the system until the system design
pressure of 1.0 bar is attained. (The actual reading on
the digital pressure gauge should ideally be 0.5 bar
plus an additional pressure corresponding to the high-
est point of the system above the base of the boiler –
10 m head equals an additional 1 bar reading on the
pressure gauge. The minimum pressure should not be
less than 1 bar in any installation.) If the system is to
be treated with an inhibitor it should be applied at this
stage in accordance with the manufacturer’s instruc-
tions. Further information can be obtained from
Sentinel, Betz Dearborn Ltd., Tel: 0151 4951861, or
Fernox, Alpha–Fry technologies. Tel: 0870 6015000.
• Refit the boiler casing (see Section 5.10).
• Only in ecoTEC plus appliances: Attach the bottom
cover to the boiler by sliding the front edge of the
cover into the lip at the bottom front edge of the
appliance chassis.
• Carefully push the rear of the bottom cover upwards
until the spring retaining clips engage at the side of
the appliance. It may be necessary to adapt the bot-
tom cover by removing the easy break sections.
6.2
Handing over to the user
• Set the maximum radiator temperature control to the
desired setting.
• Set the maximum hot water temperature control to
the desired setting.
• Instruct the user in the safe and efficient operation of
the boiler, in particular the function of
– the boiler on/off control
– the maximum radiator temperature control
– the maximum hot water temperature control (only
800 series)
– the pressure gauge
• Show the user how to operate any external controls.
• Explain to the user the importance of having the boiler
regularly serviced by a competent servicing company.
To ensure regular servicing, it is strongly recommend-
ed that arrangements are made for a Maintenance
Agreement. Please contact Vaillant Service Solutions
(0870 6060 777) for further details.
• Record central heating operating pressure in the
Benchmark Log Book along with the heat input (kW)
and temperature difference between flow and return.
Failure to install and commission this appliance in
compliance with the manufacturers instructions may
invalidate the warranty (Note: This does not affect
your statutory rights).
• Leave the user instructions, installation instructions
and log book with the user.
7
Inspection and maintenance
7.1 Initial
inspection
To ensure the continued safe and efficient operation of
the boiler it is recommended that it is checked and serv-
iced as necessary at regular intervals. The frequency of
servicing will depend upon the particular installation
conditions and usage, but in general once per year
should be adequate.
Danger!
It is law that all servicing work is carried out by
a competent person (CORGI registered).
Inspections/Maintenance work not carried out
can result in damage to property and personal
injury.
Only genuine Vaillant spare parts may be used for
inspections, maintenance and repair work to ensure the
perfect long-term working order of all functions of your
Vaillant appliance and to prevent the permitted series
condition from being changed.
Any spare parts which might be required are contained
in the current spare parts catalogues.
Information can be obtained from Vaillant Customer
Service Centres.
6 Commissioning Part II
7 Inspection and maintenance
Содержание ecoTEC plus SERIES
Страница 55: ...55 Installation and maintenance manual ecoTEC...
Страница 56: ...839592_00 GB 09 2004...