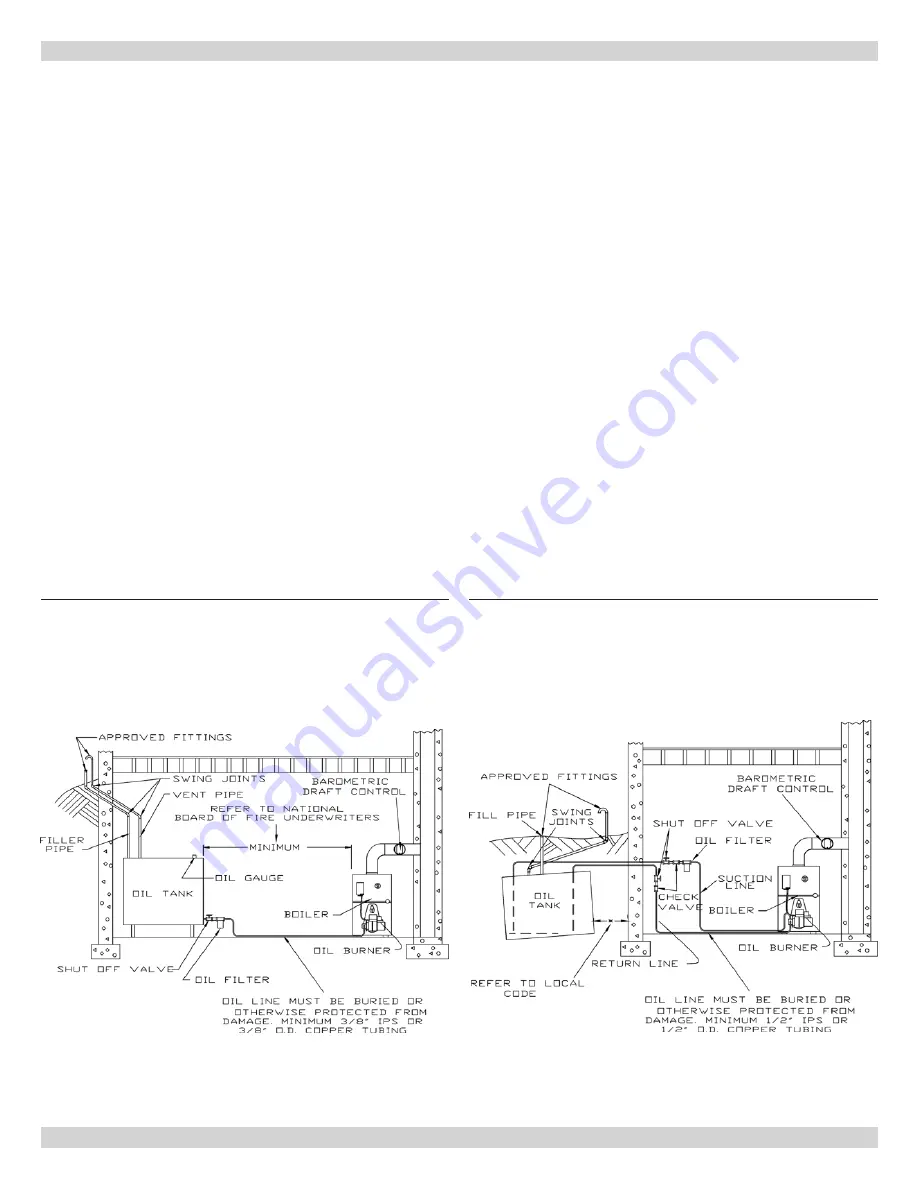
14
Oil Tank and Piping Installation
• Install oil tank and piping in accordance with the National
Board of Fire Underwriters and local regulations.
•
Oil storage tank, vent, fill pipe and caps should be as
prescribed by local codes. In no case should the vent pipe
be smaller than 1¼" I.P.S. The fill pipe should not be less
than 2" I.P.S.
• Suction line from tank to burner shall be one continuous
piece of tubing to prevent air entering the line.
A.
Suction line, must be ⅜" O.D. copper tubing for runs
of 50 feet or less, and ½" O.D. for longer runs.
B. Install oil return line same size suction line. Use on
any installation where bottom of tank is below fuel
unit of burner.
C. Oil lines should be buried or otherwise protected from
mechanical injury.
D.
Flare fittings on all oil lines are recommended.
E.
Compression fittings on suction line often allows air
to be drawn into fuel pump, making it difficult to
maintain oil pressure at the nozzle.
F. Do not run overhead fuel lines from tank to oil
burner.
• Install fuel pump connections and by-pass according to
instructions attached to the fuel pump. If tank is more
than 20' from boiler, install two stage fuel unit in place
of single stage pump supplied as standard equipment
with burner. Verify rotation and speed are same and
pump is suitable for burner horsepower rating.
•
Install oil line filter and shut-off valve in suction line.
Install shut-off valves in both suction and return lines
at burner for servicing burner. Allow extra tubing at
burner so burner may be removed from boiler for
cleaning without disconnecting tubing. See Figure 16
and
Figure 17
.
Optional flexible oil line is available.
OIL TANK AND PIPING
Figure 16
Typical Installation Single Pipe Oil
System
Figure 17
Typical Installation Two Pipe Oil
System
Содержание BC3095
Страница 16: ...16 WIRING DIAGRAMS Figure 18 Wiring Diagram...