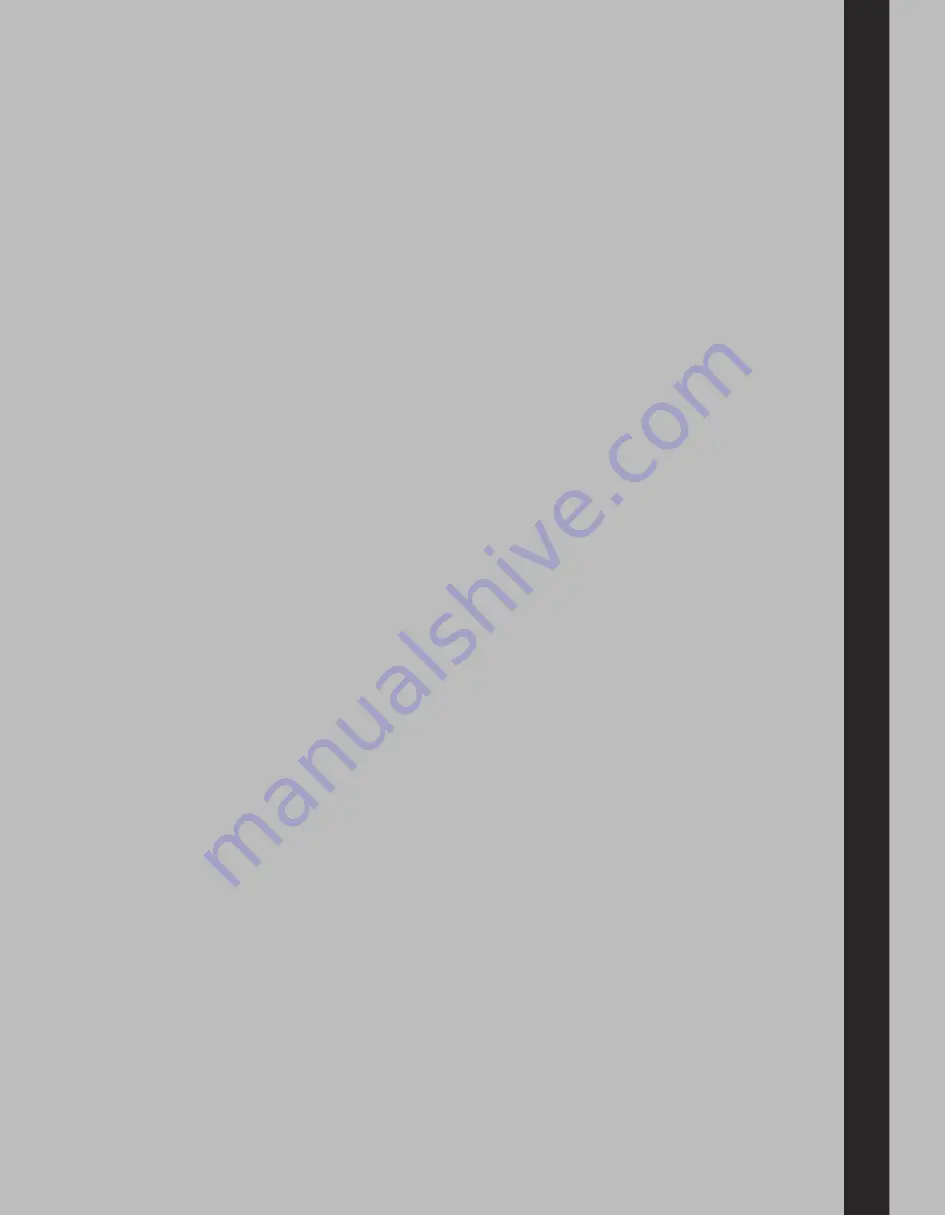
Maintenance
Frequent and routine maintenance procedures should be followed
to ensure the safe and efficient operation of the mower. The follow-
ing procedures should be performed every 8 working hours. Under
severe conditions this schedule should be accelerated.
• Check free end bearing and bearing housing for excessive heat: indicating loss
of lubrication or possible bearing damage.
• Check blades, blade bolts, nuts and towers for excessive wear, chipping or
cracking.
• Grease bearings: free end ~4 pumps every 4 hours — drive end until grease
comes out the breather
• Check hydraulic lines for damage and leaks.
• Clean debris, leaves, grass and sticks from inside shroud and or rollers.
• Check bolts and nuts on all mountings and optional equipment.
• Check depending on your options: gates, shields, shroud and rollers etc. Re-
pair if damaged or replace if necessary.
Lubrication
The drive end bearing housing has a grease zerk and a grease vent plumbed to the
surface of the mower enclosure. The amount needed varies with ambient tem-
perature and mowing load. Generally greasing twice a day is sufficient for heavy
operation. A good quality NLGI#2 lithium grease is usually satisfactory. If the
bearing housing is pumped full of grease when cold, at first run up after a cold
fill, a substantial quantity of grease will issue from the vent as the grease heats.
This is normal. To reduce this, grease when equipment is at operating temperature.
Inspect before mowing
Inspect cutter drum and knives. Inspect the blades for wear, damage & cracks. In-
spect towers for cracks. Inspect blade bolts for wear and tightness. Replace or
repair any problem items immediately. Injury can be caused if a blade or tower is
thrown from cutter shaft while mowing.
Replacing blades and blade bolts
Your mower will be more efficient if running with sharp blades. Blades may be
turned around if one side is worn. Blades should be replaced in sets to maintain
cutter shaft balance. Blade bolts, washers and bolt nuts should be examined and
replaced if worn. Bear in mind that parts subject to intense pounding will in time
develop fatigue cracks.
Install the blade assembly as shown in the shaft diagram. Note that if top lock
nuts are used they should be threaded onto the bolt such that the nut runs out
of bolt threads. It is the resulting thread jamming effect on the nut that holds
it in place against shock and vibration. This type of nut must be driven to refusal
with a 3/4” High power impact gun.