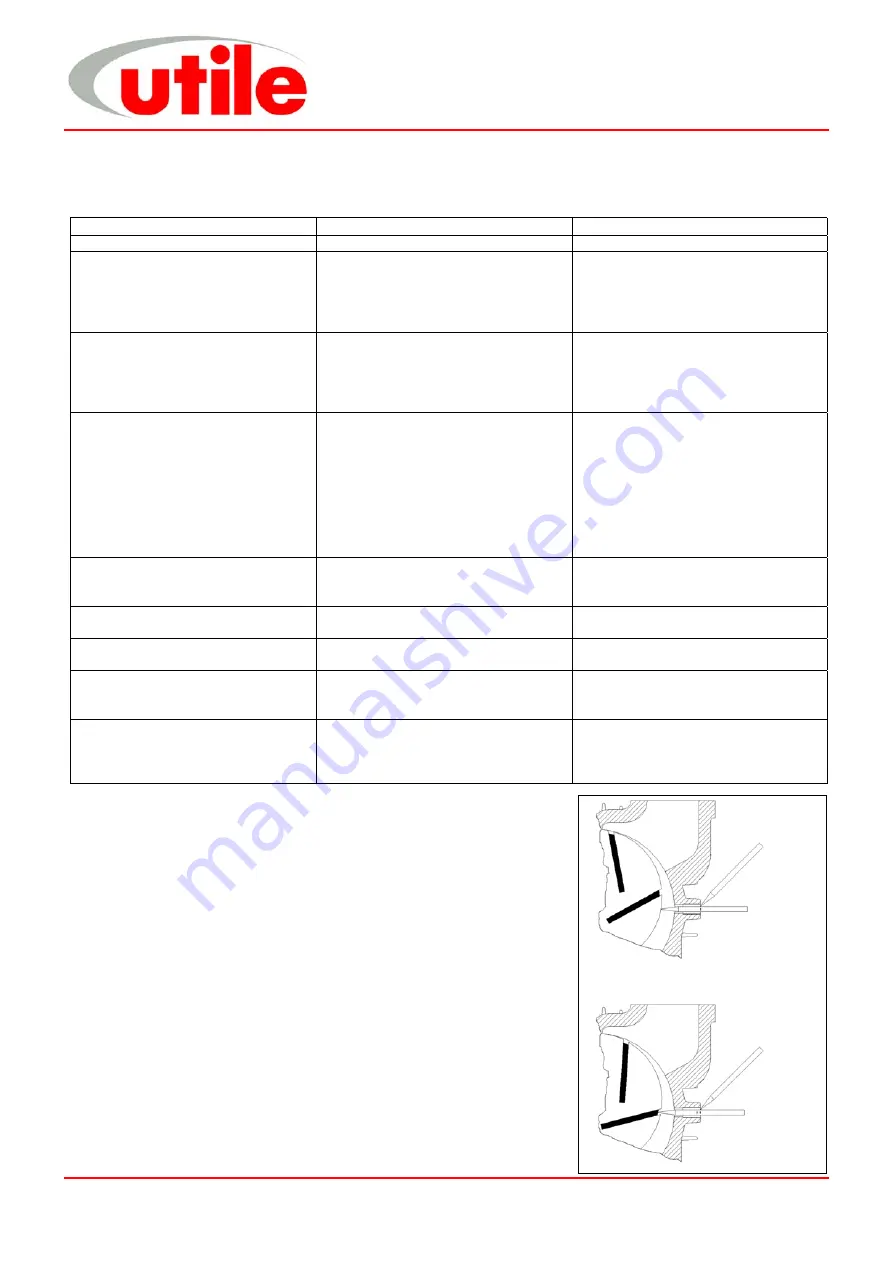
The Utile Engineering Co. Ltd.
27/11/03
Irthlingborough, Northamptonshire. England
Tel: +44 (0) 1933 650216
Fax: +44 (0) 1933 652738
11
IC162
Troubleshooting
The following table shows some typical problems and the remedies.
Note: If assistance is required in determining and correcting the fault with the machine then contact our service
department.
1.
Check Blade Wear
When carrying out any maintenance and inspections always follow the
health and safety guidelines on page 4. Fully trained and competent staff
must carry out any maintenance work.
1.1
Carry out the following procedure after the first 2,000 running
hours and repeat every 5,000-hour interval. Record all
measurements.
1.2
With the pump stationary and with the system drained, remove the
plug on the side of the machine cylinder and insert into the hole
beneath a pointed measuring rod 6mm dia x 150mm long until
contact is made with the rotor (see fig. 8). Scribe a mark on the
rod. Slowly rotate the shaft by hand until the rod drops onto the tip
of the blade, scribe a second mark on the rod. Measure the
amount of movement and renew the blades if this exceeds 6mm.
Replace the plug or eyebolt.
SYMPTONS
CAUSES
REMEDIES
Machine revolves in wrong direction
Incorrect connection of motor terminal
Re-arrange terminal connection
1. Machine operating at higher duty than
specified.
1. Check rating.
2. Blocked intake filter.
2. Clean intake filter.
3. Insufficient or wrong lubrication.
3. Use correct lubrication and feed rates.
Discharge air temperature excessive
4. Warped / Sticking blades
4. Replace blades
1. Insufficient lubricant to cylinder.
1. Inspect & clean oil lines, oil holes.
2. Incorrect lubricant.
2. Use correct lubricant.
3. Dirty inlet air/gas.
3. Clean & inspect intake.
Excessive blade wear
4. Excessive operating temperature
4. See remedies for excessive discharge
temperature.
1. Worn bearing.
1. Replace bearing.
2. Excessive blade wear.
2. Replace blades & check lubrication
3. Erratic cylinder wear.
3. Rebore, redowel & check lubrication.
4. Insufficient lubrication
4. Increase lubrication rate
5. Rotor contacting coverplates
5. Check temperature, pressure &
internal clearances
6. Drive misalignment
6. Realign and retension drive.
7. Warped rotor blades.
7. Replace rotor blades.
Abnormal noise, vibration or periodic
knocking
8. Excessive liquid carryover.
8. Drain all points.
1. Worn blades.
1. Replace rotor blades.
2. Improper belt tension.
2. Adjust belt tension.
Pressure cannot be built up or only up
to a certain extent.
3. Sticking relief valve.
3. Clean and replace.
1. Improper belt tension.
1. Adjust belt tension.
Slipping of belts
2. Worn belt.
2. Replace with new ones.
Overheating of electric motor
1.Overloading of motor due to excessive
working pressure.
1. Lower working pressure.
1. Breakdown of electric current
1. Contact power company.
2. Malfunction of motor.
2. Check motor.
Machine does not start
3. Wrong motor connections.
3. Check electrical connections.
1. Faulty bearing
1. Replace bearing.
2. Foreign particles in machine.
2. Disassemble machine and remove
foreign particles.
Shaft partially or totally locked
3. Machine seized.
3. Repair machine.
Troubleshooting
Check Blade Wear
Fig. 8
Scribe mark with rod
resting on rotor, turn
rotor and scribe mark
with rod on blade