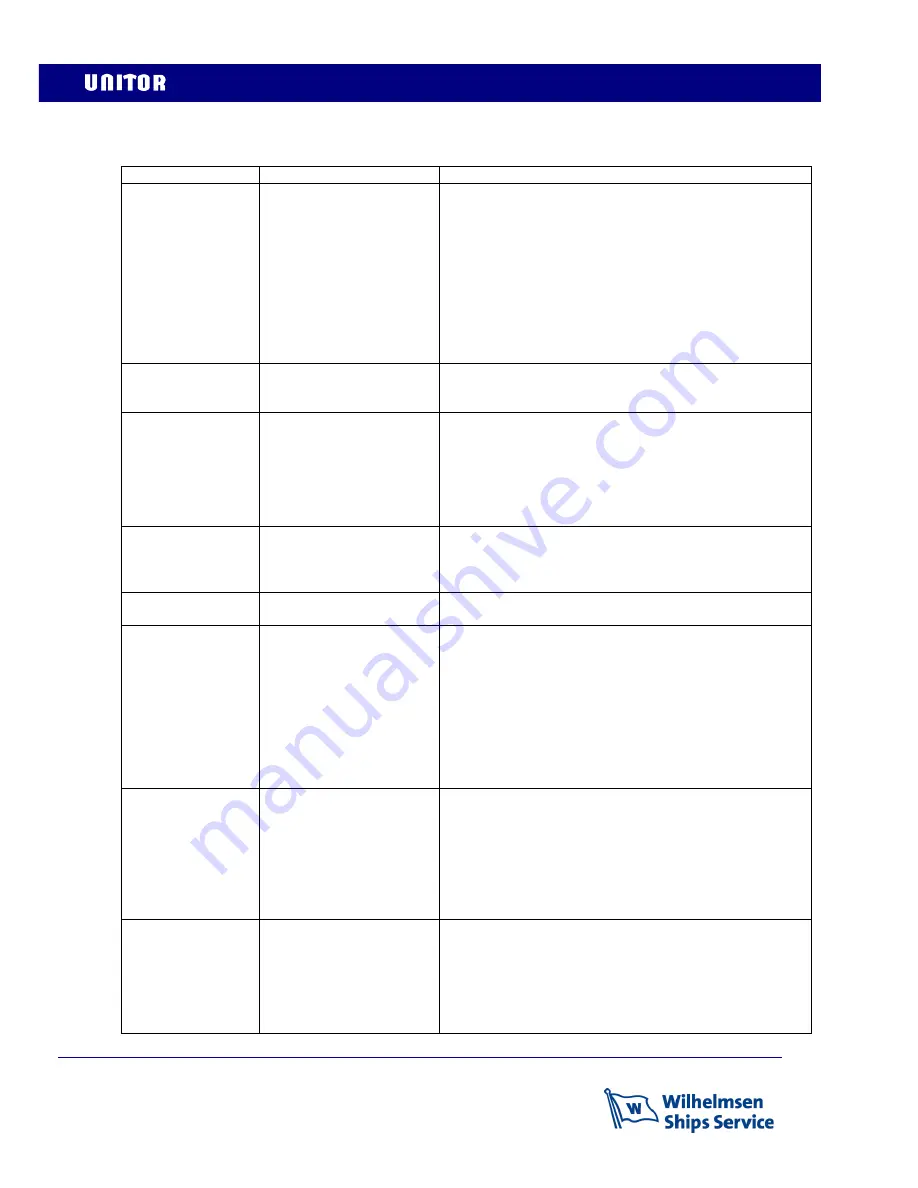
Revision date: 23 09 2014
Page 19 of 32
PROBLEM
CAUSE
SOLUTION
No output voltage
Check for a short circuit at
the DINSE plug with a
diode tester. A short
circuit may be caused by :
− damaged transil on the
snubber board;
− damaged diodes;
− damaged inverter;
− The inductive value of
the Power Transformer is
nill.
Unplug the machine. Remove the snubber board:
• check with a diode tester the status of the transil on the
snubber board (picture 2);
• check with a diode tester the status of the diodes;
• check the status of the power board (picture 4);
• The Power Transformer must be replaced.
Primary fuses blow
Settings have been set to
demand higher power
than available
Decrease the welding current / wire speed / voltage
settings
The welding is not
optimal.
− Spattering during
welding.
− Porosity in the deposit.
− Too narrow welding
seam (“dry arc”).
− Too wide welding seam
(“too hot weldpool”)
• Make sure welding polarity is correct.
• Decrease the voltage and check the gas emission from
the torch.
• Increase the wire speed and/or voltage.
• Decrease the wire speed and/or voltage.
The machine stops
welding and emits
an acoustic signal
(sound alarm).
The maximum current that
can be supplied by the
machine has been
exceeded
Decrease the value of the welding parameters.
Non optimal wire
welding start.
Spattering and crackeling
occurs on starting.
Decrease the wire speed setting or increase voltage
setting
No gas from the
solenoid valve
− Excessive gas
pressure.
− Damaged solenoid
valve wiring.
− The solenoid valve
control relay on the front
panel is damaged.
− Solenoid valve is
damaged
• Reduce gas flow setting.
• Unplug the machine, If break in a circuit, single out the
break and repair it. Make sure that the wiring contacts
are correctly inserted in the connectors.
• The logic front panel (pos 11) must be replaced.
• Should the operations carried out not have a positive
outcome, replace the solenoid valve (pos 35)..
Should the operations carried out not have a positive
outcome, try to replace the Toroidal Transformer (pos
21).
The torch button
does not work
− The amphenol board
(0042) cable is broken.
− The cable between the
euro connector and the
connector on front
panel.is broken
− The logic front panel
(pos 11) is damaged.
• The amphenol cable must be replaced.
• Check the connection between the Euro-connector and
pin 1/2 of the Amphenol connector.
- Then check the connection between the amphenol
connector and the motor board and between motor
board and front panel.
• The front panel must be replaced
The machine
always welds at
maximum current.
− The front panel is
damaged..
− The power board is
damaged.
− The shunt wires are
damaged or not correctly
inserted
Unplug the machine:
• The front panel must be replaced.
• The power board must be replaced.
• Connect the cables, or if damaged, replace them.