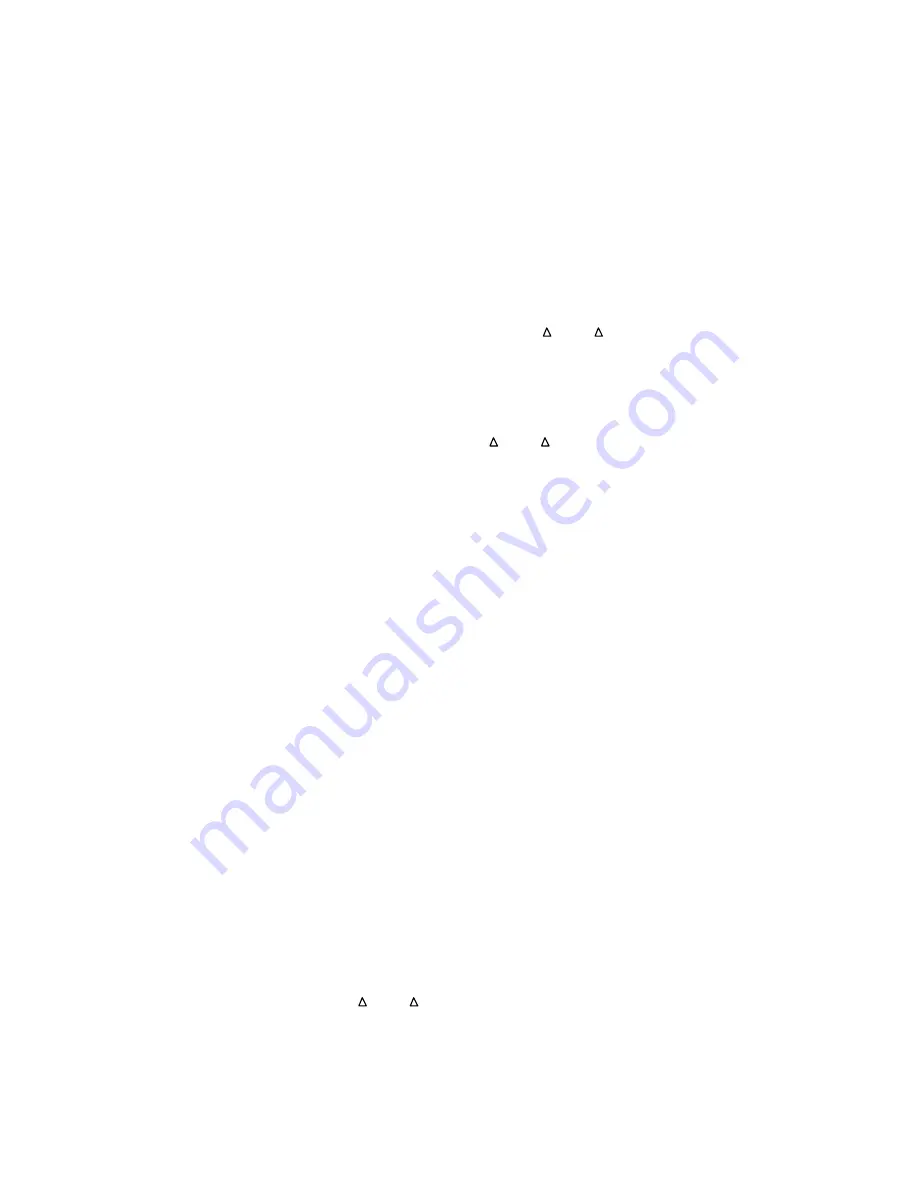
Communications wiring
Unit Ventilator
CARRIER CORPORATION ©2019
Integration Guide
All rights reserved
19
Manual Fan Speed Control
- When you use the controller with the optional SPT sensor, the automatic fan speed
operation may be overridden from the SPT sensor (if applicable). You can select any available motor speed or
automatic operation.
Unoccupied Fan Cycling
- When
Unoccupied Fan Cycling
is set to
Enable
(default), the controller operates the
equipment’s fan for 1 minute every hour during the unoccupied period. The fan operates at the lowest speed
Fan Speed Control - Electric Heat Override
- When electric heat is required and active, the control continuously
monitors the supply air temperature to verify it does not rise above the configured
Maximum Heating SAT Limit
[90°F (32.2°C) default]. As the SAT approaches the limit minus 10 °F (5.5 °C), the fan speed increases to
ensure the SAT remains below the limit. This provides the most quiet and efficient operation by running the fan at
the lowest speed possible.
Fan Speed Control - DX Cooling override
- When DX (direct expansion) mechanical cooling is required and active,
the control continuously monitors the supply air temperature to maintain the SAT at or above the configured
Minimum Cooling SAT Limit
[50°F (10°C) default] plus 5 °F (2.7 °C). When the SAT drops below this value,
the fan speed increases to prevent the SAT from dropping further. The fan operates at the lowest speed to
maximize latent capacity during cooling.
Fan Status
(Option) - The optional input can be configured as either an occupancy input or a fan status input. If
configured as fan status, the controller compares the status of the fan to the desired commanded state. When the
fan is commanded to run (ON), the fan status is checked and verified to match the commanded state. If the fan
status is not on, then a fan status alarm is generated after 1 minute and the equipment's MAD is disabled. If the
equipment has hydronic heat configured, the heating algorithm maintains the desired fan off setpoint.
Cooling
The Unit Vent operates mechanical cooling (one stage of DX, a modulating chilled water valve or a F&B damper
plus a 2-position water valve) to maintain the desired cooling setpoint. The cooling is controlled by the PI
(Proportional-integral) cooling algorithm and integrated with the modulating mixed-air damper control. The
required
Cooling Control Setpoint
is calculated by the controller and the cooling device is controlled to maintain
the
Supply Air Temperature
at this setpoint. This setpoint is compared to the actual supply air temperature and
determines valve or damper operation and staging control for DX.
The following conditions must be true in order for the cooling algorithm to run:
Cool Enable
is set to
Enable
Space temperature reading is valid
Supply fan must not be in alarm
For 2-pipe systems, the water temperature is suitable for cooling
Heat mode is not active
For DX, the 5 minute compressor time-guard timer has expired
Fire/Smoke Detector
(FSD) is
Normal
OAT > damper setpoint plus 3 °F (1.6 °C)/hr and damper output > 95% for 1 minute, or, OAT is NOT
suitable for cooling, or,
Damper Type
is not
Modulating
.