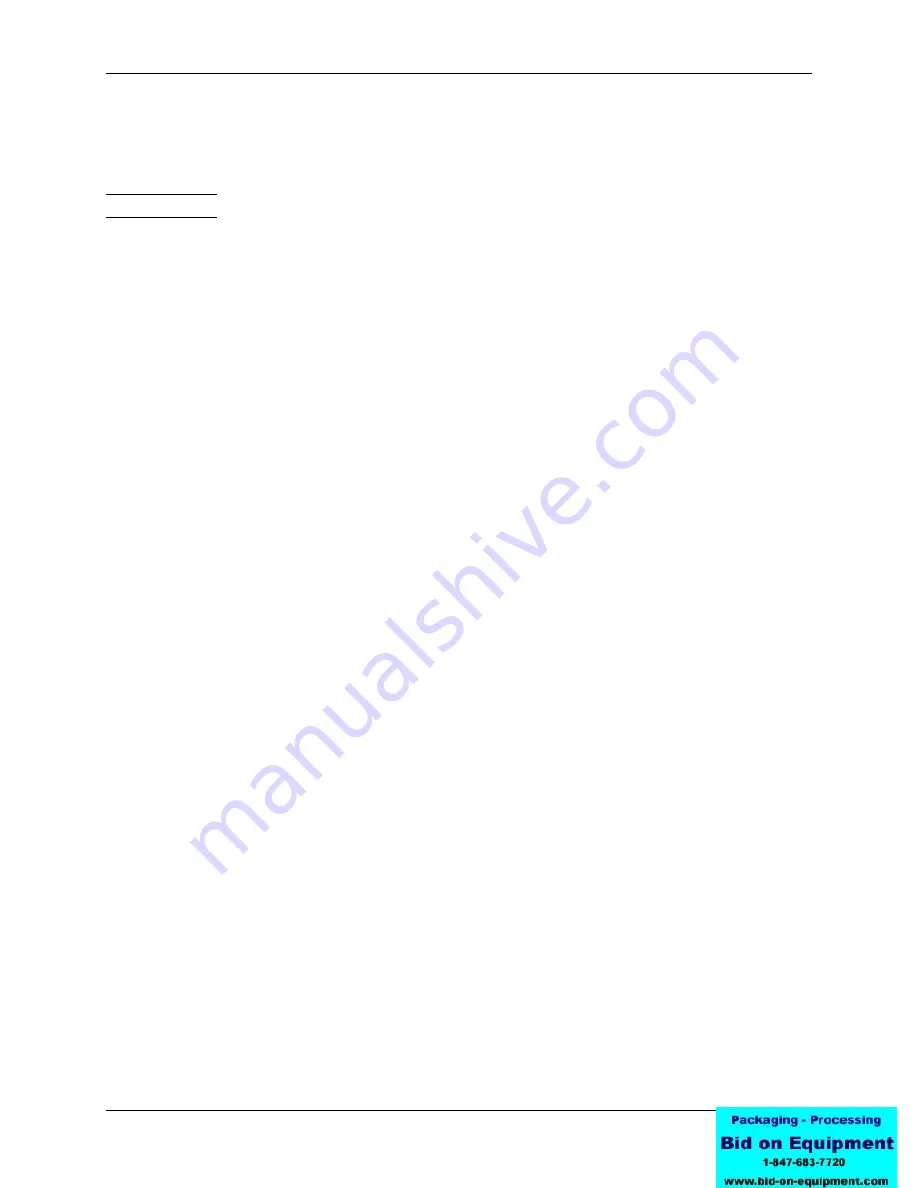
MANOWNROLH
SYSTEM MAINTENANCE
U.S. FILTER
4-5
system. Localized areas of high sanitant concentration could degrade the
RO membranes. Also, the length of time that the RO pump is turned on
will be different with each model of RO system and the means used to
introduce the sanitant.
CAUTION
Do not use the static soak method of sanitization with any chemical other
than formaldehyde.
E.
Cleaning the System
When the RO systems are properly operated, they do not require frequent
cleaning. In time, however, the RO membrane cartridges can become fouled to
a point where system performance is adversely affected, resulting in diminished
product output or salt rejection. When the product flow rate drops by 10% and/or
the salt content in the product water rises noticeable, this may indicate fouling of
the cartridge membrane. However, other factors such as temperature
decreases, or malfunctioning pretreatment systems, pressure controls and
pumps may also cause these conditions. It is important to rule out these factors
before cleaning the system.
Clean the cartridges if the system performance (based on flow rate or salt
rejection) decreases because of membrane fouling. An increase in the feed to
reject differential pressure also indicates that cleaning is needed. Membrane
foulants include colloidal materials such as aluminum and silica compounds,
precipitated metal hydroxides of iron and manganese, biological films, and
calcium or magnesium carbonate scale.
The type of cleaning solutions (See Table 4-2), and the sequence in which they
are used, depends on the type of foulant present (organic compounds, metal
hydroxides, Ca/Mg carbonates, etc.). The need for frequent cleaning (twice a
week or more), may indicate that pretreatment is inadequate. This section
includes general guidelines for developing a cleaning procedure for your
particular application.
F.
Effects of Foulants on RO System Performance
1.
Colloidal fouling
Causes product flow rate to decrease, and salt passage to increase,
usually in that order. RO systems that operate on high SDI feed water
are prone to colloidal fouling.
2.
Metal hydroxide (iron, manganese)
Causes a significant and rapid decrease in the product flow rate, and an
increase in salt passage.
3.
Biological fouling
Causes a biofilm to form on the membrane surface. This biofilm inhibits
the membrane’s ability to reject salt, and therefore salt passage
increases. The product flow rate may also decrease, but not necessarily
at a rapid rate.
4.
Scaling
Causes a decrease in the product flow rate and an increase in salt
passage.