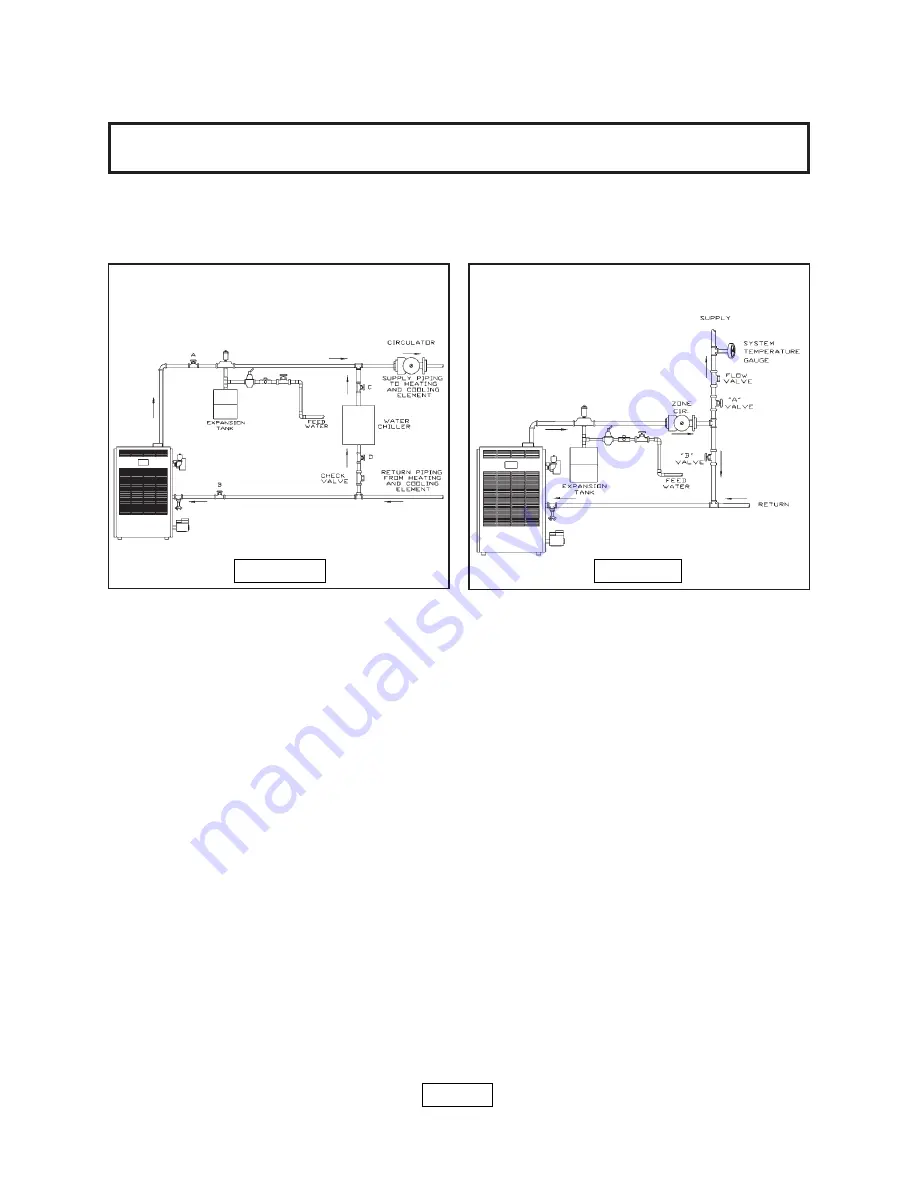
PAGE 3
FIGURE 2
FIGURE 3
BYPASS PIPING
CONNECTING SUPPL
CONNECTING SUPPL
CONNECTING SUPPL
CONNECTING SUPPL
CONNECTING SUPPLY
Y
Y
Y
Y AND RETURN PIPING
AND RETURN PIPING
AND RETURN PIPING
AND RETURN PIPING
AND RETURN PIPING
IMPORTANT:
Circulators in the following illustrations are mounted on the system supply
side, but mounting on the system return side is also acceptable practice.
B. Use appropriate valves to prevent the chilled medium from entering the heating boiler.
1. During heating cycle open valves A and B. Close valves C and D.
2. During cooling cycle open valves C and D, close valves A and B.
C. Maintain a minimum clearance of 1 inch (2.54 cm) to hot water pipes. In air handling units
where they may be exposed to refrigerated air circulation, the boiler piping system
MUST be supplied with flow control valves or other automatic means to prevent gravity
circulation of the boiler water during the cooling cycle.
2. Hot water boilers installed above radiation level must be provided with a low water cut-off
device at the time of boiler installation.
3. When a boiler is connected to a heating system that utilizes multiple zoned circulators, each
circulator must be supplied with a flow control valve to prevent gravity circulation.
* Reduced pressure back flow preventer must be used under provisions required by the
Environmental Protection Agency, (EPA).
4. Bypass piping is an option which gives the ability to adjust the supply boiler water
temperature to fit the system or condition of the installation. This method of piping is not
typically required for baseboard heating systems.
A. This method is used to protect boilers from condensate forming due to low temperature
return water. Generally noticed in large converted gravity systems or other large water
volume systems. See figure 3 above.
B. These methods are used to protect systems using radiant panels and the material
they are encased in from high temperature supply water from the boiler and protect
the boiler from condensation. See figures 4 & 5 below.
5. Note: When using bypass piping, adjust valves A and B, in figures 3 and 5, until desired
system temperature is obtained.
1. Connect supply and return piping as suggested in figure 2 below when the boiler is used in
connection with refrigerated systems:
A. The chilled medium MUST BE IN PARALLEL with the boiler.