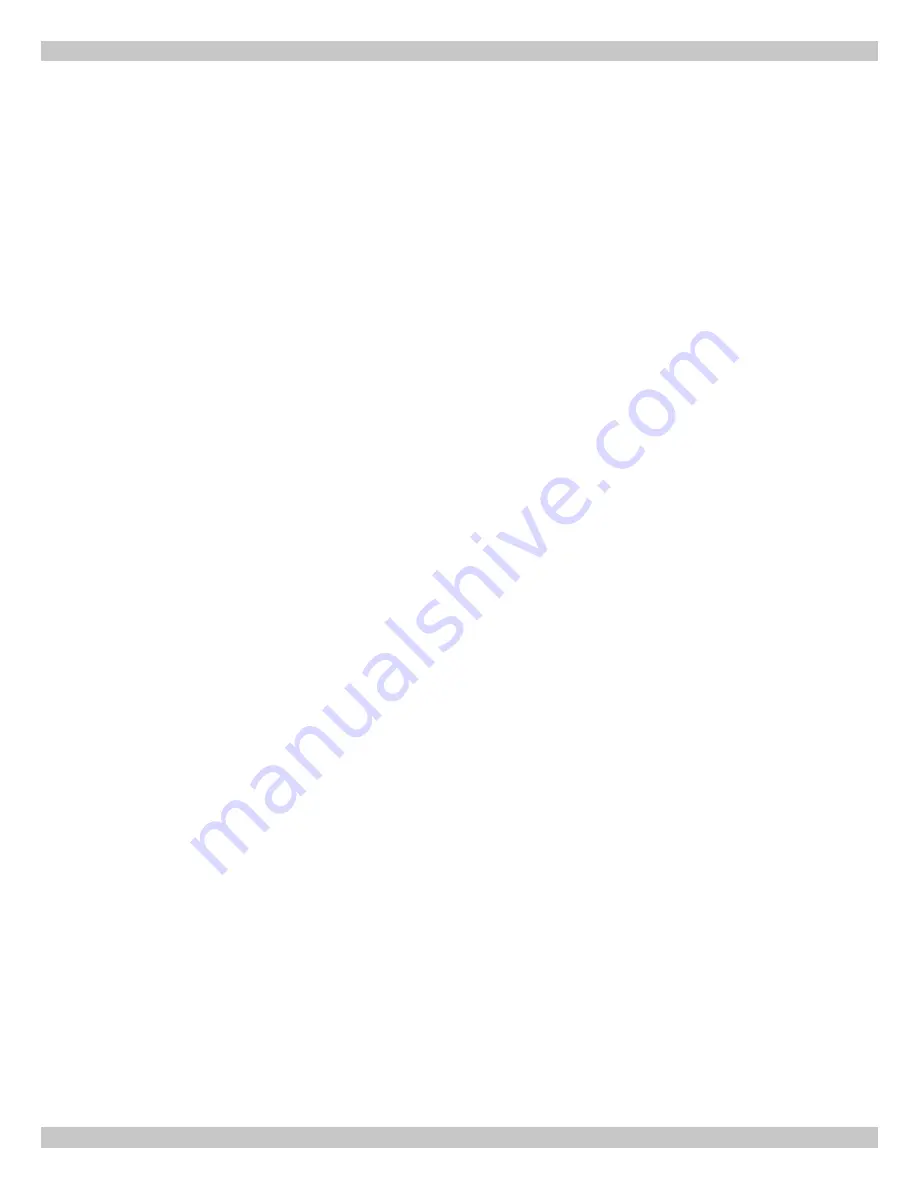
29
P/N
240011589
, Rev. A [08/03/2016]
Burners
Beginning of heating season visually check pilot end main
burner flames. See
Figures 13, and 15.
Safety Relief Valve
Test safety relief valve for proper operation. Refer to valve
manufacturer’s instructions packaged with relief valve.
Expansion Tank (Non-diaphragm)
Tank may become waterlogged, or may receive excess
of air. Frequent automatic opening of safety relief
valve indicates water logging. High boiler temperature
accompanied by unusually low radiation unit temperature
(and “knocking”) indicates excess air in tank.
To correct:
1.
Close valve between boiler and tank. Drain tank until
empty.
2.
Check all tank plugs and fittings. Tighten as necessary.
3.
Open valve between boiler and tank. Water will rise to
normal height in tank if you have automatic fill valve
(otherwise, manually refill system).
Boiler Flue Passages
Recommend following checked annually by qualified service
agent.
x
flue passages
x
burner adjustment
x
operation of controls
Before start of each season (or whenever system has been
shut down for some time) recheck whole system for leaks
and recheck boiler and vent pipe for leaks. Replace or patch
any boiler seals that are faulty. Before start of each season
(or whenever system has been shut down for some time)
recheck the whole system for leaks . . . and recheck the
boiler and vent pipe for leaks. Replace or patch any boiler
seals that are faulty.
Vent Pipe
Venting and piping should be checked at least monthly. If
vent piping shows any sign of leaking, replace immediately.
Water System
If system is to remain out of service during freezing
weather, always
drain it
completely (water left in to freeze
will crack pipes and/or boiler).
Cleaning Your Boiler And Burners
Flue passages between sections should be examined yearly
and cleaned if necessary.
To clean:
x
Remove burners, pilot, and vent pipe.
x
Remove top and front jacket panels.
x
Remove two screws attaching intermediate front panel
to left and right side jacket panels.
x
Remove control panel as a unit.
x
Remove draft diverter and intermediate front panel.
x
Carefully remove cerafelt gasket strips.
x
Clean passageways between sections with flexible
handle wire brush. Remove dirt from bottom of boiler
and from between sections by vacuuming.
x
Verify all flame ports in burners are open and clear.
Shake out or blow out all loose dirt in burners.
x
Reseal seams between adjacent sections as necessary
with 400
°
F RTV silicone sealant.
x
Reassemble all parts.
x
Verify tightness of pilot connections and condition of
burner flames after reassembly. See Figures 13 and 14.
x
Verify vent pipe connections to chimney are secure and
no obstructions are present.
Blower
Blower motor features permanently lubricated ball bearing
construction. Lubrication is not required.
Circulator Pump Isolation Valves
Operate isolation valves in circulator pump flanges
manually once or twice per year to prevent valves from
becoming stuck in open position
Rotate valves from open position to closed position and
back to open position.
Low Water Cut-off(s)
Inspect field sourced low water cut-offs annually or
as recommended by low water cut-off manufacturer.
Flush float type low water cut-off(s) per manufacturer’s
instructions.
Housekeeping
x
Keep boiler area clear and free from combustible
materials, gasoline and other flammable vapors and
liquids.
x
Keep boiler area clear of debris and other materials
obstructing flow of combustion and ventilation air.
MAINTAINING YOUR BOILER