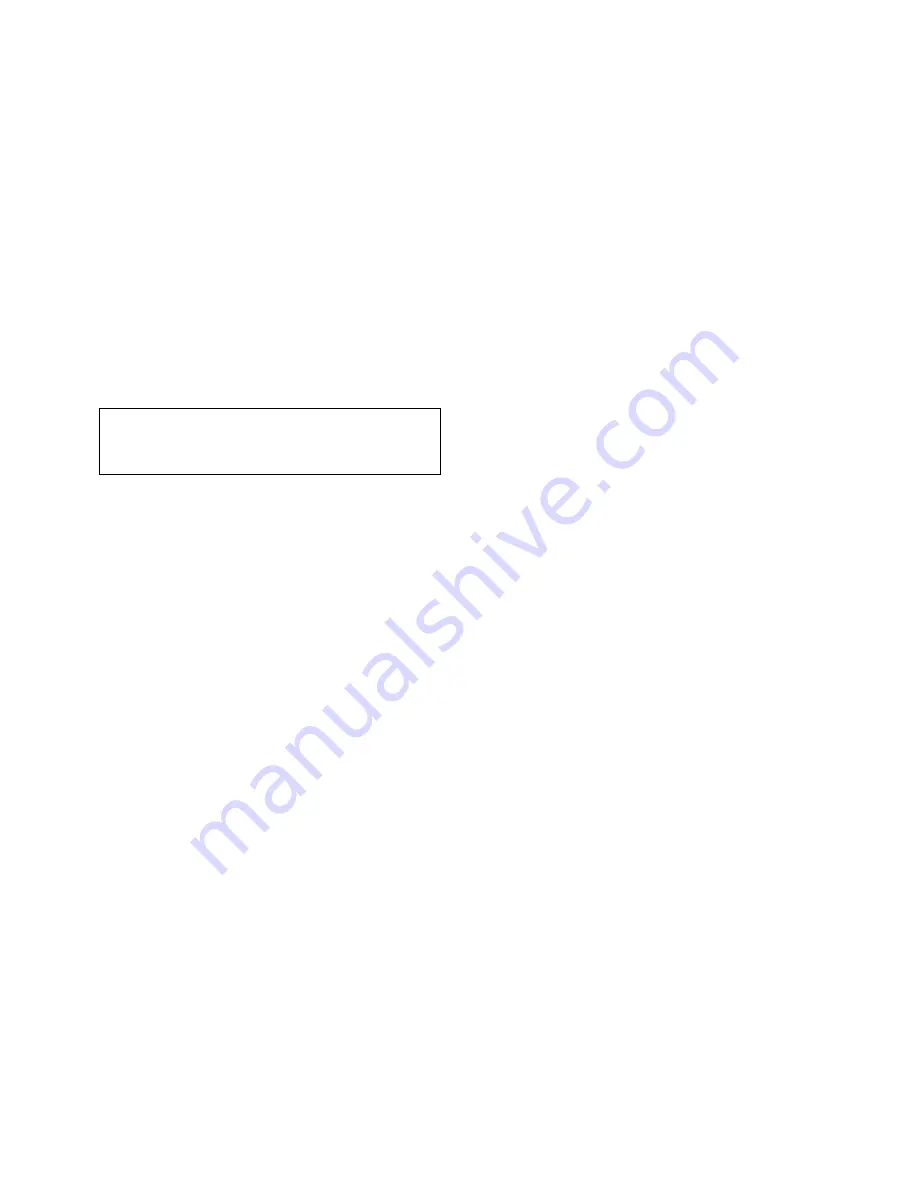
1
INSTALLATION, OPERATION and
MAINTENANCE
42
”-60” Figure 250-DOC
Oil-Cushioned Lever & Weight Swing Check
INTRODUCTION
This manual will provide the information to properly
install, operate and maintain the valve to ensure a
long service life. The Figure 250-DOC Swing Check
Valve is ruggedly constructed to provide years of
trouble-free operation with minimal maintenance.
CAUTION
The valve is NOT recommended for use with toxic or
highly corrosive fluids, fuels or fluids containing
hazardous gases
The Shop Order (SO) Number, Figure Number, size
and pressure rating are stamped on a nameplate
attached to the valve. Please refer to the SO number
when ordering parts.
DESCRIPTION OF OPERATION
The Figure 250-DOC Swing Check Valve is an oil-
cushioned, counter-weighted rubber-to-metal seated
check valve designed to permit flow in one direction
and close to prevent reverse flow. The valve opens
when the inlet pressure exceeds the outlet pressure.
The degree of opening depends on the fluid velocity
through the valve. The valve will swing closed as fluid
velocity decreases and be fully seated before flow
reversal precluding slam and bang.
RECEIVING AND STORAGE
Inspect the valve upon receipt for damage during
shipment. Carefully unload all valves to the ground
without dropping.
The valves should remain in a clean, dry and weather
protected area until installed. For long term storage
(greater than 6 months) the rubber surfaces of the
seat should be coated with a non-toxic lubricant such
as "SuperLube" made by Synco Chemical. Do not
expose the rubber parts to sunlight or ozone.
INSTALLATION
Figure Numbers suffixed with “D” indicated the valve
has ANSI Class 125 flanged connections.
An “A” in
the Figure Number (e.g., 250-DAOC) indicates the
valve is configured for installation in a vertical pipe
with upward flow.
Consult the drawings of record to verify the
configuration supplied and installed.
Prior to installation ensure all debris, packing material
or other foreign material has been removed from both
ports.
The valve can be installed in a horizontal or vertical
(upward flow direction) pipe. In either case the
counterweight arm must be horizontal when the valve
is closed. Ensure all external fasteners and set
screws are tight.
Note the
“INLET” tag and/or flow arrow and install the
valve in the proper flow direction. Forward flow
should tend to open the valve.
If installed outdoors, below ground in a vault or in an
unheated area, adequate freeze protection must be
provided.
Adequate isolating valves should be installed between
the valve and the pipeline or system to facilitate
maintenance.
The valve is supplied with (4) legs to facilitate
mounting on a pier to support its weight and to
minimize valve movement caused by pipeline
vibration. The valve flanges are not designed to
support adjacent equipment, piping loads should not
be imposed on the valve and large valves should be
properly supported. Ensure mating flanges are
square and parallel to the valve flanges before
tightening flange bolts.
Flat-faced flanged valves should be mated with flat-
faced flanges and full-face gaskets. If ring gaskets
are used the bolt material shall be ASTM A307 Grade
B (or equivalent). Higher strength bolting should only
be used with full-face gaskets.
Lower heavy valves using slings or chains around the
valve body and/or the lifting eye. Lubricate the bolts
or studs and insert around flange. Lightly tighten
bolts until gaps are eliminated. Torque bolts in an
alternating pattern in graduated steps. If leakage
occurs wait 24 hours and re-torque the bolts but do
not compress the gasket more than 50% or exceed
bolt maximum torque rating.