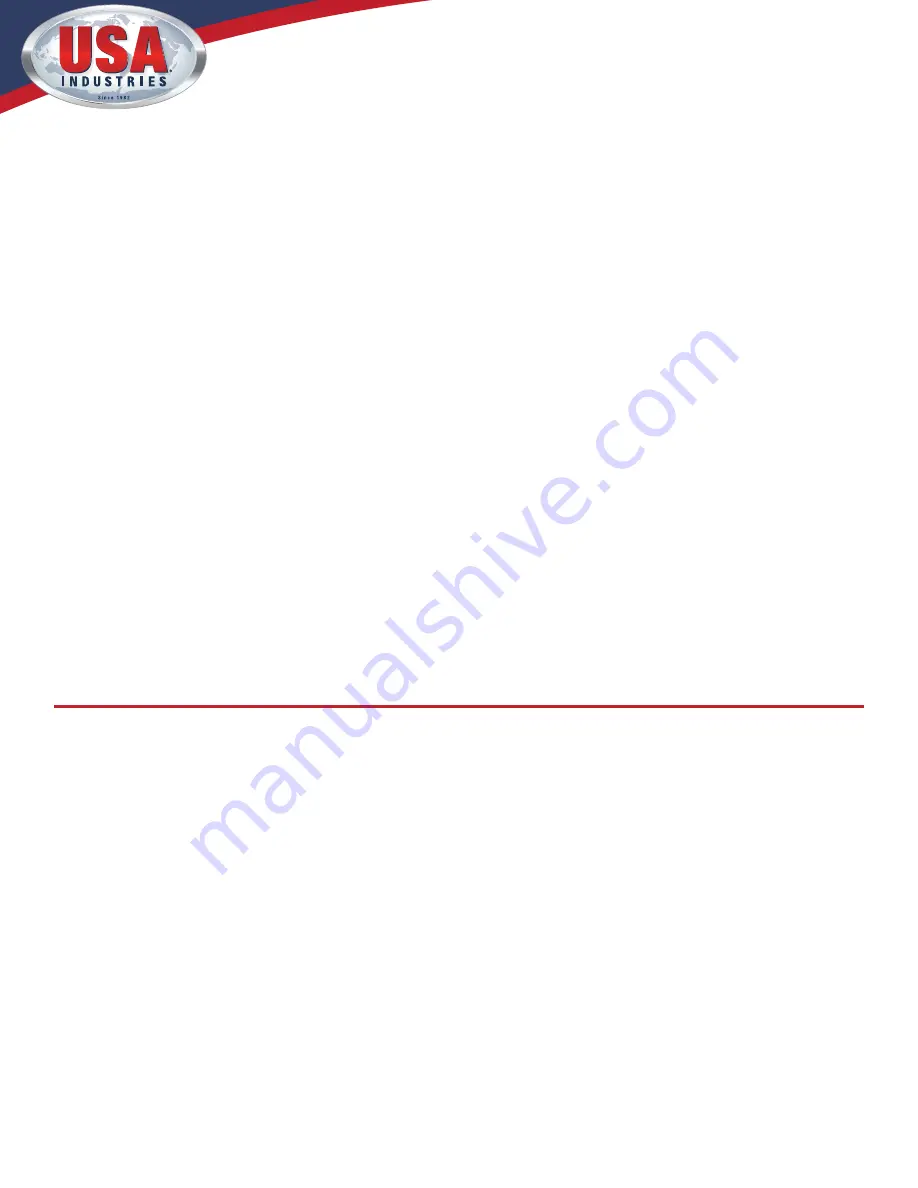
TLD-2500 OPERATING INSTRUCTION MANUAL
www.USAIndustries.com | (713) 941-3797
©2022, USA Industries
M-OM-TLD2500-1.1
TLD-2500 TUBE TESTING GUNS
OPERATING INSTRUCTIONS
5. Insert the Air Injection Gun into one tube end and the Plugging Gun on the opposite end of
the tube being tested. Apply enough pressure to seat the plastic washer (Fig. 1 & Fig. 2 Item 4)
firmly against the end of the tube. Maintain this pressure throughout the remainder of the test.
6. After ensuring the Plugging Gun operator is ready, actuate the air control valve on the Injection
Gun and hold until the pressure gauge reading is steady.
7. Release the button on the air control valve. It will automatically return to the closed position
isolating the tube being tested. The tube is now under pressure.
8. Both Injection Gun and Plugging Gun operators should monitor their respective pressure
gauges. Any decreasing pressure observed on the gauges will be indicative of a tube leak. Press
the bleed valve on the Injection Gun to reduce the air pressure in the tube and reset the air
cylinder seals. If a leak has been indicated, repeat step 11 to insure leak was not caused by a
faulty seal to the tube.
9. Remove the Test Guns and relocate to the next tube. Identify each leaking tube for repair with a
mark. While actual testing time is approximately 5-10 seconds per tube, this process time may
vary depending on verification of a tube leak or amount of time used to create stable applied air
pressure.
10. Repeat the previous steps explained here for subsequent tube leak inspection.
3. Installing Replacement Seals:
1. Replacement seals for the TLD 2500 Guns are furnished with matched size washers. All seals
and washers should be replaced on both guns at the same time.
2. Remove the lock nut from the end of the support shaft tube and place it to the side.
3. Remove the seal and washer set from the support shaft tube and dispose of if worn. Estimated
number of operations per seal and washer set before replacement is approximately 100-500 tubes
depending on conditions and operator.
4. Wipe down shaft and install replacement seal and washer on same shaft. If the dimensions have
changed, you may be required to replace the support shaft tube.
5. When replacing the lock nut (Fig. 1 & Fig. 2 Item 1) on the support shaft tube hand tighten.
Do not use a wrench or other mechanical tool. A small gap between the lock nut and the seal
washer is typical. The air cylinder stroke distance will compensate for that space.