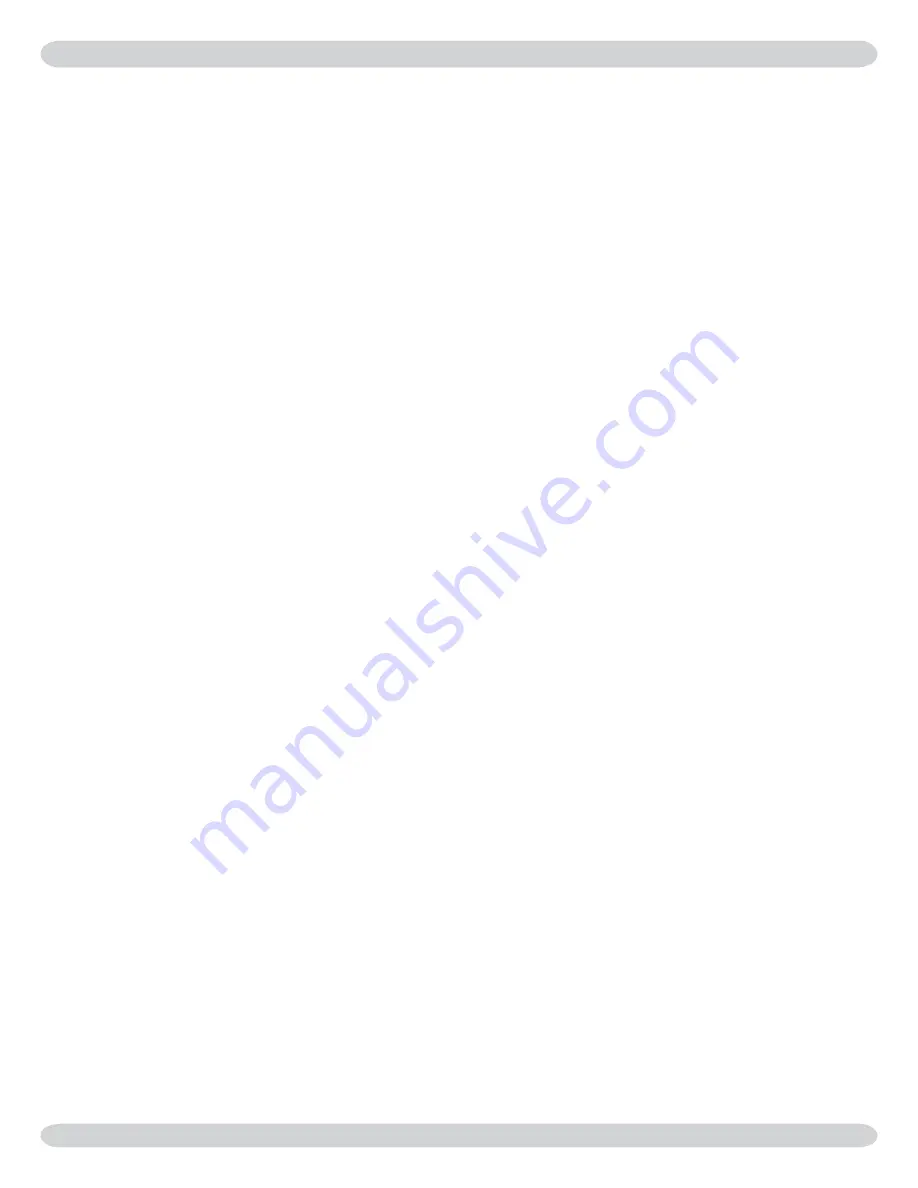
44
F. Test High Limit Control And Adjust
While burner is operating, move indicator on high limit
control below actual boiler water temperature. Burner should
go off while circulator continues to operate. Raise limit setting
above boiler water temperature and burner should reignite
after pre purge and igniter warm-up period. Set the high limit
control to the design temperature requirements of the system.
Maximum high limit setting is 200°F. Minimum high limit set-
ting is 100°F.
G. Test Other Safety Controls
If the boiler is equipped with a low water cut off, a manual
reset high limit, or additional safety controls, test for opera-
tion as outlined by the control manufacturer. Burner should
be operating and should go off when controls are tested. When
safety controls are restored, burner should reignite.
H. Set Thermostat Heat Anticipator (If Used) And Verify
Thermostat Operation
For a single thermostat connected to the yellow thermostat
lead wires in the furnished field wiring junction box, the heat
anticipator should be set at 0.7 amps. For other wiring configu-
rations, refer to the instructions provided by the thermostat
manufacturer regarding adjustment of heat anticipator. Cycle
boiler with thermostat. Raise the thermostat to the highest
setting and verify boiler goes through normal start up cycle.
Lower thermostat to lowest setting and verify boiler goes off.
I. Measure The Natural Gas Input Rate
Correct input rate is essential for proper and efficient operation
of the burner and boiler.
Determine elevation at installation site.
1.
See page 6 and 7 of this manual to determine the correct
2.
input rate for the local elevation.
Obtain the yearly average heating value of the local gas
3.
supply from the gas utility. At sea level elevation, it should
be approximately 1000 Btu’s per standard cubic foot.
Operate boiler for 5 minutes.
4.
Turn off all other gas appliances, extinguishing standing
5.
pilots where applicable.
At gas meter, measure time in seconds required to use one
6.
cubic foot of gas.
Calculate input rate according to the following formula:
7.
3600xheating value from step 3
Btuh inputrate = time from step 6
Measured input rate should be /-2% of the input
8.
rating from step 2. If within 2%, go to step 9. If not, adjust-
ment is required, proceed as follows:
Turn boiler off
A.
Set up U-tube manometer or differential pressure gauge
B.
for measuring manifold pressure, see
Figure #17
.
Manometer or gauge must be able to read at least 0.0 to
C.
3.0 inches water column of pressure, and resolve to at
least 0.1 inches water column.
Turn boiler on.
D.
Manifold pressure has been nominally set at 2.5 inches
E.
w.c. Manifold pressure and input rate must always be
measured with pressure regulator cover screw installed.
Cover screw must be removed for adjustment. Manifold
pressure reading will change (increase) when cover screw
is removed.
After adjusting input rate, turn boiler off, remove ma-
F.
nometer or pressure gauge, reinstall ⅛” plug on gas
valve. Turn boiler on.
Restore all gas appliances that may have been shut off
9.
(while measuring boiler input rate) to normal operating
conditions.
Remove regulator cover screw on top of gas valve, and
I.
insert an appropriate screwdriver into adjustment screw.
Turn adjustment screw clockwise to increase input rate,
II.
or counter clockwise to decrease input rate.
Replace cover screw, or cover hole temporarily with
III.
your finger to check new manifold pressure setting. Do
not set manifold pressure lower than 2.0 inches w.c. or
higher than 3.0 inches w.c. when adjusting input rate.
CHECK OUT PROCEDURE AND ADJUSTMENT
Содержание UB100
Страница 15: ...15 Near Boiler Piping Figure 2 Single Zone Boiler Piping ...
Страница 16: ...16 Figure 3 Multi zone Boiler Piping With Zone Valves Near Boiler Piping ...
Страница 19: ...19 Figure 6 Diaphragm Type Expansion Tank Piping Near Boiler Piping ...
Страница 20: ...20 Figure 7 Conventional closed type Expansion Tank Piping Near Boiler Piping ...
Страница 27: ...27 Combustion Air and Vent Pipe Figure 11 Combustion Air and Vent Piping ...
Страница 32: ...32 Electrical Wiring Figure 13 Field Wiring Connections ...
Страница 53: ...53 DETAILED SEQUENCE OF OPERATION ...
Страница 57: ...57 TROUBLESHOOTING CHART 2 TROUBLESHOOTING ...
Страница 58: ...58 TROUBLESHOOTING CHART 3 TROUBLESHOOTING ...
Страница 60: ...60 TROUBLESHOOTING CHART 5 TROUBLESHOOTING ...
Страница 63: ...REPAIR PARTS Model No UB90 50 UB90 75 UB90 100 UB90 50 100 GAS FIRED DIRECT VENT CONDENSING HOT WATER Boiler ...
Страница 64: ...64 20 3 5 TYP OF 4 6 11 8 9 10 13 15 16 2 12 1 21 17 18 18 4 19 7 A Jacket and Base Assembly Repair Parts ...
Страница 72: ...P O Box 4729 Utica NY 13504 4729 ...